Чем комплектуют на заводе toyota
Как же делают «Тойоты»: все секреты японских мастеров (+видео)
Как же делают «Тойоты»: все секреты японских мастеров (+видео)
27.05.15 | Рубрика: Новости от потребителей, Тематические сюжеты. Просмотры: 1 023
Загрузка...Вы слышали такие слова, как андон, муда, каракури и пока-йоке? «Авто Mail.Ru» посетил завод Toyota и узнал о целой философии создания японских машин. Пока других производителей лихорадит от «кризисной чумы», Toyota пирует в Санкт-Петербурге: завод в Шушарах расширяет площади, наращивает мощности и собирается запустить RAV4!
Причина столь успешного развития завода лежит в производственной системе TPS (Toyota Production System), ключевые положения которой были сформулированы более 60 лет назад, а также философии Toyota Way — системе ценностей, поведенческих норм и методов, в основе которых лежат принципы уважения к людям (Respect for people), наставничества, командного духа и постоянного совершенствования (Kaizen). Что это такое — мы вам сейчас и расскажем.
Одна из целей «кайдзена» — повышение эффективности производства. Допустим, оператору неудобно брать деталь. Чтобы решить эту задачу, рабочая группа, следуя принципу Genchi Genbutsu, идет на место, чтобы увидеть реальную ситуацию своими глазами. Далее проводится детальный анализ, в ходе которого и выявляются все отклонения, например, комплектующие неудобно расположены, либо сам оператор делает ошибки. «Кайдзен» важен для людей, занятых рутинной работой, для них это возможность реализовывать себя. Таких рабочих руководство ценит порою выше, чем инженеров — практический опыт куда ценнее знаний профессионала, не работавшего на производстве.
-
Раньше при доставке бочек использовались тележки с плоским полом. Посетив завод во Франции, рабочие увидели, что тележку можно оборудовать направляющими роликами для упрощения погрузочных операций.
-
Изначально сотрудники инспекции жаловались, что им плохо видно, как работают фароомыватели. Решением проблемы стала установка зеркал.
-
Станцию подсборки потолка переместили к конвейеру. Для этого пришлось уменьшить размеры стеллажей и сделать подиум, чтобы они не выпирали в коридор. Теперь оператор не мучается с разгрузкой тележек, пересекая несколько раз проезжую часть и заставляя ждать водителей электрокаров.
Именно для этого и созданы «Кружки контроля качества» — группы сотрудников, предлагающие оптимизацию своего рабочего процесса. Каждый кружок качества состоит из 5-7 сотрудников одного цеха, а также наставника. Лучшие кружки регулярно посещают международные конференции в Японии и Европе, чтобы поделиться своими идеями с коллегами из других заводов. Потому что японский принцип Yokoten подразумевает обмен опытом и распространение информации как между сотрудниками одного предприятия, так и нескольких. И эта практика принесла плоды: по качеству и производительности российский завод уже обогнал английский.
-
Yokoten-центр с рацпредложениями. От каждого сотрудника руководство ожидает не менее одного рацпредложения в месяц. И даже если идея неуспешная, это все равно полезно для развития сотрудника — ему объяснят, почему ее не воплотили, и подскажут, в каком направлении мыслить дальше. За год накапливается более 10 тысяч идей.
Одним из результатов kaizen-деятельности является создание Karakuri — так в Японии называют механические куклы, работающие благодаря часовому механизму, противовесам, либо энергии текущей воды, пересыпающегося песка или пара. Эти принципы легли в основу разных механизмов, используемых на заводе, помогающих рабочим беречь силы и время. В идеале такое устройство не должно использовать силу и энергию извне, кроме той, что дается даром (сила тяжести, незначительная мускульная сила и т.д.).
-
В одну сторону тележка под весом груза движется под уклон. Как только груз снимут, она возвратится в исходное положение под действием противовесов.
-
Чтобы не надрывать спину человек встает на педаль, которая задействует механизм, создающий первоначальное усилие, позволяющее сдвинуть тележку.
Но вернемся к производству. Любая операция на конвейере выполняется в соответствии с понятием Jikotei Kanketsu — она обеспечивает «завершенность и качество, встроенное в процесс»: на каждый последующий этап передается только качественный продукт. Для этих целей служит метод Poka-yoke — это использование приспособлений, не позволяющих продолжать работу, если операция выполнена неверно или не до конца. А чтобы дефект был вовремя локализован и устранен, используется сигнальная система Andon — часть принципа интеллектуальной автоматизации Jidoka, позволяющей внедрять устройства, останавливающие работу при возникновении нарушений. В этом и заключается особенность производства «Тойоты» — нельзя передавать процесс с отклонениями на следующий участок и потом доделывать. Сотрудники обязаны доложить начальству о любом отклонении, неважно, дефект ли это или мелочь вроде упавшего инструмента. Ведь андон — эффективное средство для выявления проблемы и ее анализа (принцип Hansei). Вопреки слухам, в момент активации андона конвейер не останавливается. Если бригадир успевает решить все вопросы в пределах проблемного производственного участка, то конвейер едет дальше. В противном случае конвейер останавливается. Если на производстве возникают повторяющиеся проблемы, то начинается расследование с участием бригадира и других руководителей для выяснения причин и поиска решения.
-
Из-за активации андона 15-20 минут простоя сборочной линии в день — это норма, хотя сейчас в Шушарах простои занимают не более 5 минут — за это время рабочие 100-200 раз дергают «желтый шнур». За 8-часовую смену выпускается около 86 машин — каждые 5,5 минуты с конвейера сходит новый автомобиль. То есть ради поддержания принципов TPS жертвуют одной невыпущенной Camry.
Также у «Тойоты» существует многоступенчатая система внешнего контроля качества. Первый — это «критические точки», связанные с безопасностью, законодательными нормами, выбросами в атмосферу и резьбовыми соединениями — у каждого цеха они свои. Эти точки проверяются на всех автомобилях. Проверке кузовной геометрии подвергаются все навесные панели, а полностью кузов исследуется лишь у каждой двадцатой машины — это около 500 контрольных точек. Второй этап — это мини-инспекции в конце каждого производственного участка, контролирующие все изменения и отклонения в процессах производства. И, наконец, третий этап — это стандартная финишная инспекция каждого автомобиля перед отправкой на склад и короткий проезд по специальной дорожке с неровностями.
-
Каждый автомобиль проходит 5-минутный тест в дождевой камере, а каждый 80-й подвергается усиленной проверке в течение суток. Такой способ проверки консервативен, длителен, зато эффективен.
А как японцы избегают лишних затрат, простоев и перегрузок рабочих? Тут на помощь приходит принцип Heijunka — «выравнивание производства». Вот пример: любой автомобиль выпускается с разными моторами и комплектациями, значит, и время на сборку будет разным. А конвейер постоянно движется с одинаковой скоростью. Поэтому Toyota выстраивает все в такой последовательности, которая позволит выровнять среднее время на сборку. Огромный склад — это всегда серьезные финансовые потери и замороженные активы. Чтобы избежать их, склад нужно урезать до минимума, а все контейнеры с деталями сразу отправлять на разгрузку — и прямиком на конвейер. То есть и поставщик, и производитель работают по принципу Just in time — все детали должны поступать в нужное место, в нужном количестве точно в срок. А для реализации этого принципа используется карточная система Kanban.
Как вы поняли, любой поставщик «Тойоты» тоже должен работать по системе TPS. Учитывая растущие требования по локализации производства, «очеловечивание» российских производителей — настоящая головная боль для «Тойоты». Ведь даже в идеальных условиях требуется около 2 лет, пока поставщик освоит TPS. Сейчас у питерского завода есть перспективы сотрудничества только с Борским стекольным заводом.
-
Kanban-карта информирует о том, какая деталь, в каком количестве и где именно была израсходована. Как только работник цеха забирает коробку с деталями, он выкладывает эту карточку из коробки в специальный ящик. С определенной периодичностью эти карточки возвращаются в отдел логистики. Таким образом, логисты всегда знают, какие контейнеры надо разгружать и какие детали доставать.
-
Запущенный в 2014 году цех штамповки — это два пресса, производящие штамповку лишь лицевых панелей кузова: крыша, капот, багажник, боковины и двери. Стальной прокат для наружных панелей везут из Франции и Германии, а остальные компоненты кузова — из Японии.
-
На заводе говорят, что даже Брюс Ли отрабатывал движения на подобном тренажере. Согласно нормативу, 8 витков веревкой вокруг колышков нужно совершить за 6 секунд, однако, рекордсмены на заводе выполняют это упражнение за 3 секунды!
-
Сотрудник тренинг-центра устанавливает уплотнительную резинку weather strip — 4-5 секунд и она на месте! Вот, где требуется ловкость и эластичность рук.
-
Нашивки с изображениями флагов государств выдаются за прохождение обучения в тренинг-центрах заводов Toyota в других странах. Всех заводчан стараются подружить с английским языком — уже около 30-40% рабочих способны объясняться с иностранцами.
Рабочие места каждого сотрудника организованы по модели 5S — это пять принципов: Seiri («Сортировка» — разделение вещей на нужные и ненужные и избавление от последних), Seiton («Соблюдение порядка» — хранение вещей, позволяющее без труда найти их и использовать), Seiso («Содержание в чистоте»), Seiketsu («Стандартизация» — поддержание порядка), Shitsuke («Совершенствование» — формирование привычки точного выполнения установленных правил и технических операций). Все это развивает в сотрудниках дисциплину и культуру, позволяющую четко следовать более сложным производственным процессам. За чистотой и безопасностью на заводе следят строго. Сейчас в «Тойоте» недовольны подрядчиками, занимающимися возведением зданий для расширения производства — не соблюдается охрана труда строителей. В итоге заводчанам приходится тратить собственные ресурсы, идти на строительную площадку, наблюдать за тем как ведутся работы, выявлять риски, анализировать и предлагать решения. Еще один пример «кайдзена» и развития общества.
А как японцы боролись с нашим менталитетом? А нет никакого менталитета, есть лишь среда. Если создать вокруг человека здоровую атмосферу, то он будет нормально работать. Вообще в «Тойоте» стараются не наказывать, а разбирать проблемные ситуации. Выстраивание доверительных отношений между руководством и сотрудниками помогает быстро докопаться до сути проблемы. Именно поэтому текучка кадров не превышает 5% — в Шушарах уже появились «старожилы», работающие по 6-7 лет. Вообще усвоение системы TPS требует времени и усердия, работа на конвейере — это тяжкий и монотонный труд — за смену рабочий может сделать до тысячи тех же приседаний! Именно поэтому каждый день на заводе начинается с зарядки — разминкой проверяют состояние человека, можно ли его допустить к конвейеру или нет? Каждый сотрудник занимается, в среднем, 5-ю сборочными операциями, которые чередуются с определенной периодичностью — это чтобы рабочие не сошли с ума от монотонной деятельности. Зарплаты на заводе начинаются от 38 000 рублей, кроме того есть хороший соцпакет, частичная компенсация общежития и трансфер (работников вечерней смены везут фактически до дома).
-
В сборочном цехе не используют фартуки и коврики, защищающие ЛКП от повреждений. Это результат повышения культуры производства. Исключения составляют конкретные операции, где контакт с поверхностью неизбежен.
-
Питерский завод не блещет высокой автоматизацией, большинство операций выполняется вручную. Но в августе будет запущена автоматизированная линия main body line (сварка основной части кузова, бортов и крыши), а это около 40% всех сварочных операций. Линия будет использовать компактных роботов нового типа — эта технология является коммерческой тайной.
-
К 2016 году завод планирует нанять еще 800 работников. «Тойотовцы» не хотят брать ни бывших «джиэмовцев», ни кого-то еще с других автозаводов — все они «испорчены» другими методами работы, их куда сложнее переучивать, чем натаскать новичка.
Глоссарий
Kaizen — принцип, который подразумевает постоянное совершенствование.
Just in time («точно вовремя») означает поступление деталей, материалов или готовых изделий в нужное место, в нужном количестве, точно к назначенному сроку.
Jidoka («интеллектуальная автоматизация») — это один из основных принципов, означающий внедрение различных приспособлений (от самых простейших до сложных), которые позволяют останавливать работу оборудования при возникновении нарушения в процессе.
Genchi Genbutsu — один из основных принципов, применяемых всеми сотрудниками от операторов линий до руководителей компании. Смысл принципа заключается в том, что, для того чтобы в чем-то разобраться, необходимо пойти на место и увидеть реальную ситуацию своими глазами.
Kanban — система карточек или других элементов, позволяющая управлять партиями и планировать доставку деталей строго в соответствии с принципом «точно вовремя».
Andon — сигнальная система (шнур), проложенная вдоль линии конвейера. С ее помощью каждый оператор может и должен сообщить руководителю о возникших проблемах или любом отклонении в процессе. Руководитель принимает решение, возможно ли продолжить работу на движущемся конвейере или необходима остановка линии.
Karakuri — механические приспособления, работающие благодаря силе гравитации, разрабатываемые сотрудниками и внедряемые на производстве для оптимизации процесса и пространства.
Nemawashi — достижение консенсуса всех вовлеченных сторон перед принятием решения.
Muda — затраты, потери, отходы и другие издержки, которых можно избежать, совершенствуя процесс производства.
Muri — перегрузка рабочих, сотрудников или производственных мощностей.
Mura — неравномерность выполнения операции или прерывистый график выполнения операций.
Poka-yoke — метод предотвращения ошибок, подразумевающий использование приспособлений, которые не позволяют продолжить производственный процесс, если операция выполнена неверно или не до конца.
Heijunka — принцип выравнивания производственного графика, объемов производства и видов продукции, выпускаемых в определенный период времени, для организации бесперебойного и эффективного производственного процесса.
Jikotei Kanketsu — принцип построения процесса, обеспечивающий передачу на следующий этап производства только безупречно качественного продукта.
Monozukuri — принцип, означающий «искусство создавать качественные вещи». Использование в совокупности творческого потенциала и профессионального мастерства.
Автор: Петр Баканов, редактор Авто Mail.Ru
Метки:: 5S, Andon, Genchi Genbutsu, Hansei, Heijunka, Jidoka, Jikotei Kanketsu, Just in time, kaizen, Kanban, Karakuri, Monozukuri, Muda, Mura, Muri, Nemawashi, Poka-yoke, Respect for people, Toyota, Toyota Production System, Toyota RAV4, Toyota Way, TPS, Yokoten, Борский стекольный завод, Брюс Ли, завод Toyota в Шушарах, кайдзен, Кружки контроля качества, производство автомобилей, Тойота
www.battery-industry.ru
Уроки японского
В декабре текущего года в России под Санкт-Петербургом начнет работать завод Toyota. Накануне этого события Toyota Motor Corporation решила продемонстрировать группе российских журналистов принципы производства, внедряемые по всему миру
В Японии я случайно увидел по местному телевидению эпизод из сериала: герой-полицейский спешит к дому, где происходит убийство. Из спальни на втором этаже доносятся крики о помощи. Полицейский взламывает дверь, но, прежде чем ворваться внутрь, быстро снимает ботинки — входить в чужой дом в обуви в Японии не принято.
Данный пример иллюстрирует то, как скрупулезно японцы соблюдают традиции и нормы. Относится это и к производству автомобилей компании Toyota — строгое следование порой необычным для европейца правилам обуславливает успех предприятий этой компании.
Рывок на первое место
Итогов текущего года руководство компании Toyota ждет, можно сказать, с трепетом. Предполагается, что объемы производства японской корпорации достигнут почти 9,5 млн автомобилей. Если это произойдет, Toyota станет самым крупным в мире автопроизводителем и наконец-то обгонит своего основного мирового конкурента — концерн General Motors.
На протяжении всей своей истории компания Toyota Motor демонстрирует внушительный рост производства автомобилей. Основана она была в 1935 году как отделение первого в мире производителя автоматизированных ткацких машин — компании Toyoda Automatic Loom Works (кстати, фирменный знак автомобилей Toyota означает вовсе не какой-то самурайский символ, как до сих пор думают многие, а нитку, продетую через петлю). И практически все время существования, более 70 лет, несмотря на мировые кризисы, Toyota Motor удавалось поддерживать растущие объемы производства (см. график 1). Особенно впечатляет динамика в последние годы: за шесть лет с 2000-го до 2006 года выпуск автомобилей Toyota вырос более чем на треть — с 5,1 до 8 млн машин в год. При этом именно рост зарубежного производства — с 3,9 млн автомобилей в прошлом до 4,4 млн в этом году — позволит Toyota сделать рывок, который даст ей звание мирового автопроизводителя номер один.
Точно вовремя
Во всем мире Toyota принадлежит 64 автомобильных завода. География их расположения довольно обширна. Конечно же, предприятия японской компании есть в США, стране с самым крупным автомобильным рынком. Здесь работает девять заводов Toyota, в том числе самое крупное зарубежное предприятие компании в штате Кентукки с объемом производства 504 тыс. автомобилей в год.
Производство Toyota развивается в Канаде, Аргентине, Бразилии, Мексике, Франции, Великобритании, Чехии, Польше. Больше всего зарубежных заводов Toyota в Китае — их там в общей сложности десять. Toyota активно налаживает производство и в странах третьего мира: Таиланде, Индонезии, Индии, на Филиппинах. Есть заводы Toyota даже в Кении, Бангладеш, Вьетнаме. На родине Toyota принадлежит 12 предприятий.
Нам удалось попасть на один из самых крупных заводов — Tsutsuni. Оно расположено близ города Нагоя в местечке, которое так и называется японцами — Toyota City. Из ворот этого предприятия ежегодно выкатываются 470 тыс. новеньких автомобилей. При первом знакомстве с заводом Tsutsuni удивляет не столько объем, сколько число производимых моделей. На конвейере предприятия одновременно собирается шесть моделей: Camry, Premio, Allion, Wish, Prius, Scion, — причем каждая имеет еще несколько модификаций. Получается, что на производственной линии завода выпускается сразу несколько десятков разных машин.
Фото предоставлено компанией Toyota
Дотошные японцы подсчитали, что в среднем автомобиль состоит из 30 тыс. деталей. На заводе Tsutsumi все эти детали превращаются в один автомобиль менее чем за сутки — всего за 20 (!) часов. Особенно зрелищна начальная часть производства автомобиля — сварка основных деталей кузова. Здесь (впрочем, как и на предприятиях многих других компаний) этот процесс полностью автоматизирован. Более 500 роботов абсолютно самостоятельно приваривают 400 кузовных деталей к каждому автомобилю в трех тысячах точек. Выглядит все это завораживающе и напоминает сцены из фильма «Терминатор». Сваривающие роботы ждут свою «жертву» — кузов очередного автомобиля. Когда он подъезжает на конвейере, роботы замирают, как бы приглядываясь (на самом деле автоматика считывает штрих-код изделия с информацией, в каких точках нужно осуществлять сварку), а потом вдруг набрасываются на заготовку. Слышен скрежет металла, отовсюду летят искры. Через пару десятков секунд все кончено — роботы удовлетворенно застывают на месте, а сваренный кузов продолжает свое путешествие по сборочной ленте.
Поодаль виднеется тележка с комплектующими. Она едет… самостоятельно. Встроенный оптический датчик следит за начерченной на полу цеха линией, и тележка сама привозит детали, куда нужно. Кстати, о деталях. Нам показывают, как на производстве действует знаменитая тойотовская система just-in-time («точно вовремя»). Детали для сборки на конвейере доставляются не со склада, а прямо с грузовиков поставщиков, которые, в свою очередь, точно вовремя подъезжают к заводу.
— А если поставщик опоздает? — задаем мы вопрос в традиционном российском стиле.
— Это как, опоздает? — удивляются встречающие.
— Ну, там, случится у него что-то, машина не заведется, водитель заболеет.
— Найдут замену водителю и машине.
— Ну а если не смогут найти?
Японцы пожимают плечами. Они не понимают, о чем мы говорим.
Канбан
При ближайшем рассмотрении выясняется, что система just-in-time основывается на обороте маленьких бумажек, название которых уже вошло в лексикон других языков: канбан. Канбан — это, по сути, небольшая бирка, которая крепится к каждой поставляемой на завод детали. Toyota начала внедрять канбаны еще в 1950-х годах. Образцом послужила система в американских супермаркетах. Наблюдательные японцы отметили принцип работы супермаркетов в США: с купленной вещи снимали бирку и отправляли ее (или информацию с нее) поставщику, с тем чтобы он прислал точно такой же продукт. Таким образом, в магазин поставлялось ровно столько продукции, сколько было куплено. «Почему бы не использовать такой же принцип поставок у нас на производстве?» — задались вопросом на автогиганте.
Часть персонала нового завода Toyota в России уже прошла обучение в Японии
Сегодня поставки на завод осуществляются по такой схеме: пошла деталь для сборки — бирка, или канбан, с нее передается в отдел работы с поставщиками, где у последнего заказывается точно такая же деталь, которая может прийти на следующий день. В результате происходит колоссальная экономия на складских помещениях и оптимизируется работа с поставщиком. Данная система работает десятилетиями, причем очень эффективно, и на Toyota даже вполне серьезно замечают, что «блок цилиндров, отлитый на заводе Kamigо (смежном предприятии компании) утром, работает в готовом автомобиле вечером». И еще на заводе говорят — не то в шутку, не то всерьез, — что тележке с деталями на конвейер уступает дорогу сам президент компании, потому что задержать детали не может никто и ничто.
Дерни за веревочку…
Особая философия на заводах Toyota выработана в отношении контроля качества производства. Почти возле каждого рабочего места можно заметить свисающую сверху обычную веревочку.
— За веревочку нужно дернуть, если рабочий допустил или увидел хоть малейший брак в сборке или отход от стандартов производства, — отвечают нам на наши вопросительные взгляды.
— И что происходит после того, как дернут хотя бы за одну веревочку?
— Останавливается весь конвейер. Мы убеждены, что, если возникает малейший брак, процесс производства должен быть остановлен для устранения непорядка на месте.
Вообще японцы не очень понимают европейскую систему контроля качества. «Мы были на заводе Volkswagen, — рассказывает нам один из топ-менеджеров Toyota Motor Corporation. — Там в конце отдельных линий или этапов сборки существуют посты контроля качества. На этих постах проверяется качество работ, и, если что-то не так, автомобиль посылают на доработку. У нас процесс выстроен по-другому: контроль качества, по сути, осуществляется на каждом рабочем месте. Лучше предотвращать появление брака или исправлять его в самом начале, чем потом тратить средства и время».
В борьбе за высокое качество на заводе Toyota главную роль отводят персоналу. Не менее важный момент — то, что японцы называют «дзидока»: высокий уровень автоматизации, но построенный опять же на человеческом факторе. По словам руководства Toyota, на предприятии очень много внимания уделяют именно умелой интеграции труда роботов и человека. Человек постоянно следит за качеством работы автоматических систем. Впрочем, иногда происходит и наоборот. На заводе Toyota есть специальное внедрение, пока-ёке — автоматизированное устройство, призванное не допускать появления брака. Техника просто не позволяет работнику совершить ошибку. Допустим, на участке установки глушителей на заводе имеется оптический датчик. Он следит за тем, чтобы глушитель был поставлен правильно. Если работник по ошибке перевернул деталь и начал как-то не так ее устанавливать, пока-ёке заблокирует работу сварочного аппарата в руках рабочего.
Музыкальная сборка
Борьба за качество продукции на заводах Toyota связана в первую очередь с повышением сознательности и профессиональных навыков каждого отдельно взятого рабочего. Это сразу заметно при посещении Toyota Global Production Centre — места, где проходят обучение рабочие заводов Toyota, причем как японских, так и зарубежных.
Уже на пороге видно особое почитание традиций. Заходя в центр, каждый обучающийся должен пройти через «ворота безопасности», которые внешне очень похожи на Ворота в бесконечность, стоящие у каждого синтоистского храма в Японии. Проходя через них, рабочий должен подумать о технике безопасности и таким образом привести мысли в порядок.
Фото предоставлено компанией Toyota
Обучение в центре начинается не с описания алгоритма выполнения работы, а с пояснения, для чего конкретно предназначается та или иная операция и что может повлечь за собой ее некачественное исполнение. Например, тренер на этапе сборки автоматической коробки передач наглядно показывает, что будет, если допустить отклонения в установке некоторых деталей: гидравлическая жидкость перестает циркулировать в коробке, и вся трансмиссия моментально выходит из строя. А на следующем стенде рабочих учат прикручивать шурупы не только на глаз, но и… на звук. Ученикам демонстрируют аудиозапись того, какие звуки при правильном закручивании издает шуруп. Если что-то идет не так, то и звук не такой. Неподалеку замечаем работающий метроном. Обучение некоторым операциям происходит при помощи этого инструмента. Метроном задает такт работе, в течение каждого такта рабочий должен успевать закручивать, допустим, по одной гайке.
Специалисты центра предлагают нам попробовать выполнить некоторые учебные операции. За 25 секунд нужно надеть на конусы с разным сечением шесть болванок. Вроде бы задача несложная. Однако с ней поначалу никто не справляется — узкие болванки постоянно застревают и не хотят надеваться на конусы. Позже нам объясняют, что кисть руки при этой операции нужно держать под особым углом, а также желательно не прикладывать излишнего усилия к детали, тогда она сама легко станет на место. После такого инструктажа дело идет значительно лучше.
Недавно здесь проходили обучение 90 человек из России. «Это очень способные ребята, они хорошо работают в команде», — отзываются о российских специалистах в обучающем центре. Неподалеку видим след, оставленный нашими соотечественниками на предприятии. Выпускники центра имеют право сделать памятную надпись на специально отведенном для этого месте. Бразильцы, скажем, написали что-то про непобедимый бразильский футбол. А русские преисполнены гордости за самих себя: «Пусть плачут те, кому мы не достались (BMW, Ford, Nissan)!» — написано размашистым почерком.
На заводе под Санкт-Петербургом, по словам представителей российского офиса Toyota Motor Company, будут работать 400 российских рабочих. Отбор кандидатов был очень жесткий. Тойотовцы утверждают, что их отдел кадров отсмотрел несколько десятков тысяч претендентов и в среднем на завод попал один из ста человек.
Вообще во время посещения завода и встреч с топ-менеджерами Toyota было заметно, что к делегации из России в компании относятся очень трепетно. Сегодня российский рынок играет заметную роль для всей Toyota Motor Company. Он уже сейчас самый большой в Европе и входит в десятку крупнейших национальных рынков продаж машин Toyota в мире. А к концу этого года Россия должна перепрыгнуть на шестое место в списке самых значимых для Toyota стран.
По словам Йошимаса Ишии, управляющего менеджера Toyota Motor Corporation, компания рассчитывает за текущий год увеличить объемы поставок в Россию в полтора раза и продать 150 тыс. автомобилей. На заводе же под Санкт-Петербургом Toyota планирует собирать модель бизнес-класса Toyota Camry пока в количестве 20 тыс. автомобилей в год.
На выходе из обучающего центра Toyota крупными буквами выведено слово «Кайзен». «Кайзен» — еще один производственный принцип, который благодаря Toyota стал интернациональным понятием. Значение этого слова — «постоянное совершенствование». «Да, наши машины хороши, но мы должны делать их еще лучше», — говорят на заводе Toyota. Что ж, постоянное совершенствование — хорошая цель для автопроизводителя номер один в мире. Впрочем, согласно традиционной японской философии это вообще смысл жизни каждого человека.
Токио-Нагоя-Москва
expert.ru
Как делают автомобили Toyota на заводе в Санкт-Петербурге? — журнал За рулем
Рынок падает, а Toyota увеличивает мощности своего завода в Санкт-Петербурге и готовится освоить выпуск новой модели. В чем здесь секрет?
01
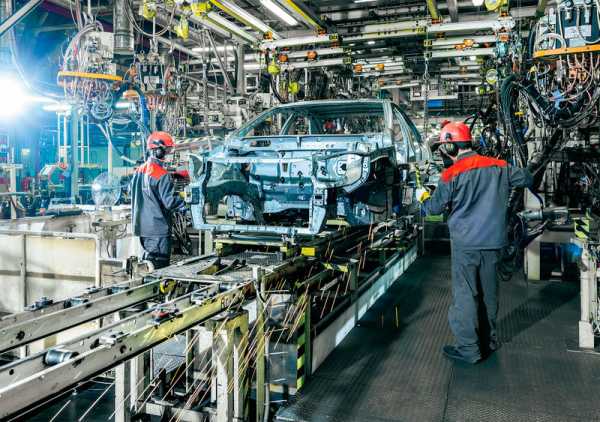
Материалы по теме
Через дорогу от тойотовского завода — предприятие концерна General Motors. В начале апреля, уже после новостей об уходе марок Chevrolet и Opel из России, смотришь на него по-другому. Служебная стоянка практически пуста, зато площадка готовой продукции битком забита. Производство остановлено, дилеры распродают остатки, которых хватит, видимо, до конца года. Уныние.
А у японцев блеск в глазах и планов громадьё. К концу текущего года питерский завод «Тойоты» прирастет мощностями и будет способен выдавать 100 тысяч машин в год вместо нынешнего потенциала в 50 тысяч. При том что в 2014 году даже действующие мощности использовались не полностью — было собрано чуть больше 36 тысяч Camry. Секрет прост: в начале следующего года к Camry присоединится кроссовер RAV4, причем уже в рестайлинговой версии.
Почему именно RAV4? Японцы посмотрели на меня как на инопланетянина: «Это же наш бестселлер!». В самом деле, Camry, оставаясь бессменным лидером класса D, в объеме продаж в 2014 году уступила «рафику» — пусть скромные три с лишним тысячи штук, но всё же.
02
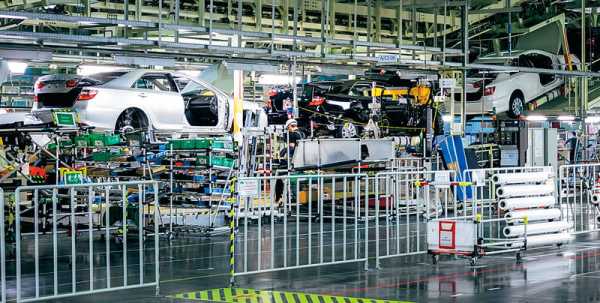
По состоянию на начало апреля завод Тойоты в Шушарах не останавливался и не планирует это делать, равно как и сокращать кого-либо из 1850 сотрудников, — хотя продажи автомобилей Toyota в первом квартале 2015 года сократились на 27,1% по сравнению с аналогичным периодом прошлого года. Впрочем, на фоне проблем других компаний это еще сносно. Для сборки кроссовера RAV4 дополнительно наймут 800 рабочих. А через дорогу, на заводе GM, персонал увольняют практически полностью: 400 человек согласились на компенсацию в семь месячных окладов, еще семьсот надеются получить двенадцать зарплат. К слову, Toyota не планирует «подбирать» чужих. При строгих фирменных требованиях к качеству работы проще обучить людей с нуля, чем переучивать.
По состоянию на начало апреля завод «Тойоты» в Шушарах не останавливался и не планирует это делать, равно как и сокращать кого-либо из 1850 сотрудников, — хотя продажи автомобилей Toyota в первом квартале 2015 года сократились на 27,1% по сравнению с аналогичным периодом прошлого года. Впрочем, на фоне проблем других компаний это еще сносно. Для сборки кроссовера RAV4 дополнительно наймут 800 рабочих. А через дорогу, на заводе GM, персонал увольняют практически полностью: 400 человек согласились на компенсацию в семь месячных окладов, еще семьсот надеются получить двенадцать зарплат. К слову, Toyota не планирует «подбирать» чужих. При строгих фирменных требованиях к качеству работы проще обучить людей с нуля, чем переучивать.
Седан локализовали первым потому, что любимцу чиновников нужно было сохранить право участвовать в государственных тендерах на правах «российского» автомобиля. RAV4 — выбор обычного покупателя, частника.
А на Дальнем Востоке Toyota собирает Land Cruiser Prado, который правит бал в сегменте больших вседорожников. Это главная составляющая успеха — переносить в Россию производство не всех машин подряд, а самых успешных. Скромные Corolla и Auris, затерявшиеся среди конкурентов, по этому критерию явно не проходят. А вот внушительные Highlander и Land Cruiser 200, думаю, есть смысл познакомить с российским конвейером.
Степень локализации питерского производства пока сравнительно невелика. При запуске в конце 2007 года российская доля в себестоимости Camry составляла лишь 10%, в 2011‑м она достигла 15%. В прошлом году в Шушарах открыли цеха штамповки внешних кузовных панелей и производства пластиковых деталей, а смежник «Тойоты» компания Boshoku начала здесь же выпускать сиденья и обшивку дверей — и степень локализации выросла до 30%.
03
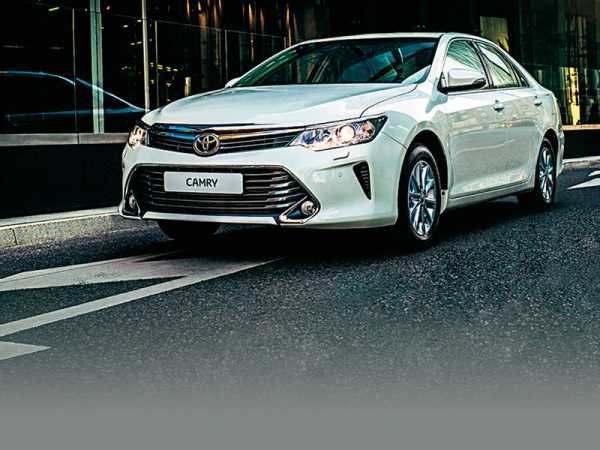
В середине марта на заводе Toyota начали собирать Camry с новым двухлитровым мотором и шестиступенчатым автоматом. Японцы полагают, что эта версия привлечет более молодых покупателей, переросших седаны С‑класса. Доля двухлитровых версий в общем объеме продаж Camry должна составить около 20%.
В середине марта на заводе Toyota начали собирать Camry с новым двухлитровым мотором и шестиступенчатым «автоматом». Японцы полагают, что эта версия привлечет более молодых покупателей, переросших седаны С‑класса. Доля двухлитровых версий в общем объеме продаж Camry должна составить около 20%.
Правда, локализация вовсе не главный показатель рыночного успеха, как иногда это представляют в прессе. Скажем, у автомобилей Chevrolet Cruze и Opel Astra, которые собирались на соседнем заводе, уровень локализации достигал 25% — но не помогло. Подозреваю, что GM подкосил нескромный рост цен при обвале рубля, в то время как некоторые конкуренты (и Toyota в их числе) предпочли затянуть пояса и поступиться частью прибыли.
Уверенности «Тойоты» в сложившихся обстоятельствах можно только позавидовать. А General Motors, надеюсь, учтет ошибки прошлого при возвращении. В том, что оно состоится, я не сомневаюсь.
Экскурсия
Toyota впервые пригласила журналистов на завод, работающий с конца 2007 года. Ничего сенсационного я не увидел, но отметил несколько нюансов, передающих характер предприятия
Ошибка в тексте? Выделите её мышкой! И нажмите: Ctrl + Enter
www.zr.ru
восточная философия и популярный бренд
В конце июля этого года компания Toyota Motor объявила о выпуске своего 200-миллионного автомобиля. Впечатляющий результат дает повод обратиться к истории этого японского автогиганта, отмечающего 75-летний юбилей со дня своего официального создания, и попытаться понять - в чем же все-таки заключается феномен Toyota?
На сегодняшний день Toyota Motor - один из ведущих автопроизводителей, занимающий 8 место в рейтинге 500 крупнейших мировых компаний (1). Toyota выпускает более 7 млн. автомобилей в год, а это значит, что каждые несколько секунд с конвейеров ее завода сходит новая машина. На предприятиях компании по всему миру трудится примерно 300 тысяч человек. Но цифры все-таки не главное: прежде всего, Toyota Motor – это яркий пример знаменитого «японского экономического чуда», образец успешного менеджмента и создатель новой производственной философии.
От ткацкого станка до автомобиля Lexus
История компании Toyota начинается в 1930-ых годах. До этого времени собственной автомобильной промышленности Япония не имела вообще, хотя американские компании General Motors, Ford и Chrysler строили на ее территории свои сборочные заводы. В 1933 году Сакичи Тойода, глава текстильной компании Toyoda Automatic Loom Works Ltd, открыл новое отделение в своей компании, которое возглавил его сын - Кииширо Тойода. Оно должно было заниматься производством легковых и грузовых автомобилей. Всем известный логотип Toyota - это стилизованная ткацкая петля, напоминающая о том, что нынешний автогигант зародился в компании по производству текстильного оборудования.
Первые модели автомобилей были не слишком удачными, однако Кииширо Тойода продолжал вкладывать деньги в производство. Правительство Японии поддерживало его инициативу, и фабрика в городке Коромо, где разместилось основное производство, быстро разрасталась. Вместе с ней рос и город, который со временем стали называть Тойота-сити. Toyota Motor Co. была основана в качестве самостоятельной компании в 1937 году - это и считается официальной датой ее создания. Вера Кииширо Тойоды в успех его детища была так велика, что он пожертвовал все собственные сбережения на строительство нового завода Toyota Motor в Хонше, вступившего в строй в 1938 году. Кстати, интересный факт - почему компания называется «Тойота», а не «Тойода»? Дело в том, что для того, чтобы написать иероглифами слово Toyoda, приходилось делать такое количество движений кисточкой, которое считалось "несчастливым". По этому поводу в руководстве фирмы шли споры, пока, наконец, не было принято название Toyota, производящее более благоприятное впечатление на покупателей - написанное катаканой, то есть японской слоговой азбукой, оно как раз состоит из 8 черточек, а число 8 считается в Японии счастливым.
Во время Второй мировой войны Toyota выпускала исключительно военные грузовики. Из-за жесткого дефицита в тогдашней Японии их делали в самых упрощенных вариантах, например, с одной фарой. В послевоенный период американские оккупационные власти разрешили продолжать выпуск грузовиков, а вот возобновить производство легковых машин удалось намного позже.
Кииширо Тойода скончался в 1952 году, когда начался настоящий расцвет созданного им детища. В отличие от других японских автомобильных фирм, Toyota не покупала лицензий у западных компаний, а активно разрабатывала собственные оригинальные конструкции. Вскоре компания вышла на мировой рынок - в 1957 году с конвейера сошла Toyota Corona, ставшая первым японским автомобилем, экспортируемым в США. Toyota Motor начала расширяться быстрыми темпами в 1960-ые годы, когда было организовано массовое производство ее автомобилей за пределами Японии. Одним из главных событий в истории компании можно считать появление в 1980-ых годах такой марки, как Lexus - подразделения Toyota, созданного для выхода на рынок автомобилей высокого класса. До этого Япония ассоциировалась с небольшими, экономичными и недорогими автомобилями, но с появлением Lexus в секторе роскошных дорогих машин положение изменилось.
В 2009 году компания завершила финансовый год с убытками – впервые с 1950 года. Однако в мае 2012 года Toyota вырвалась на первое место среди автопроизводителей, продав за первый квартал почти 2,5 млн. машин и обогнав таких автогигантов, как Volkswagen и General Motors. Этот факт весьма символичен - он доказывает, что японский автопром смог восстановиться после сокрушительного землетрясения и цунами 2011 года. (2)
В России автомобили Toyota пользуются устойчивой популярностью. Наша страна входит в десятку крупнейших для компании рынков и занимает первую позицию по объемам продаж автомобилей Toyota и Lexus среди европейских стран.(3) В 2007 году был открыт завод компании Toyota Motor в Санкт-Петербурге, на котором трудится примерно полторы тысячи человек. За четыре года предприятие выпустило более 45 000 автомобилей. Планируется, что в сентябре 2012 года на заводе будет запущена вторая смена, а число сотрудников возрастет до 1750 человек. (4)
Как устроена компания: кэйрэцу
Toyota - наглядный пример японского экономического чуда. Всего за несколько десятилетий компания добилась впечатляющих результатов, вырвалась в лидеры мирового автопрома и превратилась в образец реализации нового управленческого мировоззрения. Причин тут несколько, и главная, пожалуй, заключается в том, что Toyota не просто компания и не просто бренд - это еще и целая философия.
Для начала следует отметить, что характерной особенностью японской экономики является практика группирования - установления между предприятиями устойчивых долговременных связей, на которой основывается вся система деловых отношений в стране. Такие объединения банков, крупных промышленных компаний со средними и мелкими фирмами-поставщиками называются кэйрэцу. Это весьма эффективная форма интеграции бизнеса. Стержнем, объединяющим компании, входящие в кэйрэцу, являются производственные связи, ориентированные на нужды головной фирмы.
Toyota Group - это группа компаний, использующих бренд Toyota. В отличие от большинства японских кэйрэцу, ведущая компания в группе не банк, а Toyota Motor Corporation. Это один из наиболее ярких примеров жесткой организации вертикального типа, основанной на высокой степени зависимости субподрядных предприятий от головной фирмы. Поставщики и их субподрядчики вовлекаются в производственный процесс центральной фирмой, получая от нее конкретные задания по объему и срокам поставок, и даже по стоимости заказанных комплектующих изделий. Одновременно центральная фирма берет на себя финансовую поддержку поставщиков, оказывает им помощь в решении организационных и технических проблем. Общее число субподрядных фирм Toyota превышает 47 тысяч, из них около 170 фирм относятся к субподрядчикам первого уровня, около 5, 5 тысяч - к субподрядчикам второго уровня и около 42 тысяч - к субподрядчикам третьего уровня. (5) Вся эта система работает очень четко и слаженно.
Производственная философия
Один из главных принципов деятельности компании Toyota - «кайдзен». В японском языке это слово означает «непрерывное совершенствование». Философия кайдзен предполагает, что наша жизнь в целом, как общественная, так и частная, должна быть ориентирована на постоянное улучшение. Для японской ментальности вообще характерна вера в бесконечные возможности совершенствования. Как гласит пословица: «Если вы не встречались с другом три дня, присмотритесь получше, и вы увидите, что в нём изменилось». Западный менеджмент привержен инновациям - масштабным, кардинальным изменениям для достижения технологических прорывов. Что же касается принципа кайдзен, то он характеризуется малыми затратами, малыми рисками и обеспечивает пусть медленный, но неуклонный прогресс, который оправдывает себя в долгосрочной перспективе.
На принципе кайдзен основано и самое выдающиеся достижение компании Toyota - ее производственная философия, которую еще называют производственной системой Toyota (TPS). TPS - новая ступень в развитии эффективного бизнеса после системы массового производства, которую изобрел Генри Форд, и одна лучших на сегодняшний день систем управления производственными процессами. Ее целями являются:
- уменьшение различных потерь: оптимизация количества расходуемых материалов, необходимых перемещений, используемого инструмента и т.д.;
- достижение равномерной загрузки производства, исключающей как пиковые нагрузки, так и простои, с помощью поминутного планирования, постоянного визуального контроля и четкой стыковки последовательных производственных операций;
- контроль статуса выполнения и времени, затрачиваемого на каждую операцию, т.е. стандартизация каждой отдельной операции и производственного процесса в целом.
Производственная система Toyota охватывает все этапы производства и основывается на минимизации издержек, поиске наиболее эффективных методов работы и многолетних непрерывных улучшений производственного процесса. Тайити Оно, основатель TPS , писал: «Все, чем мы занимаемся - это следим за временем между размещением заказа потребителем и получением денег за выполненную работу. Мы сокращаем этот промежуток времени, устраняя потери, которые не добавляют ценности». (6) В основе производственной системы Toyota лежат сочетание системы Генри Форда, создателя поточного конвейера, и идей Фредерика Тейлора, который первым обратил внимание на эффективность отдельных процессов массового производства и необходимость устранять потери на каждом этапе.
Основу производственной системы Toyota составляют следующие принципы:
«Just in time» («Точно вовремя»). Это означает производство нужного вида изделий в нужном количестве и в нужное время, то есть в ходе каждого процесса создается только то, что требуется для следующего этапа в непрерывном производстве. Например, в процессе сборки автомобиля необходимые для этого детали должны поступать к конвейерной линии в определенное время и в точно рассчитанном количестве. Если система «точно вовремя» действует на всей фирме, она позволяет устранить становящиеся ненужными запасы и склады материалов.
«Kanban» (Система «канбан») Для соблюдения принципа «точно вовремя» в компании Toyota используется уникальный метод снабжения производства деталями, известный как канбан. По своей сути он является информационной системой, позволяющей оперативно регулировать количество продукции на различных этапах процесса. Система канбан основана на эффективном обмене информацией между отделом логистики и операторами производства. За каждой деталью закреплена карточка с ее номером, названием, информацией о получателе. Взяв деталь, оператор вынимает карточку канбан и оставляет ее в специальной коробке, которые в определенное время собираются сотрудникам отдела логистики. Проанализировав собранные карточки, отдел производственного контроля получает точную информацию о количестве, типе деталей и времени поставки их на линию. По такому же принципу на производство доставляются детали от поставщиков. Карточки циркулируют как внутри предприятий Toyota, так и между корпорацией и сотрудничающими с ней компаниями, а также на предприятиях филиалов. Таким образом, карточки «канбан» содержат информацию о расходуемых и производимых количествах продукции, что позволяет обеспечивать производство по принципу «точно вовремя».
«Jidoka» («Дзидока» - интеллектуальная автоматизация, или автономизация)
Дзидока – важнейший элемент производственной системы Toyota. Это внедрение различных приспособлений для оборудования, от простых до самых сложных, которые позволяют выявлять какие-либо проблемы и при необходимости останавливать работу. Принцип дзидока обеспечивает встраивание качества в ходе всего производственного процесса. Оборудование наделяется способностью отличать качественные детали от дефектных самостоятельно, без участия оператора. В результате отпадает необходимость постоянного наблюдения за станками, а это, в свою очередь, ведет к повышению производительности труда. Дзидока означает автоматизацию с человеческим интеллектом - пожалуй, это наиболее краткое и содержательное определение термина. Интересно, что принцип дзидока был заложен человеком, с которого начинается история компании Toyota. Сакичи Тойода, отец Кииширо Тойоды, в свое время изобрел ткацкий станок, который сам останавливался всякий раз, когда обрывалась нить. Это изобретение легло в основу одного из важнейших постулатов современной производственной системы Toyota.
«Genchi genbutsu» («Генчи генбуцу») - еще один важный принцип, который предполагает, что для понимания ситуации или проблемы необходимо лично, на месте, изучать процесс и результат производства. Это принятие решений, основанное на фактах, а не на мнениях: необходимо обращаться к истокам проблемы, чтобы ликвидировать ее и добиться поставленной цели. Данный принцип применяется в работе всеми сотрудниками Toyota - от операторов линий до руководителей компании, поскольку только знание реальной ситуации позволяет обеспечивать высокий уровень качества продукции, соблюдать необходимые сроки и объемы производства и контролировать расходы.
Производственная система Toyota, которую часто называют бережливым производством (Lean production), сегодня в моде. В мире существует множество компаний, стремящихся ей подражать. Подобные системы выстроили у себя не только соперники Toyota - Chrysler, Daimler, Ford, Honda, General Motors, но и многие компании, работающие в других отраслях, а также магазины, рестораны, предприятия коммунального обслуживания, больницы и почтовые службы. Для повышения производительности они применяют те же подходы, правила и управленческие методики - или, по крайней мере, пытаются применять.
Но, как известно, ничто не совершенно, и TPS тоже имеет определенные недостатки, в чем можно было убедиться на примере недавних событий. Мощное землетрясение и последовавшее за ним цунами в марте 2011 г. нанесли сильный удар по экономике Страны Восходящего Солнца и серьезно сказались на японском автопроме. Продажи Toyota в марте 2011 г. сократились на 30% по причине дефицита комплектующих, производство которых пострадало из-за катаклизма. В результате японские сборочные предприятия были загружены лишь наполовину, а зарубежные — на 40%. (7) Поскольку производственная система Toyota подразумевает малое количество складских запасов, и каждая деталь подается для сборки ровно тогда, когда она нужна, то в итоге компания понесла ощутимые потери. Но, конечно, надо учитывать и тот факт, что никто не мог предсказать масштабов подобной катастрофы.
«Качество, встроенное в процесс»
В производственной системе Toyota особую роль играет контроль качества продукции. В его основе тоже лежит принцип кайдзен, то есть идея постоянного, непрерывного совершенствования. В традиционных производственных системах качество выполненной работы проверяют только по ее завершении, однако TPS предусматривает контроль над качеством на каждом этапе производства. Эта методика называется «Качество, встроенное в процесс» . Именно благодаря ей на производстве допускается лишь 5 -10 дефектных изделий на 1 млн. штук. В отдельных случаях рабочие имеют право остановить конвейер, более того - сотруднику, который обнаружил неполадку, выплачивается премия. (8) В идеале любой дефект должен быть устранен до того, как продукция перейдет на следующий этап обработки, что уменьшает количество дорогостоящих доделок и повышает ответственность работников.
На предприятиях Toyota активно работают «кружки качества». Это добровольные объединения, которые вовлекают рабочих в деятельность по повышению качества продукции, снижению уровня травматизма и решению других производственных вопросов. Кружки качества появились в 1962 г. в Японии и позднее получили широкое распространение во многих странах мира. Как правило, это группы из 6-12 сотрудников, которые регулярно встречаются для того, чтобы обсуждать и решать разнообразные производственные проблемы, прежде всего те, которые влияют на качество труда. Однако результаты деятельности кружков не исчерпываются прямым экономическим эффектом, гораздо более важен косвенный эффект - создание корпоративного духа и особого морально-психологического климата. Считается, что «кружки качества» сыграли важную роль в создании японского экономического чуда.
В наше время фраза «японское производство» сама по себе стала синонимом высокого качества, но, тем не менее, без ошибок не обходится и здесь. В 2010 году прошли массовые отзывы дефектных автомобилей в США и других странах мира, связанные с проблемами непреднамеренного ускорения. В 2011 году компания Toyota также отозвала более 14 млн. моделей своих машин. Дефекты были обнаружены во всем автомобиле, начиная от бракованных ковриков и заканчивая ошибками тормозного программного обеспечения и неработающих стоп-сигналов.(9) Компания открыто признает свои ошибки и стремится делать все, чтобы их исправить.
Кадры решают всё.
Для управленческой модели компании Toyota в целом и системы управления персоналом, в частности, характерна особая философия, в основе которой лежит ориентация не на технику и не на финансы, а, прежде всего, на людей.
По мнению некоторых исследователей, если коротко сформулировать суть стратегии Toyota, главная ее задача - выращивание человеческого капитала. Это предполагает атмосферу доверия и сотрудничества, поддержку и помощь, снятие барьеров между подразделениями. В компании поощряется инициатива и возможность каждого сотрудника участвовать в преобразованиях, новациях и улучшениях, готовность обучаться и отношение к обучению как способу развития. Стоит отметить тот факт, что компания никогда не приобретала другие предприятия, поскольку это могло создать больше проблем и испортить качество человеческого капитала.
Базовым принципом управленческого мировоззрения в компании является принцип отказа от наказания. В Toyota принято искать не виновного, а причины ошибки. Здесь считают, что если ученик не научился, то это значит, что виноват учитель - не научил. Этот принцип противоречит широко распространенной управленческой парадигме, согласно которой начальник всегда прав. (10)
Очень яркий и характерный пример. Во время кризиса 1948 г. Toyota ввела политику жесткой экономии и вынуждена была уволить 1600 рабочих, что привело к забастовкам и демонстрациям. В этой непростой ситуации основатель и глава компании Кииширо Тойода взял ответственность за неудачи на себя и оставил пост президента. Этот его поступок помог успокоить рабочих и лишний раз подтвердил, что благополучие компании в долгосрочной перспективе важнее личных интересов, и нужно быть готовым взять на себя ответственность за происходящее. (11) С тех пор в компании больше не было массовых увольнений - даже в самые тяжелые времена. Например, во время азиатского финансового кризиса конца 1990-ых гг. отделение Toyota в Таиланде пережило четыре убыточных года, но никого из рабочих не уволили. Тогдашний президент Хироси Окуда издал распоряжение – «Сократите все расходы, но не трогайте людей». В августе 1998 года Moody's понизило рейтинг кредитоспособности Toyota с ААА до АА1 из-за ее приверженности системе пожизненного найма. В результате годовая выплата процентов выросла для компании на $220 млн., но ее руководители объявили, что от своего принципа не откажутся. (12)
Toyota считается одним из самых надежных работодателей не только в Японии, но и в мире. Компания действительно платит хорошую зарплату, хотя и не самую высокую в отрасли или в стране. Гораздо важнее, что в ней действует система пожизненного найма: рабочий приходит на завод и трудится на нем до пенсии, а иногда даже и до самой смерти. Этот принцип вообще широко применяется на многих японских предприятиях, и Toyota не является исключением. Однако на зарубежных предприятиях компании, в частности в России, такая система не всегда срабатывает. Так, например, когда в 2007 г. открылся завод Toyota в Санкт-Петербурге, после нескольких месяцев работы предприятия в учебном режиме на нем началась утечка кадров из-за низкой зарплаты и высоких требований к рабочим. (13) Видимо, сыграла свою роль выработавшаяся в условиях многолетней социально-экономической нестабильности наша привычка жить одним днем, не задумываясь о будущем. Российские рабочие предпочитают заработать как можно больше сегодня, не рассчитывая на завтрашний день, который обещает им пусть и стабильную, но не слишком высокую зарплату.
Несомненно, что японский менталитет играет важную роль в формировании управленческого мировоззрения компании. Для традиционной восточной деловой практики очень важны личные отношения, и Toyota - наглядный тому пример. Здесь принято, что информационные потоки свободно циркулируют, легко пересекают структурные и иерархические границы и распространяются за пределы компании, достигая поставщиков, покупателей и дилеров. Нередко руководители, чтобы получить или передать информацию, отправляются «в народ». Например, Такахиро Фудзиока, глава заводов в Такаоке и Тсутсуми, каждый день бывает в цеху, а по вечерам иногда выпивает вместе с рабочими (такие посиделки называются номикаи). А сотрудники, на самом высоком уровне отвечающие за сбыт, совещаются с дилерами и узнают о предпочтениях покупателей, приезжая к ним лично. (14) Еще одна особенность кадровой политики Toyota заключается в том, что программам обучения с отрывом от производства компания предпочитает повышение квалификации на рабочем месте.
Широко распространена практика, когда лучшие сотрудники выступают в роли наставников и передают свой опыт и ценности молодым. Главные критерии при оценке менеджеров - не результаты деятельности, а умение работать и учиться. В основе технологии управления Toyota лежит идеология «обучения», а не «командования», лидеры не отдают приказы, а обучают персонал. В компании действует «система предложений», введенная еще в 1950-ых годах, которая поощряет сотрудников фирмы, вносящих новые конструктивные идеи по совершенствованию производственного цикла и технологий.
Как известно, новое - это хорошо забытое старое. Истина банальная, но все равно справедливая, ведь еще не так давно в Советском Союзе тоже существовало движение наставничества, соцсоревнования, бригадный подряд - все это очень напоминают соответствующие элементы кадровой модели компании Toyota.
Социальная ответственность
Toyota Motor ведет активную деятельность по минимизации негативного воздействия своей продукции на окружающую среду. С 1997 года компания настойчиво продвигает гибридные технологи, она первой начала массовое производство и продажу гибридных автомобилей. Еще более экологичными считаются электромобили, и вслед за General Motors Toyota заявила о своём намерении начать разработку модели, действующей на аккумуляторе типа Li-ion. Сейчас компания уже испытывает «Toyota Plug-in HV» в Японии, США и Европе.
Уже второй год подряд, согласно рейтингу международного консалтингового агентства Interbrand, бренд Toyota признается самым экологичным в мире. Победа Toyota во многом продиктована лидирующими позициями компании в области гибридных технологий, кроме того, она вносит существенный вклад в сохранение природных ресурсов благодаря повторному использованию и переработке материалов. Ежегодно в июне во всех странах присутствия компании проходит экологическая акция «Зеленый месяц Toyota», цель которой - привлечь внимание общества к вопросам защиты окружающей среды. В России этот проект реализуется с 2007 года.
Компания активно участвует в различных благотворительных и социальных акциях. Что касается российских проектов, можно вспомнить участие дилерских центров Toyota в недавней благотворительной акции «Движение - жизнь!» направленной на поддержку детей с ограниченными возможностями. За последние несколько лет Toyota Motor выступила партнером целого ряда культурных, образовательных и социальных проектов в Мытищинском районе Московской области. При поддержке компании было организовано несколько выставок, спектаклей и концертов, а также проведены мероприятия по улучшению городской инфраструктуры, в частности, установлены новые светофоры и автобусные павильоны. Кроме того, компания выделяет гранты на развитие национальных парков и заповедников России. (15)
Подводя итог, можно сделать вывод, что Toyota - это не просто марка автомобиля, не просто успешная компания, и даже не просто набор передовых технологий и модных «систем». Toyota - это еще и определенная философия, в основе которой лежит понимание людей и их мотивации. В систему ценностей компании входят установка на непрерывное совершенствование (кайдзен), уважение к людям и их способностям, важность прямого опыта и получения информации из первых рук, создание и поддержание командного духа. Компания действует по принципу «покупатели на первом месте, дилеры - на втором, производитель - на последнем». Опыт компании Toyota Motor заслуживает пристального внимания и изучения именно как система базовых принципов, ориентированных не на получение сиюминутной выгоды, а на долгосрочную перспективу.
-----------------------------
1. Fortune Global 500, 2011 // http://money.cnn.com/magazines/fortune/global500/2011/full_list/index.html
2. Toyota вырвалась на первое место //http://auto.mail.ru/article.html?id=37117
3. Автомобильный портал RUS-auto.net. Toyota - 10 лет в России // http://rus-auto.net/news/nid/6003)
4. Официальный сайт компании Toyota. Завод Тойота в России //http://www.toyota.ru/about/factory.tmex
5. Лебедева И. П. Группирование предприятий в Японии (вертикальные объединения кэйрэцу) // http://www.logistics.ru/9/4/3/i20_26791p0.htm
6. Цит. по Лайкер Д. Дао Toyota - М., 2005 г., стр. 37
7. http://www.autostat.ru/news/view/1286/
8. Из интервью Тосио Хорикири, президента компании «Toyota Engineering Corporation», генерального директора Центра сертификации по TPS // http://kpi-business.com/novosti?view=12158003
9. Аргументы и Факты, 08.03.2012 // http://www.aif.ru/society/news/118173
10. Фидельман Г. Новое управленческое мировоззрение - «Экономика и жизнь» №45 (9311), 2009 г.
11. Лайкер Д. Дао Toyota - М., 2005 г., стр. 51
12. Хиротака Такеучи, Эми Осоно, Норихико Симидзу. Toyota: единство и борьба противоположностей. // http://www.up-pro.ru/library/production_management/systems/toyota_edinstvo.html
13. Экономная Тойота // Ведомости - Санкт-Петербург, 22.01.2008 г. http://www.ancor.ru/company/press/in_the_press/article/articleid/1604/
14 Хиротака Такеучи, Эми Осоно, Норихико Симидзу. Указ. соч.
15. Официальный сайт компании Toyota. Социальные проекты. // http://www.toyota.ru/about/social_projects.tmex
www.cloudwatcher.ru
14 принципов менеджмента ведущей компании мира (часть семнадцатая)
тойота
Принцип 11: уважай своих партнеров и поставщиков, ставь перед ними трудные задачи и помогай им совершенствоваться
Toyota очень практична, она совершенствует собственные системы, а потом показывает, как это может помочь нам... Так, Toyota выравнивает свое производство, чтобы упростить нашу работу. Отгрузка на Toyota производится 12 раз в день. Они помогли нам передвинуть прессы поближе к источнику воды и обучали наших работников. Что касается технической стороны ведения бизнеса, они активно помогают и здесь: приходят, производят измерения и делают все, чтобы снизить затраты в системе. С Toyota больше возможностей получить прибыль. Мы начали работать с Toyota, когда открыли завод в Канаде, где производился всего один сборочный узел, но производительность росла, и мы были вознаграждены, поэтому теперь мы изготавливаем почти все, что есть в кабине. По сравнению с остальными автомобилестроительными компаниями Toyota — самая лучшая.Поставщик комплектующих деталей для автомобилей
Поставщики комплектующих для автомобилей всегда отзываются о Toyota, как о своем лучшем потребителе, но при этом и самом жестком. «Жесткость» не означает, что с Toyota трудно ладить или что она предъявляет необоснованные требования. В случае с Toyota это означает, что компания придерживается весьма высоких стандартов и ожидает от своих партнеров соответствия уровню этих стандартов. Но что еще важнее, компания помогает своим партнерам добиться такого уровня. Эта глава рассказывает о том, как работает такой необычный подход к отношениям с поставщиками.
Давайте начнем с примера неэффективного (но, к сожалению, весьма распространенного) подхода к отношениям с поставщиками. В 1999 году одна из компаний американской «большой тройки», я буду называть ее «American Auto», решила выстроить лучшие в отрасли отношения с поставщиками. В American Auto устали слушать, каких успехов добились Toyota и Honda, обучая своих поставщиков бережливому производству. Годами American Auto работала над совершенствованием взаимоотношений с поставщиками, но когда поставщиков спрашивали, кто больше других преуспел в совершенствовании поставщиков, они неизменно вспоминали Toyota и Honda. В American Auto решили создать Центр по совершенствованию поставщиков, который станет мировым эталоном передовых методов. Даже Toyota будет равняться на American Auto.
Этот проект стал одним из основных проектов отдела материально-технического снабжения компании American Auto. У него были поборники на уровне вице-президентов. Вице-президенты заранее знали, каким будет Центр совершенствования поставщиков. У одного из них уже были готовы эскизы для строительства Центра, который должен был соответствовать последнему слову образовательных технологий. Его здание будет самым большим и самым лучшим, и поставщики потянутся туда осваивать самые передовые методы, включая методы бережливого производства.
Первым шагом в реализации проекта был сбор данных о текущей ситуации. Для этого были проинтервьюированы 25 поставщиков American Auto. Большая часть из них уже имела собственные программы бережливого производства, и многие из них в этом отношении обошли American Auto. В ходе этих интервью все поставщики неизменно высказывали одну мысль:
Скажите American Auto, чтобы она не тратила деньги на строительство большого дорогого здания для нашего обучения. Пусть они лучше приведут в порядок собственную компанию и станут надежным и умелым партнером, на которого можно положиться. Пусть займутся отладкой собственного неупорядоченного процесса разработки продукции и внедрением бережливого производства на своих предприятиях. В этом мы готовы помочь American Auto.
Слова, приведенные ниже, принадлежат одному из поставщиков Toyota. И его точка зрения очень типична для проведенных интервью.
Проблема American Auto в том, что в ней работают неопытные инженеры, которым кажется, что они все знают. Я бы предпочел им тех, которые понимают, что им нужно учиться, и занялся их подготовкой. Возможно, все дело в системе вознаграждений, которая делает их агрессивными и несговорчивыми. Я работаю с American Auto вот уже почти 18 лет и повидал немало хороших людей, готовых прийти на помощь. Теперь отношения существенно ухудшились. Раньше с людьми из American Auto было приятно работать. Сегодня я не доверяю им. Даже те, кому я доверял раньше, находят способы манипулировать поставщиками. Это весьма прискорбно.
Было понятно, что American Auto предстояла огромная работа, чтобы строительство фантастического центра совершенствования поставщиков могло принести хоть какую-то пользу. Основные проблемы заключались в слабости внутренних систем American Auto, недостаточной подготовке ее собственных людей и чрезмерном увлечении методом кнута и пряника в управлении при непонимании процессов, которые используют поставщики. Компания должна была завоевать право стать лидером, прежде чем учить своих поставщиков собственным примером. Ей же до этого было очень далеко, да и двигалась она совсем не туда, куда следует.
В конце концов, работы по созданию Центра совершенствования поставщиков были прекращены из соображений экономии средств. Это произошло в 1999 году, и дела в American Auto шли все хуже и хуже. American Auto, по моему опыту, не слишком отличается от прочих компаний, которые хотят одним махом получить все преимущества отлаженной и эффективной цепочки поставок без долгой и кропотливой предварительной работы внутри собственной компании.
Между тем Toyota потратила десятки лет на создание мощного бережливого предприятия в Японии и принялась за создание сети поставщиков мирового класса в Северной Америке. Требовательный, но справедливый подход к поставщикам находит с их стороны позитивный отклик. Так, по данным OEM Benchmark Survey, исследования поставщиков автомобильных комплектующих, проведенного Джоном Хенке из Оклендского университета, которое является основным при оценке отношений с поставщиками в американской автомобилестроительной промышленности, Toyota стоит на первом месте. По 17 показателям отношений от «доверия» до «восприятия возможностей», по данным за 2003 год, Toyota заняла первое место, за ней шли компании Honda и Nissan, тогда как Chrysler, Ford и GM оказались на четвертом, пятом и шестом местах. По сравнению с 2002 годом показатели Toyota продолжали повышаться и улучшились на 7%*.
* Источник: Robert Sherefkin and Julie Cantwell Armstrong, «Suppliers Prefer Japanese», Automotive News, May 12, 2003, pp. 1 and 50.
В ходе исследования поставщиков автомобилестроительных компаний, проведенного J. D. Power, выяснилось, что компании Nissan, Toyota и BMW являются лучшими производителями автомобилей в Северной Америке по применению инноваций в работе с поставщиками (Automotive News, февраль, 24, 2003). В отношении инноваций Honda и Mercedes также имели показатели выше средних, в то время как у группы Chrysler, Ford и General Motors были показатели ниже средних.
Toyota не раз была вознаграждена за значительный вклад в создание сети высокоэффективных поставщиков, которые функционировали как единое бережливое предприятие с Toyota. Неоднократно отмечавшееся наградами качество, которое отличает Toyota и Lexus, является следствием инноваций в проектно-конструкторской работе, в производстве и в общей надежности поставщиков. На поставщиков Toyota распространяются принципы концепции «точно вовремя» — и когда работа идет гладко, и когда в системе происходит сбой.
В то время как многие компании отказываются от системы «точно вовремя» после первого же кризиса, Toyota делает свое дело, преодолевая нечастые кризисы рука об руку с поставщиками. Так, 1 февраля 1997 года на заводе Aisin случился пожар*, уничтоживший предприятие. Aisln — один из крупнейших поставщиков Toyota, с которым ее связывают весьма тесные отношения. Обычно у Toyota есть два поставщика для каждого вида комплектующих, но Aisin был единственным производителем пи-клапана («р-valve»), который является важной частью тормозного механизма и используется в автомобилях Toyota по всему миру, — на тот момент времени 32 500 в день. Хваленая система «точно вовремя», практикуемая в Toyota, означала, что объем запасов в цепочке поставок рассчитан не более чем на два дня. Два дня, и произойдет катастрофа — неужели система «точно вовремя» себя не оправдала? Но Toyota не растерялась, 200 поставщиков самостоятельно организовали производство пи-клапана в течение двух дней. Изготовление деталей взяли на себя шестьдесят три разных предприятия. Они собрали существующую конструкторскую документацию и, используя собственное оборудование, создали временные линии для производства деталей. Они помогли Toyota продолжить работу практически бесперебойно. Возможности цепочки поставок значительно превосходят информационные технологии. Здесь на помощь приходят тесные взаимосвязи и находчивость.
Принцип: найди надежных партнеров и развивайся вместе с ними, что в долгосрочной перспективе сулит взаимную выгоду
Что вы, скорее всего, услышите, если отправитесь на конференцию по управлению цепочкой поставок? Вы узнаете массу вещей о «рационализации» цепочки поставок с помощью передовых информационный технологий. Если вы в состоянии получать информацию в наносекунды, должно быть, поставки тоже могут осуществляться в наносекунды? Вам вряд ли будут рассказывать о чрезвычайной сложности продуманной до мелочей повседневной работы по доставке ценности потребителю. Едва ли вы услышите что-нибудь об отношениях между фирмами — о том, как работать вместе на общие цели. Но именно это является ядром партнерских отношений Toyota с поставщиками, отношений, которые стали мировым эталоном.
* Nishiguchi, T. and A. Beaudet, 1998, «The Toyota Group and the Aisin Fire», Sloan Management Review, Fall, pp. 49-59.
Когда Toyota начала выпускать автомобили, у нее не было ни капитала, ни оборудования, чтобы производить мириады деталей, которые были нужны. чтобы сделать автомобиль. Одним из первых заданий, которое получил Ейдзи Тоёда как начинающий инженер, был поиск потенциальных поставщиков Toyota, изготавливающих детали высокого качества. В то время объемы производства были невелики, и Toyota не могла загрузить своих партнеров большими заказами. Все, что она могла им предложить, — это совместными усилиями развивать бизнес, чтобы в долгосрочной перспективе получить взаимную выгоду. Поставщики становились членами большой семьи, которая росла и осваивала производственную систему Toyota.
Даже когда Toyota превратилась в крупную международную компанию, она придерживалась прежних принципов партнерства. Она подолгу присматриваясь к новым поставщикам и поначалу давала им очень небольшие заказы. Они должны были доказать свое искреннее стремление соответствовать высоким стандартам Toyota в отношении качества, себестоимости и дисциплины поставок. Если первые выполненные заказы подтверждали такое стремление, объем заказов постепенно увеличивался. Компания обучала их подходу Toyota и принимала их в свою семью. А того, кто попал в семью, могут выгнать из нее, только если его поведение будет совершенно недопустимым.
Уважение к партнерам, которые входят в обширную сеть поставщиков, не означает, что работать с Toyota просто. Toyota считает, что, побуждая собственных работников постоянно совершенствоваться, она должна быть не менее требовательна и к поставщикам. Перед поставщиками ставятся весьма сложные задачи, требующие напряжения сил. Поставщики стремятся работать с Toyota, потому что они знают, что это позволит им стать лучше и завоевать уважение в мире бизнеса, у других потребителей. Но я не знаю такого поставщика, который считал бы, что Toyota легко угодить. С точки зрения Toyota, уважение с партнерам проявляется в том, что компания возлагает на своих поставщиков большие надежды, обращается с ними требовательно и справедливо и обучает их. Попустительство или карательные меры для Toyota являются проявлением неуважения. Менять поставщика из-за того, что другая компания выпускает те же изделия чуть дешевле (общая практика в автомобильной промышленности), для Toyota просто немыслимо. Как сказал Тайити Оно:
Повышение эффективности материнской компании за счет запугивания поставщиков, безусловно, чуждо производственной системе Toyota.
FORD и TOYOTA: разные подходы к партнерству в сфере логистики
Ярким примером различия в подходах Toyota и ее конкурентов является подход компании к логистическим проблемам при выстраивании цепочки поставок для производственных мощностей в Северной Америке. Как могут сборочные заводы Toyota получать детали несколько раз в день по системе «точно вовремя», если они разбросаны по всей территории США и Канады? Отчасти проблема решается за счет использования промежуточных складов (некоторые называют их терминалом «разбивки оптовой поставки»). Такой промежуточный склад несколько раз в день принимает детали, поставляемые поставщиками, перераспределяет их, составляя партии различных деталей, которых хватит на один-два часа производства, и отправляет такие комплекты деталей на сборочные заводы. Промежуточный склад обеспечивает эффективное перераспределение деталей, полученных от поставщиков, и доставку этих деталей на производственные предприятия по системе «точно вовремя». Промежуточные склады широко распространены в разных отраслях промышленности, например в пищевой, и, как правило, на такую обработку грузов заключается субподрядный договор. Но от других компаний Toyota отличает то, сколько внимания уделяет промежуточному хранению ее партнер, компания Transfreight, управляющая работой терминалов, и то, какое значение придает Toyota обучению своего партнера TPS. Toyota рассматривает промежуточное хранение как составную часть сборочной линии, ведь оно питает жизненной силой поток создания добавленной ценности, обеспечивая доставку деталей от поставщиков по системе «точно вовремя», а значит, работая на удовлетворение потребителя. Все это часть общего потока.
В середине 1990-х годов Ford Motor Company разработала собственную производственную систему Ford Production System (FPS), взяв за образец производственную систему Toyota. Сначала основное внимание уделялось внедрению этой системы на собственных предприятиях, но позднее, в 1990-е годы, стало уделяться внимание «синхронному материальному потоку» за пределами завода, главным образом регулярной доставке деталей на завод по системе «точно вовремя» небольшими партиями. Ford поступил так, как поступали в подобной ситуации многие крупные компании США В конце 1990-х годов они наняли руководителя со стороны и поставили перед ним соответствующую задачу. Этот руководитель раньше занимался материально-техническим снабжением в компании General Motors и имел некоторое представление о NUMMI (хотя сам там не работал). Он соответствовал представлениям Ford о настоящем лидере: был энергичен, требователен и беспощаден к тем, кто не торопился выполнять его распоряжения. Он пришел к выводу, что ему придется изменить систему организации приема поставок на сборочных заводах по системе «точно вовремя» и поставлять детали мелкими партиями. Для этого он нанял группу экспертов по системе вытягивания на производственном предприятии (более 20 человек), которые занялись отладкой внутренней логистики на заводе Ford. Они работали на сборочном заводе, вытягивая детали со сборочной линии и в некоторых случаях переупаковывая их из больших контейнеров размером 4" × 4" × 4" в маленькие контейнеры с запасом деталей на час работы. Затем они ввели в действие систему вытягивания для пополнения запасов на сборочной линии. На сборочных заводах по-прежнему хранились большие запасы деталей, поступивших от поставщиков в громоздких контейнерах, но этим предполагалось заняться, когда дойдут руки до внешней логистики, так что об этом пока не беспокоились.
Новый руководитель Ford решил, что внешней логистикой должна заняться независимая логистическая компания, что-то вроде поставщика Toyota — фирмы Transfreight. Он объявил тендер на заключение контракта, поставив весьма амбициозные задачи в отношении снижения затрат на логистику (на 10% в год), и обещал отдать весь логистический бизнес по Северной Америке компании, которая уложится в названную им цену. Контракт выиграла компания Penske Logistics, которая намеревалась уменьшить партии поставляемых на сборочный завод деталей. Компания взяла на себя обязательство доставлять 167 тыс. видов деталей от 900 поставщиков на заводы Ford, занимающиеся производством двигателей и сборкой. Они продумали схему транспортной сети и стали управлять ею, работая напрямую с перевозчиками, решая вопросы дисциплины и оплачивая счета.
И вот Ford отдает приказ: «Каждая деталь каждый день». Имелось в виду, что каждая деталь, раньше поставляемая на сборочные заводы еженедельно или ежемесячно, теперь должна была поступать по меньшей мере раз в день. Это было равноценно приказу «пленных не брать». Для проекта было придумано ироническое название — «Нирвана», и его ключевым моментом было соглашение с Penske Logistics. Ford твердо вознамерился сэкономить миллионы долларов на транспортировке и сокращении запасов. В результате руководитель Ford получил повышение, став вице-президентом компании по планированию материально-технического снабжения и логистике.
Penske Logistics создала отдельную бизнес-единицу во главе с собственным руководителем, которая занималась только поставками на Ford. Сама компания Penske не располагала большей частью ресурсов, необходимых для обеспечения бизнеса Ford, такими как грузовой транспорт или терминалы транзитной доставки, и в основном действовала как посредник между Ford и поставщиками услуг. В Penske на полную ставку работали аналитики и специалисты по организации движения, которые составляли соответствующую схему перевозок и затем на постоянной основе управляли ею. Таким образом, Penske играла роль посредника и, с одной стороны, вела переговоры со сборочными заводами Ford, обсуждая время и объемы поставок, а с другой — договаривалась с поставщиками транспортных услуг. Перед управляющими заводов была поставлена задача существенно сократить объемы запасов и организовать подобие «супермаркетов деталей», существующих в Toyota, чтобы освободить место на складах под иные нужды.
В целом все это очень походило на воспроизведение системы Toyota… но так казалось лишь на первый взгляд. И результаты оказались почти катастрофическими. В интервью с одним из руководителей фирмы Penske, который отвечал за планирование транспортной сети осенью 2002 года, мы узнали следующее:
«Каждая деталь каждый день» — для заводов это здорово, поскольку освобождаются здания, и, используя освободившееся место, они могут зарабатывать дополнительные доходы. Но логистика стала дороже на $100 миллионов в год. Через некоторое время мысль об этом стала для Ford настолько невыносимой, что отвечавший за это вице-президент уволился, и перед нами была поставлена задача вернуться к старой системе поставок деталей крупными партиями ежемесячно и еженедельно. На эту работу у нас ушло восемь месяцев. Высшее руководство Ford было страшно удивлено, что мы не можем сделать эту работу за восемь недель, хотя по большому счету такая работа требует более года. Теперь наша цель была вернуться к стоимости перевозок до внедрения «Нирваны». Завершая проект «Нирвана», мы добились того, что 95% деталей поставлялись ежедневно. При новом подходе Ford решил снизить этот показатель до 60%, и в настоящий момент он составляет около 80%. Переходить на систему «точно вовремя» и ожидать снижения затрат было по меньшей мере нереалистично. Я не понимаю, за счет чего могли сократиться затраты. Мы только что завершили исследование вариантов совершенствования сети поставок. Мы думаем, она сэкономит Ford $8 миллионов в год. Но что она сделает с заводами? Количество запасов обязательно возрастет, и они этому не рады.
Этот случай является ярким примером того, как Ford под руководством тогдашнего генерального директора Жака Нассера применил к управлению поставками подход, диаметрально противоположный подходу Toyota. Движимый благими намерениями, Ford пытался перенять в TPS систему поставки деталей «точно вовремя». Что, с точки зрения Toyota, компания Ford сделала не так?
Ford позволил руководителю со стороны возглавить логистическую сеть, которая стоила несколько миллиардов долларов, и принимать ключевые решения на собственное усмотрение.
Данный руководитель не понимал «подход Ford» и имел лишь поверхностное представление о том, как перевести логистическую сеть на систему «точно вовремя». Например, Toyota никогда не пыталась заниматься поставками «каждой детали каждый день». Для одних деталей это имеет смысл, для других нет.
Ответственность за огромную часть работы он делегировал сторонней организации, с которой у Ford не было тесных партнерских отношений, — по крайней мере, в данной сфере и в отношении проекта таких важности и масштабов.
Названная сторонняя фирма специализировалась исключительно на управлении логистикой и фактически не имела знаний по производственной системе компании Ford. Они знали, как перевозить грузы, и единственным показателем, который фирма стремилась оптимизировать, были транспортные расходы.
Сторонняя фирма так и не поняла предназначение проекта «Нирвана», не верила в него и считала, что Ford делает ошибку, которая может привести только к повышению затрат.
Ford поставил стороннюю компанию между своими заводами и сетью поставок, что гарантировало политические баталии между различными функциональными подразделениями, каждое из которых стремилось оптимизировать систему в свою пользу.
Последний момент очень важен. Toyota делает все, чтобы разрушить барьеры между функциональными подразделениями и сделать так, чтобы все работали на общую цель. Но, нанимая стороннюю логистическую фирму, единственная цель которой — снизить затраты на транспортную сеть, фирма Ford практически гарантировала возникновение конфликта и стремление к узковедомственной выгоде. Один из менеджеров компании Penske высказался следующим образом:
Мы (Penske) оказались между заводами и сетью поставок деталей. Заводы хотели того, что удобно им. Оптимизация поставок с точки зрения завода означает, что затраты могут и возрасти. Например, завод может захотеть получать детали конкретного поставщика пять раз в неделю. Если я раз в неделю пришлю на завод грузовик с недельным запасом деталей, я сэкономлю деньги на поставках, но завод будет испытывать неудобство. Заводы хотят добиться поставок точно вовремя. Но сеть поставок может строиться и на менее частых и менее дорогих поставках. Я веду переговоры с заводами с цифрами в руках, также поступают и они. Если мне удается их переубедить, сеть поставок только выигрывает.
На Тойоте Прадо открываем заднюю дверь, открываем крышку на двери с ключами:Около середины под дверью пластиковая крышка - снимаем:Собираем ключ для снятия запаски и в дальнейшем для домкрата:Наискосок вводим ключ до упора в квадратное гнездо - там ничего не видно, поэтому эта операция легко делается на ощупь:
Toyota – ведущий в мире производитель качественных автомобилей.Как владелец машины Toyota Land Cruiser Prado 2008 года выпуска 4 литра бензин пневмоподвеска, могу следующее сообщить об этой машине:- мягкая, не чувствует «наших плохих дорог»- с автоматической коробкой легко, без рывков набирает скорость, без завышения шума в коробке при переключениях
Элвин, герой серии научно-фантастических романов Орсона Скотта Карда, способен различать самые крохотные объекты и видеть, когда состояние вещей отклоняется от нормы, например, он видит, что кость сломана, а в куске железа есть трещина. Элвин способен вернуть объекту его нормальное состояние, которое предстает перед его мысленным взором, — кость срастается, а железо вновь становится целым и невредимым.
msd.com.ua
Dao Tayota: 14 принципов менеджмента ведущей компании мира (часть семнадцатая)
тойота
Создание расширенного обучающегося предприятия означает расширение возможностей партнеров
Размышляя о неудаче, постигшей компанию American Auto с поставщиками, и удивляясь, почему она хочет сразу взлететь на лифте на самый верх, ни разу не остановившись на нижних этажах, я попробовал осмыслить эту проблему, обратившись к иерархической модели, выстроенной в виде пирамиды. Вспоминая занятия по социальной психологии в колледже, я думал об иерархии потребностей Маслоу, о которой кратко рассказывалось в предыдущей главе. Эта теория предполагает, что люди могут работать над удовлетворением потребностей высшего уровня, таких как самоактуализация (самореализация), только тогда, когда уже удовлетворены потребности низшего уровня. Исходя из этого я разработал версию иерархии потребностей применительно к поставщикам.
Поставщики высказали мысль о том, что они не заинтересованы в помощи American Auto, которая намеревалась заниматься их совершенствованием, пока не будет решен ряд более фундаментальных вопросов. Для начала им хотелось справедливых и честных коммерческих отношений. Зачастую методы American Auto были попросту непорядочными. Например, American Auto приняла методику Toyota в отношении целевой цены, то есть установки цен для поставщиков вместо проведения открытых тендеров, но эта методика применялась весьма неэффективно. Один из поставщиков рассказывает:
С каждым подразделением (AmericanAuto), с которым мы имеем дело, нам приходится улаживать целевую цену отдельно. Если ты выходишь за установленный предел цены, они не оформляют заказ на закупку. Мы ведем бесконечные переговоры, и в результате дело заканчивается тем, что мы запускаем производство, так и не получив заказа.
Другой поставщик жалуется на то, как непоследовательна American Auto в процессе постановки задач:
Если нам удается выйти на нужную цену в самом начале процесса проектирования, они меняют задачу и ставят новую, более сложную. Поэтому никаких стимулов достижения цели на ранних этапах нет. Процесс постановки задач попросту отсутствует. Каждый раз все происходит по-разному. Единый подход отсутствует, даже если речь идет о разных программах в пределах одного и того же проекта. Все зависит от человека, который сегодня занимается этим вопросом.
Помимо этого American Auto разработала длительную и сложную процедуру сертификации процессов поставщика по критериям качества. Хотя она была достаточно обременительна, поставщики ее приняли, но American Auto беспрестанно вносила в процедуру новые изменения. За время создания нового автомобиля процедура менялась много раз, и каждый раз сертификация поставщика становилась все более длительным процессом. Не пройдя процесс сертификации, поставщик не мог получить денег за оснастку, American Auto, как и большинство производственных компаний, компенсировала затраты на оснастку, штампы и специальное оборудование, используемое для изготовления деталей. Их стоимость может достигать миллионов долларов. В некоторых случаях поставщики уже сделали всю работу, предшествующую производству, и производят новые детали месяцами, причем детали проходят все проверки качества, но, поскольку поставщик не получил сертификата качества, он не сможет получить компенсационных выплат за инструмент.
Это возвращает нас к концепции принуждающей и поощряющей бюрократии, которая рассматривалась в главе 12. И American Auto, и Toyota ведут дела с поставщиками бюрократическими методами. Под этими словами я понимаю, что существует множество стандартов, ревизий, норм, правил и т. п. Однако методы American Auto поставщики воспринимают как принуждающие, a Toyota, которая пользуется сходными процедурами контроля качества, действует поощряющими методами. Американский поставщик комплектующих деталей для отделки салона описывает работу с Toyota следующим образом:
Когда заходит речь о решении проблем, Toyota в отличие от American Auto не проводит по 15 раз подряд всесторонние исследования процесса. Ее представители говорят: «Уберите немного материала отсюда и оттуда, и все будет в порядке — действуйте». В течение 11 лет мне ни разу не приходилось делать для Toyota опытные образцы. Подколенные валики, напольные панели, приборные панели и т. д. так похожи на предшествующие модели, что в опытном образце нет никакой необходимости. Если возникает проблема, они проверяют, в чем дело, и предлагают решение — при этом их интересует качество, а не поиск виноватых.
Поставщик American Auto не может сдержать эмоции:
Сравнивая сегодняшнюю атмосферу с тем, что было раньше, можно сказать: мы рады, когда из нас не вытряхивают душу. Мы можем выполнить работу или внести изменения, работая в самых сложных условиях (например, осуществить то, что, как мы утверждали ранее, сделать невозможно), и сделать это безупречно на 99,9%. Но если мы не вышли на 100%, нас просто уничтожат. Раньше мы получали благодарность за то, что вкалываем как проклятые, чтобы в последний момент внести дополнительные изменения. Сегодня мы рады, если в течение недели не получили ни одной выволочки. Раньше мы получали вознаграждения, теперь система построена только на наказании.
Иерархия потребностей цепочки поставок, предполагает, что деловые отношения являются справедливыми, процессы — стабильными, а требования — четкими. Пока этого не произойдет, невозможно выйти на более высокий уровень расширения полномочий и возможностей и создать обучающееся предприятие. Спуститься на нижние уровни этой иерархии можно так же быстро, как и подняться вверх. В начале 1990-х годов в American Auto наблюдался прогресс применительно к уровням данной иерархии, а в конце 1990-х годов и вплоть до XXI века ситуация стала резко ухудшаться. Между тем Toyota стабильно и неизменно повышала свой уровень. Для того чтобы стать эталоном в области отношений с поставщиками, American Auto необходимо сделать куда больше, чем выстроить Центр совершенствования поставщиков. Чтобы хоть немного приблизиться к Toyota, этой компании придется пересмотреть свою внутреннюю производственную культуру, стать бережливой организацией и перестроить структуры, которые приводят к противоречивой политике в отношении поставщиков.
Принцип 11 подхода Toyota гласит: уважай своих партнеров и поставщиков, ставь перед ними трудные задачи и помогай им совершенствоваться. Образцом отношений с поставщиками Toyota стала благодаря тому, что она учится и развивается вместе с ними. С моей точки зрения, это дало уникальный результат: расширенное обучающееся предприятие. Я считаю, что это высшая форма бережливого предприятия.
Конкретная ситуация: компания TRIM MASTERS, INC. — сиденья автомобилей по системе «точно вовремя», как учит TOYOTA
В 1994 году компания Trim Masters, Inc. (TMI) была создана как совместное предприятие для снабжения завода Toyota в Джорджтауне. Создание компании было частью работы Toyota по организации сети поставок в США и по обеспечению сборочных заводов Toyota в Северной Америке деталями по системе «точно вовремя». Дао Toyota не позволяет компании покупать детали у кого попало. Toyota рассматривает поставщиков как долгосрочных партнеров, и они должны отвечать высоким стандартам в отношении качества, затрат и дисциплины поставок. Чтобы приблизить поставщиков к производству в Америке и обеспечить их соответствующий уровень, Toyota создала совместное предприятие, которым владели Toyota Tsusho, Агасо, давний поставщик комплектующих для салона автомобилей в Японии, и Johnson Controls. Компания Johnson Controls (JCI) является единственным крупным держателем акций (40%), но контрольный пакет акций находится у Toyota и Агасо (которая на 75% принадлежит Toyota). Раньше Toyota заключала с Johnson Controls контракты на поставку сидений для автомобилей и тесно сотрудничала с этой фирмой, обучая ее TPS. Этот завод до сих пор изготавливает значительную часть сидений Toyota, но Toyota любит иметь не менее двух конкурирующих поставщиков, чтобы у них был стимул совершенствоваться и снижать затраты.
Поэтому Toyota создала TMI, совместное предприятие, которое должно было обеспечить сиденьями новый завод Toyota в Джорджтауне, штат Кентукки, Завод TMI по производству сидений находится в Николасвил-ле, штат Кентукки, Всеми делами TMI заправляет в основном Агасо, в то время как JCI скорее играет роль пассивного партнера. Toyota поощряет TMI следовать принципам TPS — производить только сиденья, необходимые на сборочной линии в точно таком же порядке, в котором они востребованы. Даже Агасо, являющаяся одним из главных поставщиков сидений для Toyota и имеющая огромный опыт применения TPS, иногда держит в Японии резервный запас готовой продукции. Однако от TMI Toyota ждала большего. С той минуты, как кузов автомобиля выходит из покрасочного цеха и начинает двигаться по сборочной линии, у TMI есть около четырех часов, чтобы получить заказ Toyota на нужный комплект сидений, собрать эти сиденья и отгрузить их Toyota. Готовые сиденья точно вовремя доставляют к главной сборочной линии, где их устанавливают именно в ту машину, для которой они сделаны. Такая система требует огромного напряжения сил и предназначена не для слабонервных! Любой самый незначительный сбой приведет к остановке завода Toyota, а каждая минута его простоя обходится в десятки тысяч долларов. При этом большую часть деталей TMI получает от поставщиков, осуществляющих поставки в течение всего дня. Возникни у одного из них проблема, и через пару часов TMI остановится. К тому же сиденья являются сложным сборочным узлом, для которого весьма важен и внешний вид. Если поступит партия некачественной кожи, на одной из сотни пластмассовых деталей окажется крохотная царапина, пружинный механизм будет некачественным и т. д. Toyota не примет такое сиденье.
Но Toyota терпеливо обучает поставщиков применению TPS, заботясь о том, чтобы их продукция соответствовала самым высоким стандартам. И хотя TMI пришлось потрудиться, компания добилась прекрасных результатов. Эксперт по бережливому производству Джим Вумек (соавтор книги «Бережливое производство». — Прим. науч. ред.) любит говорить, что объем оборачиваемости запасов основных комплектующих является лакмусовой бумажкой подлинно бережливого производства — чем больше, тем лучше. Спросите Хессельброка, который является начальником производства всех заводов TMI, какова оборачиваемость запасов в Николасвилле, и вы ему не поверите: 135 в месяц! Когда я увидел это на первом слайде, я не сомневался, что заметил ошибку. Месяц перепутали с годом, да? Нет, таковы показатели за месяц. На завод поступает номенклатура из более чем 750 исходных компонентов, Часть из них поступает из Японии, часть из Мексики, большая часть комплектующих — из США и Канады. Если поставка комплектующих в какой-то момент прекратится, через полтора часа завод перестанет выпускать сиденья.
Для каждого сиденья необходим пенистый материал, поступающий из компании-филиала Foamex. Существует 75 разных видов пенистых материалов, и избыток запасов может потребовать сооружения отдельного склада. Поэтому обычно в цехе находится запас пенистого материала не более чем на полтора часа работы плюс буферный запас на 45 минут. Ежедневно TMI принимает 12 грузовиков пенистого материала, которые прибывают каждые полтора часа. Когда я посетил завод, изготавливающий сиденья, в 2000 году, средний показатель по дефектам сидений, поставляемых для Toyota, был менее 40 на миллион. Требованием Toyota был уровень 50 дефектных сидений на миллион максимум. Каждое сиденье состояло из 100 деталей, а в день производилось около 1000 сидений. Дефектной может оказаться любая деталь, и если она будет использована, дефектным будет признано все сиденье. Когда я был там в последний раз летом 2002 года, показатель дефектов снизился до 20—30 на миллион. За это время TMI ввела в строй новый завод, который изготавливает сиденья для Lexus RX330 в Кембридже, провинция Онтарио, требование которого — менее десятка дефектов на миллион — настоящее качество шести сигм*.
* Шесть сигм — статистическая концепция, на основе которой любой процесс измеряется в параметрах числа дефектов. При высшем уровне в шесть сигм число дефектов составляет 3,4 на миллион возможных. Данным термином называют также философию управления, направленную на построение идеальных процессов путем тщательного анализа результатов статистических измерений и соответствующего совершенствования процессов, — Прим. науч. ред.
Завод по изготовлению сидений в Николасвилле очень похож на заводы поставщиков Toyota в Японии, Сиденье в сборе изготавливается на движущейся сборочной линии, работающей по принципу потока единичных изделий. Вдоль линии в небольших контейнерах на передвижных стеллажах расположен небольшой запас деталей (на один-два часа). Единственным планом работы является заказ с Toyota, который поступает по радио после того, как кузов автомобиля выходит из покрасочного цеха. Таким образом, завод знает, в какой последовательности следует изготавливать сиденья, предназначенные для разных моделей. Заказ поступает каждые 55 секунд (время такта завода Toyota). Поэтому TMI узнает, какое сиденье нужно собирать следующим, лишь за 55 секунд до начала работы. Компания собирает 10 таких заказов на комплекты сидений и меняет последовательность их изготовления на обратную (отгрузка комплектов производится в той последовательности, которая необходима Toyota), после чего передает заказ на сборочную линию и другие вспомогательные производства завода TMI. Некоторые крупные компоненты, такие как рамы сидений, чехлы и пенистый материал, подаются к сборочной линии в соответствующей последовательности, а более мелкие детали, такие как болты и гайки, хранятся в «супермаркете» деталей и подаются на линию с помощью системы канбан. С собственными поставщиками TMI также использует систему вытягивания при пополнении запасов. На завод поступает около 800 различных деталей, некоторые из Мексики и Японии, Разумеется, для отдаленных заводов объемы запасов больше, и TMI принимает эти детали по графику. Например, для деталей из Мексики они держат буферный запас на 40 часов, что их крайне расстраивает.
Но Toyota не позволяет TMI почивать на лаврах. В 2001 году Toyota поставила перед своими поставщиками задачу снизить цену комплектующих на 30% для очередного представления новых моделей в 2004 году, то есть ежегодно требовалось снижать цену приблизительно на 10%. Ходили слухи, что, создав совместное предприятие с компанией Peugeot, Toyota узнала, сколько платят за детали другие автомобилестроительные компании. В то время как другие компании в подобном случае подыскивали поставщиков подешевле, Toyota, верная своему принципу использовать отличное качество и непревзойденное мастерство как стратегическое оружие, не видела причины, по которой нынешние поставщики с помощью TPS не могут добиться снижения затрат до мирового уровня.
Несмотря на то что затраты TMI на рабочую силу и без того невелики, компания отреагировала на это предложение позитивно и продуктивно. Для решения поставленной задачи был развернут крупный проект хосин канри («развертывание политики»). Оно начинается с постановки целей высшего уровня с последующей детализацией этих целей для каждого подразделения организации. Развертывание политики является частью подхода Toyota к управлению и представляет собой процесс взаимных уступок в ходе обмена информации между высшим и средним звеном управленческой структуры, а иногда мастерами (супервайзерами) и лидерами команд. Одним из основных преимуществ хосин канри является возможность с его помощью перевести цели высшего уровня, уровня корпоративного руководства, на уровень количественно измеримых, осуществимых мероприятий. Иначе говоря, развертывание политики представляет собой систему, которая поощряет работников анализировать ситуацию, создавать планы совершенствования, заниматься проверками производительности и принимать соответствующие меры. Для этой цели компания Trim Master имеет специальный штаб, где на уровне каждого функционального подразделения представлены цели снижения затрат, а также межфункциональные проекты. Любая схема развертывания политики выходит на измеримые цели и меры и обязательно содержит сведения о лицах, ответственных за достижение намеченных результатов. TMI проводит еженедельные совещания для обсуждения прогресса в каждом из направлений.
TMI никогда не впадает в панику из-за высоких требований, которые к ней предъявляются, так как гарантией ее успеха является сотрудничество с Toyota. Toyota понимает, что возможности контроля затрат со стороны TMI ограничены и значительных сокращений затрат можно достичь лишь совместными усилиями с помощью разработки максимально экономичных изделий. Такая разработка требует систематичного межфункционального подхода к исследованию конструктивных параметров, влияющих на затраты при создании новой продукции, и проектирования продукции, которая отвечают стандартам качества при намеченных Toyota затратах. Работая вместе, TMI и Toyota могут значительно снизить цены за счет изменения конструкции сидений до того, как они пойдут в производство. Кроме того, представители Toyota, занимающиеся снабжением, регулярно посещают завод, чтобы проверить, как организован процесс и как он совершенствуется. Сегодня они очень довольны работой TMI. TMI, в свою очередь, понимает, что усердие и хорошие результаты обеспечат ей справедливое и доброжелательное отношение, TMI является примером успешного применения TPS в США и при этом является компанией, которая работает в жестких условиях — производство по системе «точно вовремя» и поставка без запасов для обеспечения заданной последовательности работы сборочного завода. Но спросите высшее руководство, является ли их компания образцовым бережливым предприятием, и в ответ они только рассмеются. Они знают, как далеко им еще до уровня, который они видели в материнской компании в Японии.
Продолжение
На Тойоте Прадо открываем заднюю дверь, открываем крышку на двери с ключами:Около середины под дверью пластиковая крышка - снимаем:Собираем ключ для снятия запаски и в дальнейшем для домкрата:Наискосок вводим ключ до упора в квадратное гнездо - там ничего не видно, поэтому эта операция легко делается на ощупь:
Toyota – ведущий в мире производитель качественных автомобилей.Как владелец машины Toyota Land Cruiser Prado 2008 года выпуска 4 литра бензин пневмоподвеска, могу следующее сообщить об этой машине:- мягкая, не чувствует «наших плохих дорог»- с автоматической коробкой легко, без рывков набирает скорость, без завышения шума в коробке при переключениях
Элвин, герой серии научно-фантастических романов Орсона Скотта Карда, способен различать самые крохотные объекты и видеть, когда состояние вещей отклоняется от нормы, например, он видит, что кость сломана, а в куске железа есть трещина. Элвин способен вернуть объекту его нормальное состояние, которое предстает перед его мысленным взором, — кость срастается, а железо вновь становится целым и невредимым.
msd.com.ua
Тойота
Оказывается, сегодня компания Тойота занимается не только выпуском автомобилей. Она производит разнообразную продукцию, начиная от роботов и заканчивая возведением элитных коттеджей. Но конечно главное для столь многогранной компании - выпуск автомобилей, ведь это крупнейший производитель в мире.
Также стоит отметить, что благодаря компании Тойота появились интересные подходы в менеджменте. Можно упомянуть хотя бы систему поставок «точно в срок» и кайдзен. Так что имя компании постоянно на слуху. К тому же именно она и стала главным двигателем всей экономики Японии в прошлом столетии.
Сакиши Тойода, родившийся в 1867 году в семье плотника, обожал мечтать. Он хотел стать изобретателем, чтобы своими открытиями изменить жизнь людей. Сакиши был самым старшим ребенком в семье, согласно неписаным национальным традициям, именно он и должен был унаследовать профессию отца. Хорошо еще, что в те времена на старые традиции смотрели уже сквозь пальцы. Так молодой Сакиши получил шанс стать кем-то другим и исполнить свою мечту. Тойода занялся ткацкими станками, погрузившись надолго в эту отрасль, начиная с 1890 года.
У Сакиши не было профессионального образования, он всему обучался на практике. В 1894 году у начинающего изобретателя появился сын Кииширо. Именно он через 20 лет поможет отцу создать автоматический ткацкий станок. То устройство ляжет в основу появления новой компании семьи Тойда - Toyoda Automatic Loom Works. Так появилась знаменитая компания.
А в 1930 году Сакиши Тойода скончался, и семейный бизнес возглавил его сын Кииширо. Говорят, что на самом деле Сакиши всегда мечтал заниматься автомобилями. Легенды гласят, что его последней просьбой сыну было переключиться именно на это направление. Как бы то ни было, но Кииширо продал патент на семейное достояние - автоматизированный ткацкий станок. Новыми хозяевами изобретения стали англичане из Platt Brothers & Со. Ltd., а Тойода получил 100 тысяч фунтов.
Эти средства были вложены им в новое подразделение компании, которое создавало собственный автомобиль. Стоит отметить, что производство велось все же с нуля. Компания начала с того, что стала попросту копировать удачные американские модели. И такой подход, в общем-то, типичный для японской промышленной культуры. Местные инженеры предпочитают копировать нечто хорошее, пока не появится совершенство. И только потому уже можно приступать к самостоятельной разработке.
Однако даже просто копировать было не так-то и просто. Долго инженеры не могли выполнить полный комплекс работ. Только в 1936 году компания Toyoda Automatic Loom Works представила машину Toyoda AA, она, естественно, практически полностью копировала американскую Chrysler Airflow. Обрадовавшись успехам, компания представила собственный логотип, а вскоре и грузовик. Он сразу же стал экспортироваться в Северный Китай.
Уже на первоначальном этапе производства компания стала придерживаться некоторых инновационных подходов. Будучи еще ткацкой фирмой, Тойода придерживалась принципа, что из-за проблем у одного работника производство не должно останавливаться. В итоге готовая продукция имела минимальные шансы получить брак. Такая же тактика была применена и при выпуске японцами автомобилей.
В 1937 году Кииширо Тойода, видя успехи своего автомобильного направления, решил выделить его в отдельное предприятие. Оно получило название Toyota Motor Company. Очевидно, что в названии буква «d» оказалась замененной на «t». И на этот счет есть своя легенда. Оказывается, при написании слова Toyoda иероглиф «d» выводить довольно тяжело. Надо делать целых девять взмахов кисточкой, а ведь это число для Японии традиционно несчастливое. Кииширо проявил суеверие, решив, что не стоит иметь дело с чем-то, что может плохо повлиять на продажи. Так вместо иероглифа «d» появился «t», который требовал восемь взмахов кистью. А ведь для Японии это уже счастливое число!
Для европейца такие внимание к деталям написания букв может показаться смешным, но мы просто обладаем другими культурными традициями. Нам вообще сложно понять, почему сотрудники Тойота так любят петь гимн своей компании и вообще работают на компании всею свою жизнь. Так и родилась компания Тойота, выпускающая автомобили. Ей быстро повело - правительство сделало заказ на три тысячи грузовиков. Компания за счет этого получила средства для дальнейших исследований. Ведь японцы понимали, что на одном копировании далеко не уедешь и рано или поздно придется выпускать уже оригинальный продукт.
А в 1938 году в городе Коромо открылся первый завод компании Тойота, целиком ориентированный на создание машин. А средства на его строительство дало как раз правительство тем самым свои крупным заказом. Сегодня города Коромо уже не существует - в честь компании он носит имя Тойота. В годы Второй мировой войны компания выпускала военные грузовики для императорской армии, при этом в силу дефицита конструкция была упрощенной, например, с одной фарой. Считается, что одним из факторов быстрого поражения Японии стала бомбардировка союзников города Аити, когда были уничтожены заводы Тойота.
В 1947 году компания, оправившись, стала выпускать коммерческие пассажирские модели SA. Тогда была заложена стратегия компании на долгие годы. Она основывалась на выкупе компаний и основании дочерних фирм, которые могли бы обеспечить выпуск комплектующих для автомобилей на протяжении всего производственного цикла. Так фирма обезопасила себя от проблем с поставками запчастей. В то же время в компании стала культивироваться система поставок «точно в срок».
Благодаря ей детали приходили на склад как раз к началу производства автомобиля. Это позволяло избежать огромных залежей ненужных пока еще комплектующих. Но по-настоящему качественные машины стали появляться только лишь в начале 1950-х, с полным переход на создание более или менее собственных автомобилей. В тот момент рождается еще одна отдельная компания, Toyota Motor Sales Co., Ltd. Ее цель - сбыт готовой продукции.
В 1950-1960-е на заводах японской компании осуществляется значительная модернизация. Тогда в компанию и внедряются принципы «кайдзен». Само слово это составное, включает две части, обозначающие «перемену» и «мудрость». Принципы кайдзен можно считать своеобразной философией, рассчитанной на постепенные улучшения. Для достижения совершенства надо просто меняться к лучшему пусть и неспешно, медленно, но каждую минуту. Принципы постоянного совершенствования к началу 1960-х вовсю уже применялись на заводах Тойоты.
А в 1951 году в компании появилась еще одна управленческая инновация - система предложения идей. Любой сотрудник фирмы мог внести свои предложения по улучшению любого процесса, происходящего в компании. Сегодня такие вещи кажутся нормальной для любой крупной фирмы, но полвека назад это было в диковинку. Уже позже этот удачный подход был скопирован западными компаниями.
А в 1957 году открылся филиал японской компании, Toyota Motor Sales USA., в самой Америке. Начались поставки автомобилей из Страны Восходящего солнца в США. Правда, первый опыт оказался неудачным. В «автомобильной Мекке» было нелегко заявить о себе, что и повлекло за собой плохие продажи японских машин. Да и американским условиям они плохо отвечали. Первый экспортный вариант компании, Toyota Crown, никак не вязался у жителей Штатов с образом хорошего автомобиля. Вскоре компания запустила шестилетнюю программу реформ, которая позволила улучшить качество новых моделей.
А рывок в плане экспорта у Тойота пришелся на 1973 год с наступлением в мире нефтяного кризиса. Национальные экономики отдельные предприятия терпели убытки, а для японской компании такая ситуация только пошла на пользу. В моду вошли экономичные автомобили, которые Тойота тут же и разрекламировала в США. В 1982 году вместе с General Motors японцы построили свой первый завод на территории Америки. И работать это предприятие будет не менее эффективно, чего японские отделения. А в конце 80-х в США родилась новая марка Lexus.
Этот бренд роскошных автомобилей создала Тойота, с его помощью удалось потеснить на рынке таких классиков, как Mercedes и Cadillac. В настоящее время Тойота является самым крупным в мире производителем машин, она по прежнему верна принципу кайдзен, продолжая совершенствоваться. Компания смогла впервые за 76 лет сместить с трона лидера американцев из General Motors. Но Тойота открывает для себя новые горизонты, намереваясь, в частности заявить о себе в мире робототехники.
Недавно бывший руководитель компании заявил, что в ближайшие десять лет именно создание роботов может стать основным направлением для компании. Главная разработка Тойота - роботы-партнеры. Создать их удалось в тесном сотрудничестве с Технологическим университетом Токио и другими компаниями. Первоначально планировалось создать таких роботов, которые помогали бы человеку при производстве автомобилей. Разработка учитывала наличие таких качеств, как ловкость, физика, интеллект и гибкость. Один из партнеров «Тойота» не так давно показал на своей презентации, как умеет играть на скрипке.
Этот робот - самый знаменитый концепт, чья полезность сомнительна. Пока еще компании не удалось создать такого робота, который смог бы заменить на производстве человека. Внимание японской компании на робототехнику заставляет обратить еще и резкие падение рождаемости в стране. В перспективе может оказаться, что в Японии попросту не будет хватать квалифицированных сотрудников и некому будет ухаживать за стариками. Так что в этой связи разработка роботов-партнеров дело перспективное.
Сегодня на Тойота работает более 320 тысяч человек, оборот компании составляет более 200 миллиардов долларов, а чистая прибыль более 2 миллиардов. Японский гигант занимает восьмое место в списке Fortune Global 500 - крупнейших мировых компаний. Такому успеху компания обязана деловым принципам, заложенным в нее еще основателями и японским национальным чертам - трудолюбие, упорству, стремлению учиться.
Новые мифы.
Новые факты.
Новые советы.
www.molomo.ru