Испытание авто после ремонта
Испытание и выдача автомобилей из ремонта
1.Испытание и выдача автомобилей из ремонта. После сборки автомобиль поступает на контроль и испытание. Контроль и испытание автомобиля проводят для проверки комплектности, качества сборочных, регулировочных и крепежных работ, проверки работы и технического состояния всех агрегатов, механизмов и приборов, дополнительной регулировки, а также для выявления соответствия технических показателей требуемым техническим условиям. Испытания проводят на стенде с беговыми барабанами. Стенд позволяет проверить работу двигателя, агрегатов трансмиссии и ходовой части, а также оценить основные эксплуатационно-технические качества автомобиля (мощность двигателя, тяговое усилие на ведущих колесах, расход топлива на различных скоростных и нагрузочных режимах, путь и время разгона до заданной скорости, потери мощности на трение в агрегатах и ходовой части, наибольший допустимый тормозной путь с определенной скоростью), проверить и отрегулировать установку углов управляемых колес и т.д. Все выявленные при испытании неисправности необходимо устранить.
1.1.В дополнение к стендовым испытаниям каждый грузовой автомобиль после капитального ремонта должен пройти испытание пробегом на расстояние 30 км с нагрузкой, равной 75 % номинальной грузоподъемности, при скорости не более 30 км/ч, для проверки на управляемость, а также для дополнительного определения соответствия технического состояния автомобиля требуемым техническим нормам на различных режимах работы и в различных дорожных условиях. При пробеге проверяют также исправность и надежность работы всех систем, механизмов и соединений.
После испытания пробегом автомобиль тщательно осматривают. Все выявленные пробегом и осмотром дефекты устраняют. При отсутствии дефектов (или после их устранения) автомобиль поступает на окончательную окраску, а затем предъявляется отделу технического контроля (ОТК). На принятом ОТК автомобиле (на передней панели кабины под капотом) ставят приемочное клеймо.Качество отремонтированных автомобилей должно соответствовать техническим условиям на сдачу в КР и выдачу из ремонта автомобилей, их агрегатов и узлов. На каждый выпускаемый из ремонта автомобиль заказчику выдается паспорт этого автомобиля, в котором фиксируется комплектность, техническое состояние и соответствие отремонтированного автомобиля техническим условиям. Технические условия устанавливают гарантированную исправную работу автомобиля в течение определенного времени и до определенного пробега за этот период. Эти сроки службы и пробеги гарантированы при условии эксплуатации автомобилей в соответствии с «Положением о техническом обслуживании и ремонте подвижного состава автомобильного транспорта» и инструкциями заводов-изготовителей. В течение гарантийного срока все обнаруженные заказчиком неисправности по вине АРП должны быть устранены безвозмездно в течение трех суток со дня предъявления рекламации. Карбюраторные двигатели отремонтированных автомобилей в целях ограничения нагрузки на период обкатки снабжают запломбированной ограничительной шайбой, снимать которую в эксплуатации нужно в строгом соответствии с правилами, установленными для новых двигателей.В настоящее время установлен гарантийный срок эксплуатации автомобилей — 12 мес со дня выдачи из ремонта при пробегах (для первой категории эксплуатации): не более 20 тыс. км — автобусами; не более 16 тыс. км — прочими автомобилями всех видов и назначений.Гарантийный срок хранения отремонтированных составных частей автомобилей 12 мес с момента выдачи из ремонта при условии соблюдения правил консервации и хранения.При выпуске автомобиля из КР к нему прилагаются следующие документы:паспорт автомобиля с отметкой АРП о произведенном ремонте, указанием даты выпуска из ремонта, новых номеров шасси и двигателя, а также основного цвета окраски;инструкция по эксплуатации с указанием особенностей эксплуатации отремонтированных автомобилей в обкаточный и гарантийный периоды, а также периодов и организации устранения дефектов в гарантийный период;При выпуске двигателя из КР к нему прилагаются: паспорт; инструкция по эксплуатации с указанием особенностей установки и эксплуатации двигателя в обкаточный и гарантийный периоды.Выпуск из КР автомобилей, их составных частей и деталей (комплектов деталей) оформляется приемо-сдаточным актом.
www.autoezda.com
Испытание и выдача автомобилей из ремонта
После сборки автомобиль поступает на контроль и испытание. Для проверки комплектности, качества сборочных, регулировочных и крепежных работ, проверки работы и технического состояния всех агрегатов, механизмов и приборов, дополнительной регулировки, а также для выявления соответствия технических показателей требуемым техническим условиям производят контроль и испытание автомобиля. Испытания проводят на стенде с беговыми барабанами. Стенд дает возможность проверить работу двигателя, агрегатов трансмиссии и ходовой части, а также установить основные эксплуатационно-технические качества автомобиля (мощность двигателя, тяговое усилие на ведущих колесах, расход топлива на различных скоростных и нагрузочных режимах, путь и время разгона до заданной скорости, потери мощности на трение в агрегатах и ходовой части, максимальный допустимый тормозной путь с определенной скоростью), проконтролировать и отрегулировать установку углов управляемых колес и т.д. Все обнаруженные при испытании неисправности следует устранить.
Каждый грузовой автомобиль после капитального ремонта в дополнение к стендовым испытаниям должен пройти испытание пробегом на расстояние 30 км с нагрузкой, равной 75% номинальной грузоподъемности, при скорости не более 30 км/ч, для проверки на управляемость, а также для дополнительного установления соответствия технического состояния автомобиля требуемым техническим нормам на различных режимах работы и в различных дорожных условиях. Исправность и надежность работы всех систем, механизмов и соединений можно проверить во время испытания пробегом.
После испытания пробегом автомобиль тщательно осматривают. Все дефекты, выявленные пробегом и осмотром, устраняют. При отсутствии дефектов (или после их устранения) автомобиль поступает на окончательную окраску, а затем предъявляется отделу технического контроля (ОТК). На принятом ОТК автомобиле приемочное клеймо ставят на передней панели кабины под капотом.
Качество отремонтированных автомобилей должно соответствовать техническим условиям на сдачу в КР и выдачу из ремонта автомобилей, их агрегатов и узлов. На каждый выпускаемый из ремонта автомобиль заказчику выдается паспорт этого автомобиля, в котором отмечается комплектность, техническое состояние и соответствие отремонтированного автомобиля техническим условиям. Технические условия определяют гарантированную исправную работу автомобиля в течение определенного времени и до определенного пробега за этот период. При условии эксплуатации автомобилей в соответствии с «Положением о техническом обслуживании и ремонте подвижного состава автомобильного транспорта» и инструкциями заводов-изготовителей сроки службы и пробеги гарантированы. В течение гарантийного срока все обнаруженные заказчиком неисправности по вине АРП должны быть устранены безвозмездно в течение трех суток со дня предъявления рекламации. В целях ограничения нагрузки на период обкатки карбюраторные двигатели отремонтированных автомобилей снабжают запломбированной ограничительной шайбой, снимать которую в эксплуатации нужно в строгом соответствии с правилами, определенными для новых двигателей.
Гарантийный срок эксплуатации автомобилей в настоящее время установлен — 12 мес. со дня выдачи из ремонта при пробегах (для первой категории эксплуатации): не более 20 тыс. км — автобусами; не более 16 тыс. км — прочими автомобилями всех видов и назначений.
Гарантийный срок хранения отремонтированных составных частей автомобилей — 12 мес. с момента выдачи из ремонта при соблюдении правил консервации и хранения.
При выпуске автомобиля из КР к нему прилагаются следующие документы:
- паспорт автомобиля с отметкой АРП о произведенном ремонте, указанием даты выпуска из ремонта, новых номеров шасси и двигателя, а также основного цвета окраски;
- инструкция по эксплуатации с указанием особенностей эксплуатации отремонтированных автомобилей в обкаточный и гарантийный периоды, а также периодов и организации устранения дефектов в гарантийный период.
При выпуске двигателя из КР к нему прилагаются:
- паспорт;
- инструкция по эксплуатации с указанием особенностей установки и эксплуатации двигателя в обкаточный и гарантийный периоды.
Приемо-сдаточным актом оформляется выпуск из КР автомобилей, их составных частей и деталей (комплектов деталей).
Другие статьи по теме:
с вашего сайта.
autocarta.ru
Техническое Обслуживание и Ремонт Автомобилей
§ 76. Способы и технологический процесс сборки автомобиля
Автомобили собирают двумя способами: тупиковым и поточным. Тупиковый способ сборки обычно применяют на предприятиях с небольшой программой ремонтных работ, поточный же способ — на специальных ремонтных предприятиях. Характеристика каждого способа рассматривалась ранее при разборке автомобиля. Применяют различные инструменты, позволяющие механизировать процесс сборки.
Технологический процесс сборки разных моделей автомобилей определяется их конструкцией, но общая последовательность сборки примерно одинакова.
Рассмотрим в укрупненном виде технологический процесс сборки грузового автомобиля ЗИЛ-130. Сборка заключается в установке на раму автомобиля в определенной последовательности собранных, испытанных и окрашенных узлов и агрегатов. Раму располагают так, чтобы горизонтальные нижние полки продольных балок находились в верхнем положении. Устанавливают и закрепляют обоймы и дополнительные буфера передних и задних рессор, тягу соединения двигателя с рамой в сборе с чашками и буферами.
Затем устанавливают передний - и задний мосты в сборе с рессорами так, чтобы совместились отверстия передних ушек рессор и кронштейнов, вставляют и закрепляют пальцы. Задние концы рессор устанавливают накладками на сухари кронштейнов, вставляют втулки, совмещают отверстия вкладышей, втулок, устанавливают стяжные болты, пружинные шайбы и закрепляют гайки.
Следующей операцией является установка и закрепление амортизаторов передней подвески. В гнездо кронштейнов задней опоры двигателя вставляют опорные подушки.
Устанавливают и закрепляют воздушные баллоны, тормозной кран, пневматические трубопроводы, соединяя их с тормозным краном, воздушными баллонами и тормозными камерами передних и задних колес.
Размещают и закрепляют карданную передачу (основной и промежуточный карданные валы), закрепляют на раме брызговики двигателя, глушитель, амортизатор глушителя и приемные трубы глушителя. Краном поднимают шасси и переворачивают, опуская на деревянные подкладки под передний и задний мосты. Устанавливают буксирный прибор в сборе, соединяют с трубопроводами гибкие шланги тормозных камер передних и задних колес. На поперечину рамы устанавливают и закрепляют разобщительный кран, соединив его с тормозным краном.
На раме устанавливают и закрепляют кронштейн вала педали сцепления, надевают рычаг и закрепляют его болтом, подложив под головку болта пружинную шайбу. На вал педали надевают рычаг управления тормозным краном и устанавливают его в отверстие кронштейна. На наружный конец вала надевают педаль привода сцепления, предварительно вставив шпонку, и закрепляют болтом.
Устанавливают и закрепляют рулевой механизм с гидроусилителем, соединяют передний мост с рулевым механизмом продольной рулевой тягой, вставив в отверстие поворотного рычага и сошки вала рулевого механизма шаровые пальцы, и закрепляют их гайками. На передние концы продольных балок рамы устанавливают и закрепляют передний буфер, усилители и буксирные крюки, брызговики .облицовки радиатора.
Затем прокладывают пучки проводов, закрепляют их скобами, а соединительную трех- клеммную панель крепят к четвертой поперечине рамы. Аккумуляторную батарею устанавливают в гнездо, присоединяя соответствующие провода.
Устанавливают, закрепляют на раме двигатель в сборе со сцеплением и коробкой передач. К выпускному трубопроводу прикрепляют приемные трубы глушителя. Устанавливают и закрепляют первую трубку от крестовины тормозного крана к клапану регулятора давления и трубку от компрессора к первому воздушному баллону. Колено подводящего патрубка радиатора соединяют со шлангами и сливным краником, а затем устанавливают и соединяют хомутами с патрубком водяного насоса. Тягу от промежуточного рычага тормозного крана закрепляют с рычагом привода ручного тормоза, отрегулировав длину тяги и обеспечив зазор, равный 1,0 мм, между пальцем и скобой тяги. Рычаг педали сцепления соединяют с рычагом вилки включения сцепления, отрегулировав свободный ход педали — 35—50 мм.
На переднем кронштейне топливного бака устанавливают и закрепляют фильтр-отстой- ник. Устанавливают в кронштейны и закрепляют топливный бак, фильтр-отстойник и топливный насос.
Отвернув пробки наливных отверстий, заливают трансмиссионное автомобильное масло в картеры заднего моста и коробки передач. Через пресс-масленки смазывают узлы головой, рулевых тяг, подшипник вилки выключения сцепления, оси педали сцепления, стебля крюка буксирного прибора, шкворней поворотных цапф, пальцев передней и задней подвески, валов разжимных кулаков.
Устанавливают и закрепляют на передней поперечине рамы радиатор в сборе с рамкой подвески, кожухом вентилятора, жалюзи, масляным радиатором. При помощи хомутов соединяют шланги патрубка водяной рубашки и колена подводящего патрубка с патрубками радиатора. Также шлангами с трубками соединяют патрубки масляного радиатора с масляным картером двигателя и нижней секцией масляного насоса. Шлангами низкого и высокого давления соединяют бачок и корпус насоса с гидроусилителем рулевого механизма.
Затем устанавливают и закрепляют кабину в сборе с арматурой, электрооборудованием, отопителем, облицовкой радиатора, крыльями,
подножками, капотом и колонкой рулевого управления. На рычаг переключения передач навертывают рукоятку, соединяют верхнюю и нижнюю части педали сцепления. Соединяют трубки пневматической системы с регулятором давления и воздушным манометром.
Далее соединяют провода с соответствующими узлами и датчиками автомобиля.
К полу кабины закрепляют передний и задний коврики. К ступицам крепят передние и задние колеса. Устанавливают подушки и спинки сидений пассажира и водителя.
Затем отсоединяют продольную рулевую тягу от рулевого механизма и заправляют маслом систему гидроусилителя, предварительно повернув рулевое колесо в крайнее левое положение. Масло доливают до тех пор, пока при вращении рулевого колеса от одного крайнего положения до другого не будет залить не менее 2,5 л. Затем включают двигатель и на режиме холостого хода доливают масло до уровня метки, вращая рулевое колесо от одного крайнего положения до другого и удерживая его в этих положениях в течение 2—3 с с усилием 10 кгс. Заливку масла заканчивают при прекращении выхода пузырьков воздуха из системы через масло в бачке насоса гидроусилителя. После заправки маслом закрепляют крышку бачка насоса, устанавливают сошку на валу рулевого механизма, предварительно совместив их метки.
Далее готовят собранный автомобиль к испытанию. Перед испытанием автомобиль подвергается внешнему осмотру. При осмотре проверяется комплектность, качество сборки, исправное действие и правильность регулировки отдельных механизмов и приборов, а также готовность к испытательному пробегу.
Проверяют состояние дверей. Они должны легко открываться, плотно закрываться и не иметь перекосов. Стекла дверей должны плавно опускаться и подниматься подъемными механизмами. Проверяют качество сборки капота двигателя. Он должен плотно закрываться, легко подниматься, опускаться и удерживаться в поднятом положении.
Обращают внимание на монтаж передних колес, которые не должны иметь ощутимого люфта при боковом качании. Проверяют работу приборов освещения и сигнализации, а также надежность крепления всех резьбовых соединений. Затем автомобиль полностью заправляют (водой, топливом, маслом), проверяют правильность подсоединения проводов зажигания и регулируют фары. Заправку осуществляют в соответствии с заводской инструкцией
www.toira.ru
Общая сборка, испытание и выпуск автомобиля из капитального ремонта
Общая сборка автомобиля является завершающим этапом в технологическом процессе его ремонта и восстановления. Качество сборки зависит не только от точности сборки, но и от методов организации сборочного процесса, чистоты собираемых деталей, оснащения рабочих мест, контроля в процессе сборки и испытания собраных узлов и агрегатов автомобиля. Для наглядного представления процесса сборки состовляют графическую схемму сборки (рис. 4), на которой видна последовательность сборки деталей 1- 32 в подузлы или узлы и далее узлов и агрегатов вплоть до общей сборки автомобиля.
Формы сборки. В зависимости от типа производства, трудоемкости процесса сборки и особенностей автомобиля в насстоящее время различают две организационные формы сборки: поточную и непоточную.
Поточный метод сборки считается наиболее совершенной формой сборки агрегатов автомобилей. Его применение целесообразно в организациях по ремонту полнокомплектных автомобилей со значительной производственной программой. Собираемый автомобиль принудительно перемещается по конвейру. Режим работы конвейра (как правило, переодический) устанавливается в зависимости от производственной программы, такта выпуска, сложности сборочных операций и различных технологических
факторов. Промежуток времени между выходом со сборки двух готовых автомобилей или его узлов называется тактом сборки.
Для бесперебойной поточной сборки необходимо своевременное обеспечение линии требующимися деталями и узлами. При этом сборка узлов должна быть согласована с тактом общей сборки агрегата или автомобиля. Сборка на конвейре с переодическим перемещением проводится в периоды его остановки.
Признаки, характеризующие почетную сборку:
за каждым рабочим местом закреплена определенная операция;
собранный на предидущем рабочем месте агрегат или автомобиль передается на следующую операцию немедленно по окончании предидущей;
на всех рабочих местах сборочной линии работа синхронизирована и выполняется в соответствии с установочным тактом;
сборка механизирована.
Сборка грузового автомобиля проводится в такой последовательности. На базовую сборочную единицу (раму) устанавливают собраные агрегаты и узлы: передний и задний мосты, карданную передачу, рулевое управление, двигатель в сборе с коробкой передач, радиатор, кабину, колеса и остальные узлы, механизмы и детали. Необходимые регулировочные работы осуществляют непосредственно в процессе сборки.
Непоточный метод сборки характеризуется выполнением сборочных операций на постоянном рабочем месте, к которому подаются все детали и узлы собираемого автомобиля. При этом сборка может быть выполнена по принципу концетрации и деффиринциации операций.
При концетрации сборочных операций автомобиль собирается на одном рабочем (сборочном) месте. Однако при такой организации технологического процесса сборку должны проводить высококвалифицированые сборщики, причем времени на сборку затрачивается больше.
При дифференциации сборочных операций сборка выполняется паралельно на нескольких рабочих местах, что значительно ускоряет этот процесс при некотором снижения качества сборки.
Средства механизации и автоматизации сборочных процессов. Эти средства, устанавливаемые на рабочих местах, обеспечивают значительное повышение производительности и качества труда при сборке, а так же снижение трудоемкости и себестоимости продукции. К ним относятся устройства для установки и закрепления изделий и манипуляций ими, специализированая тара для деталей и улов и механизированые (автоматизированые) механические устройства для выполнения основных сборочных операций.
При осуществлении сборочных операций применяют механизированно- ручной и механизированный инструмент с электрическим, пневматическим и гидравлическим приводом. Наиболее широкое применение находят электрические и пневматические механизированно – ручные инструменты.
Приработка контактных поверхностей и испытание изделия. Приработка – это процесс изменения размеров, макро- и микрогеометрии, а так же физико – механических свойств трущихся поверхностей с целью оптимизации их параметров за сравнительно короткий промежуток времени.
Приработке (обкатке) и испытанию подвергаются такие агрегаты, как двигатель, коробка передач, редуктор, ведущий мост и др. Эти процессы осуществляются на установках,оснащеных необходимыми приводными и нагрузочными устройствами, комплексом контрольно – измерительных средств и инженерных коммуникаций.
Приработка двигателей осуществляетсяв три стадии: холодная приработка, горячая без нагрузки и горячая с нагрузкой. На стадии холодной приработки электродвигатель потребляет ток, на стадии горячей приработки электродвигатель работает в генераторном режиме, вырабатывая ток, который направляется в сеть организации. В процессе приработки проводятся необходимые регулировки, оценивается техническое состояние двигателя и качество ремонта. В конце процесса приработки двигатель подвергается испытанию на соответствие ТТ.
Приработка и испытание агрегатов трансмиссии (коробка передач, раздаточная коробка, редуктор, ведущий мост и др.) осуществляется на установках, имеющих приводные и нагрузочные устройства, а так же контрольно – измерительные средства.
Коробки передач прирабатывают и испытовают на установленных режимах без нагрузки и под нагрузкой на всех передачах, контролируя при этом легкость их переключения, отсутствие самовыключения, уровень шума, степень нагрева контролируемых участков и т.д.
Редукторы и задние мосты прирабатывают и испытывают при различной частоте вращения ведущей шестерни без нагрузки и с нагрузкой до полного торможения поочередно одного из барабанов. При этом одновременно контролируют уровень и характер шума шестерен редуктора,герметичность соединений, степень нагрева подшипниковых узлов и т.п. При наличии повышеного шума шестерен редуктора производится дополнительная регулировка по контракту и боковому зазору в зубьях.
Выпуск автомобиля из ремонта. Собранный автомобиль должен быть смазан, а агрегаты заправлены маслами в соответствии с ТТ. Все регулируемые механизмы и узлы должны быть отрегулированы с соблюдением ТТ. После этого автомобиль поступает на пост контроля и испытания.
В процессе контроля и испытания проверяется комплектность автомобиля, качество сборки, исправность функционирования и правильность регулировки отельных механизмов и приборов в соответствии с ТТ.
Испытания автомобиля проводят на стендах с беговыми барабанами, где проверяется работа двигателя, агрегатов трансмиссии и ходовой части. При этом оцениваются основные эксплуатационно- технические качества автомобиля, включая мощность двигателя, тяговое усилие на ведущих колесах, расход топлива при различных скоростных и нагрузочных режимах, путь и время разгона до заданной скорости, потерю мощности на трение в агрегатах и ходовой части, наибольший допустимый тормозной путь при определеной скорости, интенсивность действия тормозных механизмов. При этом проверяется и при необходимости регулируется установка углов управляемых колес и т.п.
После стендовых испытаний каждый автомобиль проходит испытание пробегом, например на расстояние 40 км с грузом, равным 75% грузоподъемности автомобиля , со скоростью не более 40 км/ч по дорогам с твердым покрытием. При пробеге проверяют исправность и надежность
работы всех систем, механизмов и соединений. После испытания пробегом автомобиль тщательно осматривают, после чего все выявленые дефекты устраняют.
Затем автомобиль поступает на окончательную окраску и на склад готовой продукции. На каждый выпускаемый из ремонта автомобиль АРО выдает заказчику паспорт, в котором фиксируется комплектность, техническое состояние и соответствие отремонтированого автомобиля техническим требованиям на его КР. ТТ устанавливают гарантированую исправную работу автомобиля в течение определеного времени и определеного пробега за этот период. На протяжении гарантийного срока все обнаруженые заказчиком неисправности по вине АРО должны быть устранены в течение трех суток со дня предьявления рекламации.
В настоящее время гарантийный срок эксплуатации автомобиля составляет 12 месяцев со дня выдачи из ремонта при пробегах:
не более 20 тыс. км – для автобусов;
не более 16 тыс. км – для прочих автомобилей.
При выпуске автомобиля из КР прилагаются следующие документы:
к автомобилю:
паспорт с отметкой АРО о проведеном ремонте с указанием даты выпуска из ремонта;
новые номера шасси и двигателя;
основной цвет окраски автомобиля ;
инструкция по эксплуатации с указанием особенностей эксплуатации отремонтированного автомобиля в обкаточный и гарантийный периоды;
к двигателю:
паспорт;
инструкция по эксплуатации с указанием особенностей установки и эксплуатации двигателя в обкаточный и гарантийный периоды.
Выпуск из КР автомобилей, их составных частей и деталей (комплектов деталей) оформляется соответствующим приемосдаточным актом.
studfiles.net
Техническое Обслуживание и Ремонт Автомобилей
§ 54. Ремонт деталей кривошипно-шатунного механизма
Блок цилиндров большинства двигателей изготавливается из серого чугуна со вставными мокрыми гильзами. Основными дефектами блока цилиндров являются: пробоины, сколы, трещины различного размера и расположения, износ цилиндров или деформации посадочных отверстий под гильзу, износ гнезд вкладышей коренных подшипников, гнезд клапанов, обломы шпилек, срыв резьбы в отверстиях.
Дефекты блока цилиндров устанавливают тщательным осмотром, обмером цилиндров и опрессовкой. Осмотром обнаруживают пробоины, сколы, заметные для глаза трещины, срывы резьбы, состояние зеркала цилиндров. Опрессовкой выявляют трещины, не замеченные при осмотре. Один из применяемых стендов для гидравлического испытания блока цилиндров показан на рис. 70. В рубашку охлаждения блока под давлением 4—5 кгс/см2 нагнетается вода. При этом на блок цилиндров должна быть установлена головка блока или вместо нее чугунная плита с резиновой прокладкой. Поворачивая раму стенда, осматривают блок и устанавливают, нет ли течи воды.

сверлом диаметром 5 мм и разделывают по всей длине шлифовальным кругом под углом 90° на глубину 4/5 толщины стенки. Рекомендуется перед сваркой блок цилиндров нагреть до температуры 600—650°С. Трещину заваривают газовой сваркой, применяя нейтральное пламя, флюс и чугунно-медный присадочный пруток диаметром 5 мм. Шов должен быть ровным, сплошным и выступать над поверхностью основного металла не более 1,0—1,5 мм. После заварки блок цилиндров медленно охлаждают в термошкафу или в томильной яме, Заварку трещин можно осуществлять и без подогрева блока. В этом случае трещину заваривают электросваркой, применяя постоянный ток обратной полярности. Хорошие результаты получаются при заварке трещин между поясками цилиндров электродами, изготовленными из монель-металла, и следующем режиме сварки: сила тока — 120 А, напряжение 65—75 В.
Сварочный шов зачищают заподлицо с плоскостью основного металла напильником или наждачным кругом. Затем блок цилиндров подвергают опрессовке на стенде, проверяя герметичность сварочного шва. Течи воды через шов не допускаются.
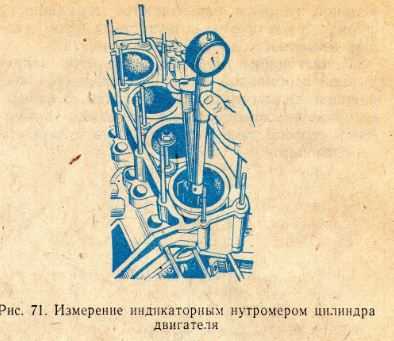
На поверхности блока вокруг трещины на расстоянии до 30 мм создают шероховатость путем насечки зубилом или дробеструйной обработкой. Ацетоном или бензином обезжиривают подготовленную поверхность блока. Шпателем последовательно наносят слои эпоксидной пасты на подготовленную сухую поверхность. Вначале наносят первый слой пасты толщиной до 1 мм, резко перемещая шпатель по поверхности блока. Затем наносят второй слой пасты толщиной не менее 2 мм, тщательно втирая ее. Общая толщина слоя пасты на всей поверхности должна составлять 3—4 мм.
После заделки трещины блок цилиндров оставляют на 25—28 ч до полного затвердевания пасты. Процесс затвердевания пасты можно ускорить подогревом электрической отражательной печью до температуры 100°С или при приготовлении пасты осуществляют выпаривание отвердителя (полиэтиленполиамина) путем нагревания до температуры 105—110°С и последующей выдержки при данной температуре в течение 3 ч. Отремонтированную поверхность зачищают драчевым напильником или абразивным кругом. Подтеки пасты срубают зубилом.
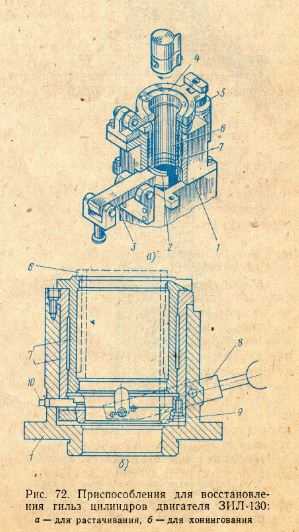
Пробоины можно заделывать приваркой заплат, изготовленных из мягкой стали такой же толщины, что и стенка детали. Форма заплаты должна соответствовать форме поврежденного участка, а размеры ее на 1,5—2,0 мм меньше размера пробоины. Края пробоины и заплаты обрабатывают под углом. Заплату вначале приваривают в двух местах, а затем приваривают по всему периметру. Применяют электросварку и медные электроды, обернутые жестью. Рекомендуется герметизировать поврежденный участок эпоксидной смолой.

Трещины рубашки охлаждения блока можно заделать постановкой штифтов. Порядок выполнения работ следующий. Вначале по концам трещины просверливают отверстия сверлом диаметром 4—5 мм. Затем этим же сверлом сверлят отверстия по всей длине трещины на расстоянии 7—8 мм одно от другого. Нарезают резьбу и ввертывают медные прутки на глубину, равную толщине стенки блока.
Прутки обрезают ножовкой, оставляя концы, выступающие на 1,5—2,0 мм над поверхностью детали. Сверлят отверстия между установленными штифтами так, чтобы они перекрывали их на 3/4 диаметра. Нарезают резьбу, ввертывают медные прутки и обрезают их ножовкой, оставляя соответствующие концы. Далее легкими ударами молотка концы штифтов расчеканивают, образуя плотный шов. Если требуется, то шов выравнивают напильником. Затем блок цилиндров подвергают опрессовке.
Блок цилиндров, имеющий сколы, допустимые для ремонта, восстанавливают наплавкой или приваркой заплаты.Величину износа цилиндров или гильз определяют индикаторным нутромером (рис.71). Измерения делают в двух взаимно перпендикулярных направлениях и в трех поясах. Одно направление устанавливают параллельно оси коленчатого вала. Первый пояс располагается на расстоянии 5—10 мм от верхней плоскости блока, второй — в средней части цилиндра и третий — на расстоянии 15—20 мм от нижней кромки цилиндра. В зависимости от величины износа устанавливают вид ремонта. Обычно осуществляют растачивание и последующую доводку или постановку (запрессовку) гильз.
Вставные гильзы также можно ремонтировать расточкой с последующей окончательной обработкой хонингованием. Результаты исследований показали, что не менее,.80% гильз двигателя ЗИЛ-130, поступивших на авторемонтные заводы в первый раз, можно восстанавливать.
Растачивание является основным способом ремонта цилиндров и гильз. Цилиндры или гильзы обрабатывают до ремонтных размеров на расточных станках стационарного или переносного типа. Гильзы крепят в специальном приспособлении, установленном на столе расточного станка.На рис. 72, а показано приспособление, применяемое при растачивании гильзы двигателя ЗИЛ-130. Гильза 6 устанавливается во втулке 7, которая расположена в корпусе 1 приспособления. Крепление осуществляется зажимами 3 и 5. Усилие зажима передается на гильзу через два сферических кольца 4 и 2.
После растачивания гильза подвергается хонингованию. Гильзу 6 (рис. 72,6) крепят на столе станка в специальном приспособлении, которое состоит из корпуса 1, двух втулок 7, выталкивающего устройства 8, установочного кольца 9 и зажимного болта 10.
При обработке хонинговальную головку, соединенную со шпинделем станка, вводят в обрабатываемое отверстие (бруски находятся в сжатом состоянии). Вначале осуществляют предварительное, а затем окончательное хонингование. Применяют хонинговальную головку с механическим, гидравлическим или пневматическим разжимным устройством.
На рис. 73 показана одна из конструкций хонинговальных головок с пневматическим приводом.
Пневматический привод обеспечивает постоянное давление брусков на стенки цилиндра, что повышает качество обработки и производительность процесса хонингования. При этом можно регулировать давление брусков на обрабатываемую поверхность и автоматизировать процесс разжатия брусков по мере изменения диаметра гильзы.
Для получения правильной геометрической формы цилиндра в процессе хонингования необходимо установить определенную длину хода головки. Она должна быть такой, чтобы абразивные бруски выходили за торец цилиндра на величину, не превышающую 0,2—0,4 их длины. При большей величине хода хонинговальной головки наблюдаются погрешности формы, в частности, вогнутость, а при меньшей величине хода — бочкообразность.
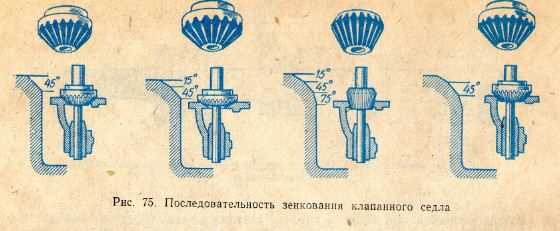
Для предварительного хонингования рекомендуются бруски синтетических алмазов А10МХ50, а для окончательного хонингования — бруски БХ-100Х 11 Х9К38БС. Обработка ведется при режимах: окружная скорость вращения головки 280 об/мин, а скорость возвратно-поступательного движения — 90 двойных ходов в минуту. Припуск на предварительное хонингование устанавливают не более 0,08 мм, а для окончательного хонингования 0,04 мм.
Окончательная обработка цилиндров двигателя может быть осуществлена шариковыми раскатными головкам и, позволяющими получить поверхность требуемой точности и шероховатости. Процесс осуществляют после растачивания или одновременно за один проход обрабатывают отверстие цилиндра резцом и шариком головки.
Рекомендуется следующий режим резания и раскатывания: частота вращения — 450 об/мин; подача на 1 оборот — 0,08 мм; глубина резания — 0,25 мм; сила давления на шарик — 20 кгс.
Независимо от способа окончательной обработки цилиндров (гильз) их внутренний диаметр должен иметь один и тот же ремонтный размер.
Цилиндры можно восстанавливать запрессовкой гильз, если их износ превышает последний ремонтный размер или на стенках имеются глубокие риски и задиры. Для этого цилиндры обрабатывают под ремонтную гильзу, толщина которой должна быть не менее 3— 4 мм. В верхней части цилиндра растачивают кольцевую выточку под буртик гильзы. Гильзы запрессовывают с натягом 0,05—0,10 мм на гидравлическом прессе, опрессовывают и обрабатывают (растачивают и хонингуют) до номинального размера. Иногда гильзы обрабатывают под размер меньше номинального, чтобы использовать перешлифованные старые поршни.
Вставные гильзы выпрессовывают и запрессовывают при помощи специальных съемников.
Деформации гнезд коренных подшипников проверяют поверочной скалкой. Если она входит в гнезда и без больших усилий проворачивается, то деформации отсутствуют.

Изношенные и деформированные гнезда вкладышей коренных подшипников растачивают до номинального размера. Снятые крышки подшипников обязательно маркируют (ставят номер блока цилиндров и порядковый номер крышки). Плоскости разъема крышки фрезеруют на определенную величину (0,6—0,8 мм) и контролируют индикаторным приспособлением. Так же фрезеруют внешний паз в крышке переднего и фасонный паз в крышке заднего коренного подшипника. Обработанные и принятые ОТК крышки собирают с блоком цилиндров соответственно их маркировке.

Ремонт головки блока цилиндров и клапанных седел. Основными дефектами головок блока цилиндров являются: трещины в различных местах, коробление поверхности сопряжения с блоком цилиндров, износ отверстий в направляющих втулках клапанов и резьбы, ослабление посадки седел клапанов в гнездах.
Головка блока цилиндров с деталями клапанного механизма работает в очень тяжелых условиях — при высоких температурах и воздействии механических и тепловых нагрузок.
Поэтому в зависимости от дефекта и места его расположения необходимо правильно установить способ ремонта. Трещины можно заделывать эпоксидными пастами, заваркой с общим подогревом головки, наложением заплат, штифтовкой.
Коробление плоскости сопряжения головки с блоком цилиндров устраняют шлифованием или фрезерованием с последующим шлифованием. При этом должна быть выдержана минимально допустимая глубина камеры сгорания, которая указывается в технических условиях. Величину коробления плоскости устанавливают на плите по краске или при помощи контрольной линейки и щупа.
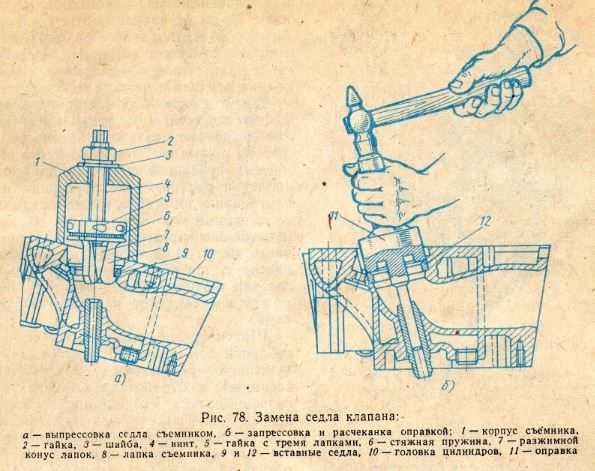
Износ и раковины на фасках седел клапанов устраняют шлифованием или осуществляют замену седла. Производят притирку седла с клапаном или зенкование с последующим шлифованием и притиркой. При зенковании применяют комплект из четырех зенковок, имеющих углы наклона режущих кромок 30 или 45, 75 и 15°. Зенковки с углами 75 и 15° являются вспомогательными и применяются для получения необходимой рабочей фаски. На рис. 75 показана последовательность зенкования клапанного седла.
Рабочие фаски седел клапанов шлифуют абразивными кругами под соответствующий угол. Для двигателя ЗИЛ-130 впускные клапаны шлифуют под углом 60°, а выпускные клапаны —под углом 45° к оси направляющих втулок. Ширина рабочей фаски седла клапана должна быть 1,5—2,0 мм для двигателей ГАЗ и 2,5—3,0 мм — для двигателей ЗИЛ.
При больших износах седла клапана, когда утопание калибра превышает допустимую величину, указанную в технических условиях, седло клапана заменяют новым. Для этого изношенное клапанное седло растачивают, а затем запрессовывают вставное седло клапана, расчеканивая его при помощи специальной оправки. Далее шлифуют или зенкуют рабочую фаску до получения требуемого размера. Затем осуществляют притирку с рабочей поверхностью клапана.
Притирку выполняют на специальных станках, которые полностью механизируют процесс и позволяют выполнять обработку всех клапанов одновременно. Для притирки применяют притирочную пасту или пасту ГОИ. Рекомендуется вначале притирку производить более грубой пастой. Тонкая паста применяется для получения окончательной чистовой поверхности. Притирка должна обеспечить плотное, герметичное соединение рабочих фасок клапана и седла, исключающее возможность проникновения газов. Притертые клапан и седло должны иметь по всей окружности фаски ровную матовую полоску а определенной ширины (рис. 76). Для двигателей ЗИЛ ширина полоски должна быть равной l/2 ширины рабочей фаски седла.
Качество притирки проверяют прибором (рис. 77), при помощи которого создают над клапаном избыточное давление воздуха (0,7 кгс/см2). Давление устанавливают по
манометру и оно не должно заметно снижаться в течение 1 мин.
При ослаблении посадки седла клапана в гнезде его выпрессовывают, а отверстие растачивают для установки седла ремонтного размера. При выпрессовке применяют различные съемники. На рис. 78 показана одна из применяемых конструкций съемников.
Ремонт поршня. Основными дефектами поршня являются нагар на днище и канавках, износ канавок под кольца, отверстий в бобышках, трещины и царапины на стенках.
Для очистки канавок поршня от нагара применяют приспособление в виде стальной ленты с рукоятками, на внутренней поверхности которого закреплены резцы. Вставляя резцы в канавку и поворачивая приспособление вокруг поршня, удаляют нагар.
Поршни с изношенными канавками под
поршневые кольца заменяют новыми соответствующих размеров.
Изношенное отверстие в бобышках поршня восстанавливают развертыванием с последующей установкой поршневого пальца увеличенного размера. Незначительные риски или царапины на наружной поверхности поршня удаляют зачисткой наждачной шкуркой. Поршни с трещинами и глубокими царапинами заменяют на новые.
Подбор поршневых колец. Изношенные и потерявшие упругость поршневые кольца заменяют новыми. Подбор новых колец производят в соответствии с размерами поршня и цилиндра. При подборе к поршню кольца (рис. 79,а) производят прокатку его по канавке и если нет заеданий, то щупом определяют зазор. В случае заедания кольца в канавке или малого зазора кольцо шлифуют на листе мелкозернистой наждачной бумаги, положенной на поверочную плиту. Величина зазора по высоте канавки не должна превышать 0,052—0,082 мм для верхнего и 0,035— 0,70 мм — для остальных компрессионных колец.
При подборе по цилиндру (рис. 79, б) определяют зазор в стыке кольца, установленного в цилиндр. Кольцо можно устанавливать в калибр, внутренний диаметр которого равен
диаметру цилиндра. При отсутствии или малой величине зазора осуществляют подпиливание стыков колец личным напильником. При этом плоскости стыков колец должны быть параллельны. Техническими условиями установлена для каждого двигателя определенная величина зазора. Для компрессионных колец зазор должен быть 0,3—0,5 мм, а для малосъемных колец —0,15—0,45 мм. При зазоре больше нормального кольца бракуются.
Ремонт поршневого пальца. Изношенные поршневые пальцы восстанавливают хромированием. Осуществляют наращивание пористого хрома, который хорошо удерживает масло. После нанесения слоя хрома пальцы шлифуют под необходимый 'размер. При износе по диаметру более 0,03 мм пальцы ремонтируют или заменяют новыми. Рекомендуется при капитальном ремонте двигателя устанавливать поршневые пальцы только номинального размера. Для облегчения сборки их размеры рассортированы на ряд групп.
Ремонт шатуна. Основными дефектами шатуна являются: изгиб и скручивание стержня, износ отверстия втулки верхней головки и отверстия под втулку, износ отверстия и торцовых поверхностей нижней головки.
Изношенные втулки верхней головки шатуна обычно заменяют новыми. Иногда отверстие втулки растачивают или развертывают под увеличенный ремонтный размер поршневого пальца.
Изношенное отверстие головки под втулку восстанавливают обработкой под ремонтные размеры (шатуны двигателей ЯМЗ-236 и ЯМЗ-238) или шатуны с данным дефектом выбраковывают (шатуны двигателей ЗИЛ-130, ЗИЛ-164, ГАЗ-51).
Отверстие нижней головки шатуна под вкладыш растачивают и шлифуют под номинальный размер после обработки стыковых поверхностей крышки с шупом. Последние фрезеруют или шлифуют, используя специальные приспособления. При наличии гальванического участка целесообразно отверстие нижней головки шатуна ремонтировать осталиванием. После осталивания отверстие восстанавливают до номинального размера. Этот метод ремонта позволяет сохранить жесткость детали и межцентровое расстояние между отверстиями верхней и нижней головок шатуна.
Изгиб и скручивание стержня шатуна устраняют правкой. Для правки и контроля шатунов применяют различные приспособления. На рис. 80 показана одна из конструкций применяемых приспособлений. На данном приспособлении одновременно проверяют изгиб и скручивание шатуна, а также расстояние между центрами его головок. При обнаруженных отклонениях, превышающих допустимые величины, шатун правят специальным ключом без снятия с приспособления. При этом верхняя головка шатуна должна занимать положение между вертикальной и горизонтальной плитами.
Шатун плотно устанавливается в приспособлении при помощи большой скалки 8; пропущенной через стойки 9. Малую скалку 10 вставляют в обработанное отверстие верхней головки шатуна. Вначале предварительно проверяют скрученность шатуна. Для этого шатун, установленный в горизонтальном положен ним, вручную поворачивают так, чтобы малая скалка 10 поочередно упиралась на сухари стоек 11. Наличие зазора укажет о скручивании шатуна.
Определение величины скручивания и изгиба производится при нахождении шатуна в вертикальном положении. При этом малая скалка 10, соприкасаясь с упорами коромысла 4, находится в контакте с штифтами 2 индикаторов / и 7, которые указывают величину скрученности шатуна. Индикатор 5 устанавливает отклонение расстояния между осями отверстий верхней и нижней головок, а индикатор 6 — непараллельность осей отверстий.
После правки и контроля, резко перемещая рукоятку 13, выбивают большую скалку 8, освобождая шатун.
Перед началом работы индикаторы приспособления настраивают по эталонному шатуну.
Ремонт коленчатого вала. Основными дефектами коленчатого вала являются: изгиб, износ шатунных и коренных шеек, износ отверстия под подшипник ведущего вала коробки передач и отверстий фланца вала под болты крепления маховика.
Изгиб коленчатого вала двигателя проверяют на стенде, на призмах, установленных на контрольной плите или в центрах токарного станка при помощи индикатора. Изгиб (биение средней коренной шейки относительно крайних) свыше допустимого по техническим условиям устраняют правкой на прессе.
Коленчатый вал устанавливают на призмы крайними коренными шейками, а штоком пресса через медную или латунную прокладку давят на среднюю шейку со стороны, противоположной изгибу. При этом величина прогиба должна быть примерно в 10 раз больше устраняемого изгиба. Вал выдерживают под нагрузкой на прессе в течение 2—4 мин. После правки рекомендуется вал подвергнуть термической обработке, т.е. нагреть до 180—200°С и выдержать при этой температуре в течение 5—6 ч. Затем вал проверяют на биение. Биение средних шеек по отношению к крайним шейкам не должно превышать 0,05 мм.

В тех случаях, когда использованы все ремонтные размеры и дальнейшее уменьшение диаметра вала недопустимо, а прочность его достаточна, шейки можно восстанавливать наплавкой с последующей обработкой под номинальный размер.
При восстановлении шеек коленчатого вала важна правильно выбрать установочные базы. Рекомендуется устанавливать коленчатый вал на станке на те же базовые поверхности, которые применялись при изготовлении. Тогда получаются минимальные погрешности, связанные с его установкой. В конструкциях коленчатых валов двигателей ЗИЛ-130, ГАЗ-53, ЯМЗ-236 и других предусмотрены фаски с двух сторон (со стороны отверстия под храповик и отверстия под шариковый подшипник направляющего конца ведущего вала). Данные фаски принимают в качестве установочных баз. Предварительно их проверяют и при необходимости зачищают или исправляют.
В конструкциях коленчатых валов двигателей ГАЗ-51, ЗИЛ-164 центровые отверстия, используемые при изготовлении, в последующем удаляются. Поэтому необходимо при шлифовании шеек коленчатого вала правильно выбрать новые установочные базы, которые бы удовлетворяли предъявляемым требованиям. Для таких валов можно принимать за установочные базы: при шлифовании .коренных шеек — фаску отверстия под храповик и отверстие под подшипник направляющего конца ведущего вала, при шлифовании шатунных шеек— шейку под шестерню и наружную цилиндрическую поверхность фланца под маховик. Для обеспечения требуемой точности обработки выбранные установочные поверхности предварительно подготавливают.
В качестве технологической базы могут быть приняты прошлифованные коренные шейки при шлифовании шатунных шеек. При этом ось вращения шатунных шеек должна точно совпадать с осью шпинделя станка.
Износ отверстия под подшипник ведущего вала коробки передач восстанавливают постановкой втулки. На рис. 81 приведен эскиз восстановленного коленчатого вала двигателя ЗИЛ-130, На токарно-винторезном станке растачивают отверстие в вале до диаметразатем запрессовывают ремонтную
втулку до упора, растачивают отверстие во втулке до размера 52и снимают фаску 3X30°
Изношенное отверстие во фланце вала под болты крепления маховика обрабатывают разверткой до ремонтного размера в сборе с маховиком. При сборке ставят болты крепления маховика увеличенного ремонтного размера.
После ремонта необходимо осуществить контроль коленчатого вала для установления качества выполненных работ и выявления возможных раковин и трещин.
Замена подшипников. Подшипники для шатунных и коренных шеек коленчатого вала изготовлены в виде стальных тонкостенных вкладышей, с внутренней стороны залитых антифрикционным сплавом. Заводы выпускают вкладыши как номинального, так и ремонтного размеров. При износе их осуществляют замену вкладышей без какой-либо дополнительной подгонки. Вкладыши заменяют только парами.
www.toira.ru
Испытание и сдача М после ремонта
Количество просмотров публикации Испытание и сдача М после ремонта - 152
Процесс сборки
ОБЩАЯ СБОРКА, ИСПЫТАНИЕ И СДАЧА МАШИН ПОСЛЕ РЕМОНТА
При капитальном ремонте М собирают поточным способом. Сущность и преимущества этого способа подробно рассмотрены при описании процесса разборки.
Процесс общей сборки состоит в установке на отремонтированную и окрашенную раму (базовый агрегат) в определенной последовательности собранных, испытанных и окрашенных агрегатов и узлов.
На сборку М, так же как и на сборку узлов и агрегатов, разрабатывают технологический процесс и оформляют технологические карты. Сборка выполняется согласно техническим условиям на ремонт, сборку и испытание М. Сборка М осуществляется на конвейере прерывного действия (см. § 5).
Процесс сборки начинается с укладки на конвейер рамы автомобиля (или задний мост трактора) в перевернутом положении. Далее на раму ставят передний и задний мосты в сборе с рессорами и соединяют их с рамой. Раму в сборе с подсоединенными мостами переворачивают с помощью специального кантователя. После этого устанавливают карданную передачу, двигатель в сборе с коробкой передач и рулевой механизм, а затем кабину, радиатор и оперение. На последнем посту автомобиль заправляют водой, бензином и маслом и направляют его на испытание.
Для проверки качества сборки М испытывают на специальном испытательном стенде или пробегом. Испытание на стенде имеет ряд существенных преимуществ перед испытанием пробегом.
При испытании пробегом возникают известные трудности, связанные с погодными условиями в различные времена года (дождь, грязь, снег, гололед и т. д.). Качество проверки в данном случае во многом зависит и от квалификации испытателя.
Испытание на стенде производят в закрытом помещении. Использование различных приспособлений и приборов позволяет всесторонне проверить М в соответствии с техническими условиями на ремонт, сборку и испытание. Вместе с тем, на стенде значительно сокращается продолжительность испытания.
Стенд для испытания автомобилей после сборки представляет собой сварную раму , на которой смонтированы четыре пары барабанов. Две пары смонтированы на задних мостах автомобиля, из которых удалёны главные передачи и дифференциалы, две другие установлены свободно на кожухах полуосей заднего моста автомобиля. Барабаны оборудованы тормозными механизмами с дистанционным гидравлическим приводом. Передние барабаны на своей цилиндрической поверхности с левой стороны имеют выступы, предназначенные для имитации движения испытуемого автомобиля по булыжной мостовой.
Автомобиль устанавливают колесами на барабаны стенда. Задние пары барабанов получают вращение от колес испытуемого автомобиля. Передняя пара барабанов приводится во вращение с помощью клиноременной передачи, которой они соединены с задними барабанами. Для отвода выхлопных газов имеется вытяжная труба, которая устанавливается на нужной высоте и затем убирается с помощью пневматического цилиндра. Для предотвращения схождения автомобиля с барабанов во время испытания имеются пневматические упорные щитки. Боковые ролики предохраняют автомобиль от бокового схождения.
При соприкосновении колес испытуемого автомобиля с правой гладкой стороной барабанов имитируется спокойная езда по гладкой дороге с асфальтовым покрытием; при переходе же колес на левую сторону барабанов с выступающими шипами условия испытания автомобиля соответствуют движению по булыжной мостовой. Переход колес автомобиля с одной стороны барабанов на другую во время испытания осуществляется незначительным поворотом рулевого колеса.
Нагрузка автомобиля при испытании создается затормаживанием барабанов с помощью тормозных механизмов.
Испытание автомобиля пробегом производят на расстояние 30 км с нагрузкой, равной 75% номинальной грузоподъемности. При этом дорога должна быть с твердым покрытием и скорость — не более 30 км/ч на прямой передаче.
Режим испытания устанавливается техническими условиями. Трогание автомобиля с места не должно вызывать резкого повышения числа оборотов коленчатого вала двигателя. При прогретом двигателе переход с малых оборотов на большие не должен сопровождаться хлопками в карбюраторе и ʼʼвыстреламиʼʼ в глушителе. Переключение передач должно происходить легко и бесшумно.
Температура воды в системе охлаждения в период испытания должна быть в пределах нормы.
В процессе испытания и после него автомобиль подвергают тщательному контрольному осмотру. Все обнаруженные при этом дефекты заносятся в специальный обкаточный лист. Автомобиль вместе с обкаточным листом поступает на участок регулировки и устранения дефектов. В тех случаях, когда при устранении дефектов приходится вскрывать или заменять агрегаты, автомобиль подвергают повторным испытаниям. Объем последних зависит от характера дефекта и способа его устранения. В случае если в процессе устранения дефектов оказалось поврежденным лакокрасочное покрытие, автомобиль подвергают местному подкрашиванию.
После испытания и устранения дефектов производится окончательный осмотр и приемка автомобиля. Гибкий вал спидометра, ограничительная шайба между фланцами карбюратора и впускной трубы, картеры двигателя, коробки передач и заднего моста должны быть опломбированы. На каждый отремонтированный автомобиль наносят паспортную табличку, в которой указывается авторемонтный завод, номер шасси, номер двигателя и дата приемки автомобиля из ремонта. Принятый автомобиль направляют на склад готовой продукции.
Автомобили после капитального ремонта предъявляются заказчику ʼʼна ходуʼʼ. Перед выдачей из капитального ремонта автомобили подвергаются осмотру и проверке представителем заказчика без разборки агрегатов, узлов и механизмов. Сдача автомобиля заказчику оформляется приемо-сдаточным актом. При этом вместе с автомобилем выдается паспорт установленной формы. Авторемонтный завод гарантирует в течение шести месяцев со дня приемки из ремонта нормальную работу легковых и грузовых автомобилей с пробегом до 15 000 км и автобусов — до 20 000 км при условии соблюдения заказчиком всех правил эксплуатации автомобиля.
В случае обнаружения в течение гарантийного срока неисправностей в автомобилё, возникших не по вине заказчика, при условии целости пломб, установленных ОТК завода, заказчик предъявляет заводу рекламационный акт. Ремонтный завод обязан в трехдневный срок произвести замену неисправных агрегатов, указанных в рекламационном акте, или автомобиля в целом.
Ремонтный завод не принимает претензий и рекламаций в случае:
а) снятия ограничительной шайбы карбюратора при пробеге автомобиля менее 1000 км;
б) отсутствия акта на снятие ограничительной шайбы, составленного по установленной форме;
в) вскрытия двигателя и других агрегатов М, в которых обнаружены дефекты, без участия представителя ремонтного завода или соответствующей инспекции.
referatwork.ru
9.3. Испытание и выдача автомобилей из ремонта
После сборки автомобиль поступает на контроль и испытание. Контроль и испытание автомобиля проводят для проверки комплектности, качества сборочных, регулировочных и крепежных работ, проверки работы и технического состояния всех агрегатов, механизмов и приборов, дополнительной регулировки, а также для выявления соответствия технических показателей требуемым техническим условиям. Испытания проводят на стенде с беговыми барабанами. Стенд позволяет проверить работу двигателя, агрегатов трансмиссии и ходовой части, а также оценить основные эксплуатационно-технические качества автомобиля (мощность двигателя, тяговое усилие на ведущих колесах, расход топлива на различных скоростных и нагрузочных режимах, путь и время разгона до заданной скорости, потери мощности на трение в агрегатах и ходовой части, наибольший допустимый тормозной путь с определенной скоростью), проверить и отрегулировать установку углов управляемых колес и т.д. Все выявленные при испытании неисправности необходимо устранить.
В дополнение к стендовым испытаниям каждый грузовой автомобиль после капитального ремонта должен пройти испытание пробегом на расстояние 30 км с нагрузкой, равной 75 % номинальной грузоподъемности, при скорости не более 30 км/ч, для проверки на управляемость, а также для дополнительного определения соответствия технического состояния автомобиля требуемым техническим нормам на различных режимах работы и в различных дорожных условиях. При пробеге проверяют также исправность и надежность работы всех систем, механизмов и соединений
.
После испытания пробегом автомобиль тщательно осматривают. Все выявленные пробегом и осмотром дефекты устраняют. При отсутствии дефектов (или после их устранения) автомобиль поступает на окончательную окраску, а затем предъявляется отделу технического контроля (ОТК). На принятом ОТК автомобиле (на передней панели кабины под капотом) ставят приемочное клеймо.
Качество отремонтированных автомобилей должно соответствовать техническим условиям на сдачу в КР и выдачу из ремонта автомобилей, их агрегатов и узлов. На каждый выпускаемый из ремонта автомобиль заказчику выдается паспорт этого автомобиля, в котором фиксируется комплектность, техническое состояние и соответствие отремонтированного автомобиля техническим условиям. Технические условия устанавливают гарантированную исправную работу автомобиля в течение определенного времени и до определенного пробега за этот период. Эти сроки службы и пробеги гарантированы при условии эксплуатации автомобилей в соответствии с «Положением о техническом обслуживании и ремонте подвижного состава автомобильного транспорта» и инструкциями заводов-изготовителей. В течение гарантийного срока все обнаруженные заказчиком неисправности по вине АРП должны быть устранены безвозмездно в течение трех суток со дня предъявления рекламации. Карбюраторные двигатели отремонтированных автомобилей в целях ограничения нагрузки на период обкатки снабжают запломбированной ограничительной шайбой, снимать которую в эксплуатации нужно в строгом соответствии с правилами, установленными для новых двигателей.
В настоящее время установлен гарантийный срок эксплуатации автомобилей — 12 мес со дня выдачи из ремонта при пробегах (для первой категории эксплуатации): не более 20 тыс. км — автобусами; не более 16 тыс. км — прочими автомобилями всех видов и назначений.
Гарантийный срок хранения отремонтированных составных частей автомобилей 12 мес с момента выдачи из ремонта при условии соблюдения правил консервации и хранения.
При выпуске автомобиля из КР к нему прилагаются следующие документы:
паспорт автомобиля с отметкой АРП о произведенном ремонте, указанием даты выпуска из ремонта, новых номеров шасси и двигателя, а также основного цвета окраски;
инструкция по эксплуатации с указанием особенностей эксплуатации отремонтированных автомобилей в обкаточный и гарантийный периоды, а также периодов и организации устранения дефектов в гарантийный период;
При выпуске двигателя из КР к нему прилагаются: паспорт; инструкция по эксплуатации с указанием особенностей установки и эксплуатации двигателя в обкаточный и гарантийный периоды.
Выпуск из КР автомобилей, их составных частей и деталей (комплектов деталей) оформляется приемо-сдаточным актом.
studfiles.net