Ссср свечи зажигания
Свечи Ссср - OLX.ua
свечи СССРАвтозапчасти и аксессуары » Автозапчасти | ||
Макеевка Вчера 18:32 |
50 грн. Договорная | ||
Кривой Рог, Дзержинский 20 нояб. |
www.olx.ua
Как делают свечи зажигания | Журнал Популярная Механика
Технологию производства свечей зажигания мы изучали на единственном в России заводе данного профиля, ныне принадлежащем компании Robert Bosch и недавно переоборудованном на современный лад.
На левом берегу Волги прямо напротив Саратова стоит небольшой, но интересный промышленный город Энгельс. Здесь находится единственный в России аэродром, на котором базируются тяжелые бомбардировщики Ту-160. Троллейбусы, на которых каждый из нас ездил, тоже делаются здесь, на заводе «ТролЗа». Кроме них в Энгельсе делают железнодорожные вагоны, газовое оборудование, трубы, спецавтомобили и многое другое. Вот и «свечной заводик» Bosch прописался здесь, забор в забор с производителем троллейбусов.
На проходной на нас укоризненно глядит бюст старика с окладистой бородой. Он смахивает на Фридриха Энгельса, и кажется, что мы оказались в прошлом веке, когда это головное предприятие СССР по свечам зажигания называлось «Заводом автотракторных запальных свечей» (ЗАЗС). Но все оказывается с точностью до наоборот. В скульптуре увековечен не столп мирового коммунизма, а Роберт Бош, основатель компании, образцовый капиталист. Что касается завода, теперь он называется Bosch-Eng.
Критический взгляд легендарного немецкого инженера легко объясняется, достаточно прочитать его изречение рядом на стене: «Для меня невыносима мысль, что при проверке моей продукции будет доказано, что я произвел что-то с отклонением от стандарта. Поэтому я всегда старался производить только такие товары, которые выдержат любую проверку, то есть лучшее из лучшего». Роберт Бош был в первую очередь изобретателем и лишь затем менеджером, но качество он ставил во главу угла. В любой стране мира, в том числе и в России, этот принцип должен соблюдаться.
Выпечка по‑крупному
Технологический процесс изготовления свечей разбит на три блока: керамическое и металлическое производство плюс сборка. Необходимое условие — пространственное разделение участков металла и керамики. Если хотя бы малая толика металла попадет в компаунд, из которого делаются изоляторы, свечи не пройдут испытания на электрический пробой. Поэтому сборочный участок расположен в середине здания, а металлический и керамический — по разные стороны от него. Это позволяет сократить перемещения заготовок до минимума и обеспечить изоляцию металлического участка от керамического.На практике таких эксцессов на заводе не помнят, но считают, что предотвращать надо даже теоретические риски. Сейчас на Bosch-Eng вводят дополнительные меры предосторожности: переходят на хранение порошка в герметичных контейнерах. Это, кстати, местная инициатива, исходящая от русских сотрудников, обученных работать по немецкой системе. Высушенный порошок попадает в пресс с резиновой матрицей, где из него под давлением 400−500 бар формируется заготовка изолятора, держащая форму, но хрупкая, как мел. Твердой она станет после обжига в печи при температуре 1600 °C.
Сама печь — это длинный тоннель, разбитый на участки с разной температурой. По тоннелю движется поезд из вагонеток, загруженных керамическими контейнерами (капселями). В них уложены хрупкие заготовки, по 10?000 в каждой вагонетке. В печи они проведут около 30 часов, пройдя несколько ступеней нагрева и затем плавного остывания. Вагонетки идут непрерывным потоком: с одного конца въезжают, с другого выезжают. За год обжиг проходят около 50 млн изоляторов.
Под пресс!
Самые важные металлические детали свечи — это стальные корпус и контактный стержень, медные центральный и боковой электроды. Все они изготавливаются из проволоки, и на металлическом участке можно увидеть, сколь разнообразны ее профили и размеры (завод производит несколько типов свечей зажигания, отличающихся формой и материалом электродов).Мастер многозначительно кивает на рулоны стальной проволоки толщиной в мизинец взрослого человека. Ее режут на короткие цилиндры, а затем робот-пресс за шесть ударов превращает их в корпуса свечей. Сила ударов достигает 250 тс, и под таким воздействием металл становится текучим, как пластилин. За минуту робот-пресс делает 120 деталей. Энергия и частота ударов таковы, что сравнить их можно с быстрым движением поезда, вагоны которого нагружены в пять-десять раз больше обычного. Но вибрация и шум в цехе невелики, поскольку станок хорошо сбалансирован.
Этот участок производства самый грязный: под ногами солидный слой машинного масла, смешанного с грязью. Температура в момент удара очень высокая, объясняет мастер, поэтому без масла не обойтись, и технологи пока не знают, как предотвратить его потери. Периодически масляно-грязевую массу собирают с пола и утилизируют, превращая в топливо.
После пресса корпус свечи требует небольшой доработки на автоматизированном токарном станке с ЧПУ. Затем, опять же на роботизированных станках, к нему за доли секунды приваривается боковой электрод, наносится клеймо и накатывается резьба. В заключение он покрывается никелем. Примерно так же, с помощью нескольких штамповочных, сварочных и гальванических операций, изготавливаются контактный стержень и центральный электрод.
Место встречи
Сборочные операции разбиты на два этапа: сборка сердечника и окончательная сборка. Здесь тоже трудятся станки-автоматы весьма причудливого вида. Первый станок совершает сразу несколько операций: наносит на изолятор надписи и герметик, окунает в глазурь, вставляет контактный стержень и центральный электрод, а в конце вторично обжигает, чтобы глазурь затвердела. Получившаяся деталь называется сердечником свечи.На заводе Bosch-Eng изготавливается несколько десятков типов свечей, сильно варьирующихся по характеристикам электрической прочности и долговечности. Резонно возникает вопрос: чем на уровне технологии отличаются свечи разных моделей? Оказывается, что только материалами: технологический процесс одинаков для всех.
Вкалывают роботы… и человек
Справочник Б. Басса «Свечи зажигания» сообщает, что в СССР было четыре завода, выпускавших свечи зажигания, хотя только ЗАЗС был узкоспециализированным, производившим до 40% готовых изделий. Уже тогда он занимал исключительное положение: тут свечи разрабатывались и впервые внедрялись в производство. Здесь же монопольно изготавливались изоляторы для всех заводов Союза. В музее Bosch-Eng можно увидеть первые свечи для ВАЗ, ЗиЛ и УАЗ, свечи для уникальных вазовских роторных движков.Сейчас Bosch-Eng остался один на все страны бывшего постсоветского пространства. Две из трех свечей, сделанных в Энгельсе, уходят на экспорт — примерно 35 млн штук в год. Внешне завод практически не изменился со времен СССР: немцы говорят, что здания построены хорошо и перестраивать ничего не нужно. Внутри же его не узнать. Производство свечей стало гораздо компактнее: изначально оно занимало три корпуса, но инженеры Bosch заново спроектировали линию, уместив ее в один цех; освободившуюся площадь использовали под производство других деталей, например электронной педали газа для Lada Granta и топливной рампы.
Технология также изменилась кардинально. Революция на участке металлообработки связана в первую очередь с масштабной заменой токарной обработки на штамповку — отходы металла, расход энергии и времени сократились на порядок. Кругом роботы, роботы… это вторая часть технологического переворота. Без роботов был бы невозможен значительный рост качества и производительности. Примечательно, что это не привело к сокращению численности персонала: сейчас на заводе в Энгельсе даже немного больше работников, чем было до модернизации. Просто на той же территории изготавливается в разы больше продукции.
«Когда мы сможем отказаться от свечей, перейдя, например, на лазерное зажигание?» — задал я вопрос перед отъездом с завода. Руководитель керамического производства Bosch-Eng Антон Носов ответил, что работа над лазерным зажиганием интенсивно ведется, но эта технология пока далека от практики и никто в компании не осмеливается назвать сроки начала производства. Известно лишь, что завод еще как минимум десять лет сохранит свою историческую специализацию.
У свечей зажигания впереди долгие годы службы. А раз так, то и работа по улучшению технологии их производства не закончена.
Керамическое производство
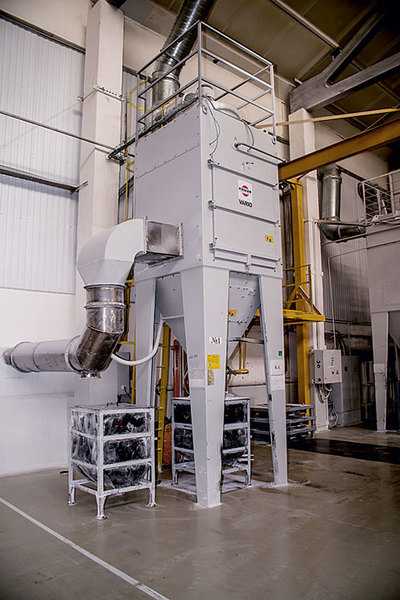
Этап 1
Огромная мельница превращает глинозем с присадками и воду в керамический порошок.

Этап 2
Высушенный порошок попадает в формы, где под давлением превращается в заготовки изоляторов. Заготовки укладываются в капсели.
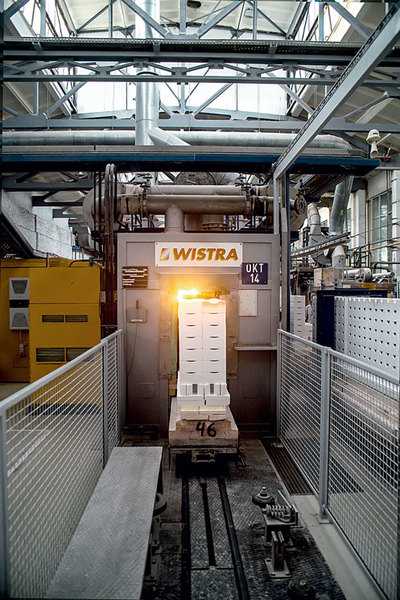
Этап 3
Вагонетки с капселями поступают в печь, где проходят несколько стадий нагрева и плавного остывания.
Металлическое производство
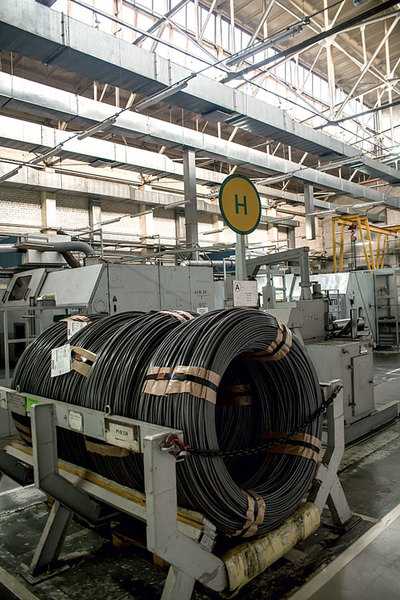
Этап 1
Проволока толщиной в мизинец будет распилена на цилиндры, из которых пресс сформирует корпуса свечей.
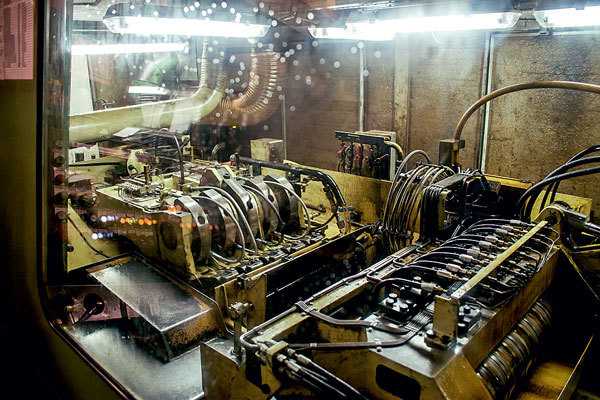
Этап 2
Каждую секунду пресс выдает два корпуса для свечей.
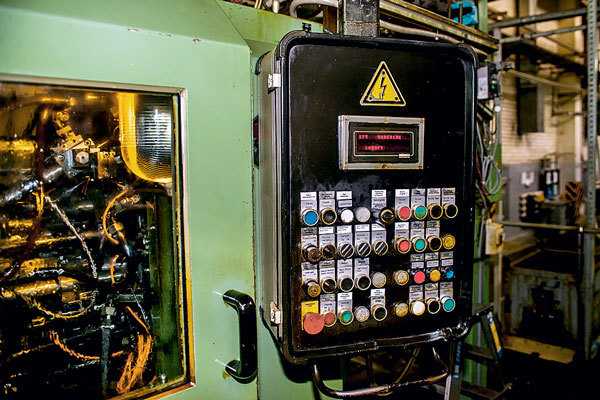
Этап 3
Станки с ЧПУ обрабатывают поверхность корпусов, нарезают резьбу, приваривают боковой электрод и ставят клеймо.

Этап 4
Готовые корпуса покрывают никелем.
Сборочное производство

Этап 1
На начальном этапе сборки изоляторы покрывают розовой глазурью. После обжига она станет прозрачной.

Этап 2
В изоляторы вставляются контактные стержни и электроды.
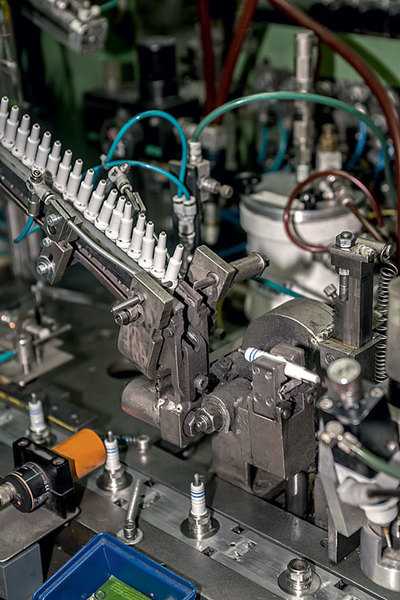
Этап 3
На завершающем этапе сборки стыкуются сердечник и корпус.
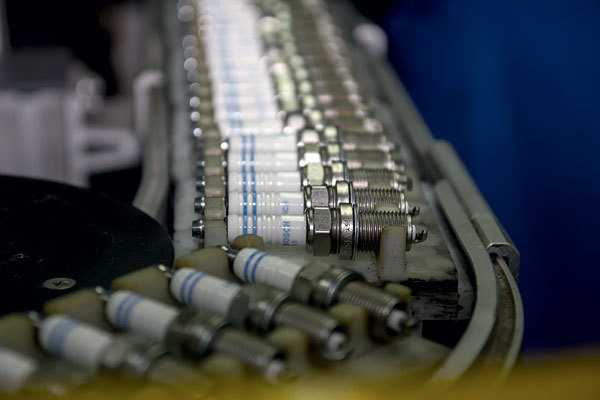
Этап 4
Готовые свечи поступают на автоматическую упаковочную линию.
Статья «Пока искрит свеча» опубликована в журнале «Популярная механика» (№3, Март 2015).www.popmech.ru
Свеча зажигания.История изобретения… | Jeep-Planet.com
Свеча зажигания это еще одна незаменимая деталь автомобиля, достойная внимания и целой статьи. Свеча зажигания родилась в те далекие времена, когда наука об электрическом токе только начинала зарождаться. Считается, что отцом первого прототипа свечи был Алессандро Вольта.
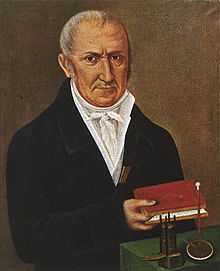
в 1800 году, Вольта впервые поместил пластины из цинка и меди в кислоту, чтобы получить непрерывный электрический ток, создав первый в мире химический источник тока («Во́льтов столб»). Именем Вольты названа единица измерения электрического напряжения — Вольт. Прототипом свечи можно назвать изготовление металлического стержня, помещенного внутрь глиняного изолятора, дабы разъяснить свойства электрического тока и его возможность изоляции от металла. Конечно, в те годы еще не было двигателей внутреннего сгорания, были лишь мысли и идеи о чём-то новом, о самостоятельном устройстве, способном вращать и передвигать определенный вес.
Спустя годы, бельгийский инженер Жан-Этьен Ленуар начал разработку своего первого двигателя внутреннего сгорания, работающего на светильном газе. Для получения искры, Ленуар разработал электрическую систему, основанную на свече зажигания, которая очень похожа на современную своей формой и принципом работы.
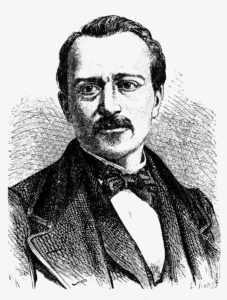
В 1860 году Ленуар оформил патент на изобретенный им двигатель и к 1885 году полностью доработал свою свечу. На основе своего прототипного двигателя, Ленуар создал новый двигатель для своей самобеглой повозки под весёлым названием- «Гиппомобиль», который появился задолго до автомобиля Бенца.
Свеча требовала постоянного обслуживания из-за замасливания и регулярно выходила из строя. Изолятор не мог долгое время выдерживать температуру и от перегревания разрушался.


В 1898 году, сразу три патента на изобретение и разработку систем искрообразования были оформлены Николой Тесла, Робертом Бошем и Фредериком Ричардом Симсом. Этот год можно уверенно назвать основой для современных свечей зажигания. Но лишь благодаря стараниям Готлиба Хоннельда, сотрудничавшего с Робертом Бошем в 1902 году на свет появилась свеча, способная работать в системе Магнето.
В начале 1900-х годов братья Роберт и Фрэнк Стрэннахан, занимавшиеся продажей автомобильных запчастей решили модернизировать свечу. Собрав необходимую информацию, свеча была отправлена на доработку. Изолятор изготовили из фарфора и было добавлено металлическое кольцо для уплотнения в месте посадки. В результате этих поисков и доработок, в 1908 году образовалась компания Champion, которую вы прекрасно знаете. Более 300 тысяч свечей нового поколения было приобретено компанией Ford и Triumph.

Существует легенда о неком Эдмонде Бергере, который придумал особый вид свечи, но пропал без вести, а свой рисунок оставил неизвестному инженеру одной из компаний, находившейся под крылом Champion. К сожалению, проверенных фактов нет, поэтому, это останется мифом…
Учитывая все изменения и прогресс в области создания двигателей внутреннего сгорания, свечи становились прочнее, долговечнее и красивее! Более ста лет назад, на пике автомобилестроения и развития электроприборов, появился главный символ жизни мотора-свеча, до сих пор являющаяся его неотъемлемой частью!
По материалам: Google Patents,Wikipedia,MadeHow,Champion,Bosch
jeep-planet.com
Свечи зажигания - краткий справочник
ОСНОВНЫЕ ПАРАМЕТРЫ СВЕЧЕЙ
На территории России свечи должны изготавливаться в общеклиматическом исполнении в соответствии с требованиями ОСТ 37.003.081-98 “Свечи зажигания искровые. Общие технические условия».
Свечи относятся к классу перемонтируемых, обслуживаемых в период эксплуатации изделий, они должны быть работоспособны при температуре окружающей среды от -45 до +100 ‘С.
ТЕХНИЧЕСКИЕ ТРЕБОВАНИЯ
Изолятор должен соответствовать требованиям ОСТ 37.003.036-87 «Изоляторы керамические для искровых свечей зажигания. Технические условия».
Металлические детали должны иметь оксидное или металлическое покрытие (цинковое или никелевое), на них не допускаются трещины и поврежденные нитки резьбы. На термоосадочной канавке и в местах наложения контактов на корпус при электротермической сборке допускается частичное нарушение покрытия.
Новообразование между электродами свечей с искровым зазором менее 0.6 мм должно быть бесперебойным при давлении газа, окружающего электроды, 1,0±0,05 МПа (10±0,5 кгс/смг). При искровом зазоре 0,6 мм и более давление газа должно быть 0.85*0,05 МПа (8,5±0,5 кгс/смг).
Свечи должны быть герметичны, суммарная утечка газа через соединение корпуса с изолятором и изолятора с центральным электродом при разнице давлений 2,0*0,05 МПа (20,0*0,5 кгс/смг) не должна превышать 5 см3/мин.
Свечи с плоской опорной поверхностью должны выдерживать следующие механические нагрузки:
крутящий момент 45 Н м (4,5 кгсм), приложенный к шестиграннику корпуса; усилие 400 Н (40 кгс), приложенное под прямым углом к контактной головке для свечей с размером шестигранника под ключ 20.8 мм; и 300 Н (30 кгс) при шестигранниках 16,0 и 19,0 мм;
растягивающую силу 300 Н, приложенную к контактной головке вдоль ее оси. Свечи с конической опорной поверхностью должны выдерживать следующие механические нагрузки:
крутящий момент 25 Н м (2,5 кгс м), приложенный к шестиграннику корпуса; усилие 300 Н (30 кгс), приложенное под прямым углом к контактной головке; растягивающую силу 300 Н (30 кгс), приложенную к контактной головке вдоль ее оси.
Боковой электрод должен быть надежно закреплен на корпусе. Свечи должны выдерживать без повреждений вибрационные и ударные нагрузки, возникающие на двигателе в процессе его работы.
Толщина уплотнительного кольца свечей с плоской опорной поверхностью должна быть от 1,4 мм до 2.0 мм после однократной затяжки усилием 30 Н м (3 кгсм).
Сопротивление изоляции между контактной головкой и корпусом при температуре 550± 15 *С должно быть не менее 5.0 МОм.
Допустимое отклонение калильного числа, установленное для данного типа свечи, не должно превышать ±10 %.
Изолятор для свечей с размерами шестигранника подключ 16,0 и 19.0 мм в сборе с электродом и контактной головкой должен выдерживать испытательное напряжение 18 кВ. При шестиграннике 20.8 мм изолятор должен выдерживать 22 кВ (действующее значение при частоте 50 Гц).
Конструкция свечей должна допускать очистку теплового конуса изолятора от нагара и регулирование искрового зазора.
КАЛИЛЬНОЕ ЧИСЛО
Прямое определение тепловой характеристики связано с необходимостью измерения температуры теплового конуса изолятора и электродов на работающем двигателе. Это сложная техническая проблема, так как требует установки в свечу миниатюрных термопар и защиту их от высокого напряжения. Такая работа требует огромных затрат и проводится только в исследовательских целях при доводке вновь разрабатываемых двигателей.
В связи с этим определение тепловой характеристики заменяют подбором свечей по верхнему температурному пределу. Для этого производятся тепловые ряды конструктивно одинаковых свечей с различными тепловыми характеристиками.
Каждую свечу теплового ряда испытывают на моторной испытательной установке, позволяющей за счет наддува моделировать тепловую напряженность двигателя с любой удельной мощностью, вплоть до самого форсированного спортивного. В процессе испытания величину наддува последовательно увеличивают. соответственно возрастает тепловая напряженность и основной характеризующий ее показатель — величина среднего индикаторного давления.
Калильное число — это величина среднего индикаторного давления, при котором в цилиндре двигателя при испытании свечи возникает калильное зажигание.
Основным конструктивным параметром, с помощью которого изменяют величину калильного числа, является длина теплового конуса изолятора. Чем длиннее тепловой конус изолятора, тем рабочая температура свечи больше, и наоборот, чем короче тепловой конус изолятора, тем температура меньше.
До 1974 г. свечи, производимые в СССР, имели в своей маркировке обозначение длины теплового конуса изолятора, выраженной в миллиметрах. Ветераны-автомобилисты помнят свечи с уралитовыми изоляторами для автомобиля «Запорожец» первых выпусков, которые имели маркировку А6УС или А7.5УС. свечи для автомобиля «Волга» ГАЗ-21 с маркировкой А14У. свечи А11У для автомобиля «Москвич-401- и многие другие. Интересно отметить, что на первые модели автомобилей ВАЗ ставились свечи с изолятором из керамики «боркорунд», также с маркировкой длины теплового конуса изолятора, сначала А6БС. затем А7.5БС. С появлением двигателей автомобилей ВАЗ-2101. ГАЗ-24, АЗЛК-412. ЗАЗ-966. ЗИЛ-130, ГАЗ-53 и других требования к свечам возросли. Выяснилось, что необходимо учитывать то, что рабочая температура свечи зависит не только от длины теплового конуса изолятора, но и от многих других конструктивных и технологических факторов. Ведь калильное число является интегральным показателем, характеризующим зависимость рабочей температуры свечи не только от длины теплового конуса, но и от других конструктивных факторов.
Каждой длине теплового конуса изолятора соответствует своя величина калильного числа. В соответствии с российским стандартом калильные числа следует выбирать из ряда 8, 11, 14, 17, 20. 23 и 26 условных единиц. Допускаются промежуточные значения, выраженные целыми числами.
С помощью калильных чисел различают более «горячие» и более «холодные» свечи. Эти понятия определены тем, что при установке на один и тот же двигатель «горячие» свечи в равных условиях имеют рабочую температуру выше, чем «холодные». Устанавливая последовательно на двигатель свечи с различными калильными числами, можно осуществить подбор по тепловой характеристике. Первым критерием подбора является отсутствие калильного зажигания при полной нагрузке двигателя. Вторым критерием является то. что ближайшая более «горячая» свеча вызывает калильное зажигание. Правильно подобранная свеча всегда должна иметь максимальную температуру, несколько ниже, чем температура калильного зажигания. При подборе к двигателю угол опережения зажигания устанавливают на 10-15′ раньше относительно установочного. Этим способом искусственно повышают рабочую температуру свечи, что обеспечивает гарантированный запас до верхнего температурного предела.
Зарубежные фирмы применяют свои шкалы калильных чисел, прямые и обратные. В прямых шкалах с увеличением длины теплового конуса калильное число возрастает, а в обратных уменьшается. Отечественная шкала калильных чисел едина для всех производителей в России и является обратной. Чем больше калильное число, тем короче при прочих равных тепловой конус, тем свеча -холоднее». В отличие от нашей страны, за рубежом каждая фирма применяет свою шкалу калильных чисел и свою систему маркировки свечей. Для определения соответствия по калильному числу свечей различных производителей приходится пользоваться таблицами взаимозаменяемости.
ГАБАРИТНЫЕ И ПРИСОЕДИНИТЕЛЬНЫЕ РАЗМЕРЫ
Эти размеры свечей должны соответствовать международным стандартам ISO (Международная организация по стандартизации). Поэтому весьма удобным для потребителей обстоятельством является то, что по своим размерам однотипные свечи, выпускаемые различными производителями, полностью взаимозаменяемы.
Свечи могут иметь плоскую или коническую опорную поверхность. Для герметизации соединения с головкой блока цилиндров двигателя свечей с плоской опорной поверхностью необходимо специальное уплотнительное кольцо, а при конической посадочной поверхности уплотнительное кольцо не требуется.
Размеры свечей определяются типом посадочного места, резьбой на корпусе. длиной резьбовой части корпуса и размером шестигранника под ключ.
УСТРОЙСТВО СВЕЧИ
При всем разнообразии конструкций, любая искровая свеча зажигания (рис.9) включает в себя керамический изолятор, металлический корпус, электроды и контактную головку для соединения с высоковольтным проводом.
Центральный электрод установлен в канале изолятора, имеющем переменный диаметр. Головка электрода опирается на коническую поверхность канала изолятора в месте перехода от большего диаметра к меньшему. Рабочая часть центрального электрода выступает на величину от 1.0 до 5.0 мм из изолятора. Закрепление электрода в канале изолятора и герметизацию этого соединения осуществляют с использованием стеклогерметика.
Он представляет собой смесь специального технического стекла и порошка металла. Стекло должно иметь коэффициент термического расширения одинаковый с этим коэффициентом у керамики.
В этом случае герметизирующая пробка не разрушится при изменениях температуры в процессе эксплуатации. Порошок металла (медь или свинец) добавляют в стекло для придания ему электрической проводимости,
Сборку сердечника (изолятора в сборе с центральным электродом и контактным стержнем) осуществляют в следующем порядке. Электрод устанавливают в канале изолятора и сверху засыпают порошкообразный стек- логерметик или укладывают его в виде таблетки Затем в канал изолятора устанавливают контактную головку. До запрессовки стеклогерметик занимает больший объем, чем после этой операции, и контактный стержень не может полностью войти в канал изолятора. Он примерно на треть длины выступает над изолятором. Заготовку нагревают до температуры 700-900 ‘С и с усилием в несколько десятков килограммов контактный стержень вводят в размягченный под воздействием температуры стеклогерметик. При этом он затекает в зазоры между каналом изолятора, головкой центрального электрода и контактной головкой. После остывания стеклогерметик затвердевает и надежно закрепляет обе детали в канале изолятора. Между торцами электрода и контактной головки образуется герметизирующая пробка высотой от 1,5 до 7,0 мм, полностью перекрывающая канал изолятора от прорыва газов.
В случае необходимости встроить в цепь центрального электрода электрическое сопротивление для подавления электромагнитных помех применяют резистивный стеклогерметик. После остывания герметизирующая пробка приобретает электрическое сопротивление необходимой величины.
Сердечник устанавливают в корпусе свечи так, что он соприкасается своей конической поверхностью с соответствующей поверхностью внутри корпуса. Между этими поверхностями устанавливают герметизирующую -теплоотводящую» шайбу {медную или стальную).
Закрепление сердечника осуществляют завальцовкой буртика корпуса на поясок изолятора. Герметизацию по соединению изолятор — корпус осуществляют методом осадки корпуса в нагретом состоянии (термоосадкой).
Боковой электрод -массы» прямоугольного сечения приваривают к торцу корпуса и изгибают в сторону центрального. На цоколь корпуса с упором в плоскую опорную поверхность устанавливают уплотнительное кольцо, предназначенное для герметизации соединения свеча — двигатель.
На резьбовую часть контактного стержня устанавливают контактную гайку, если это требуется конструкцией наконечника высоковольтного провода. В некоторых свечах контактный стержень не имеет резьбовой головки, она сразу же штампуется в форме контактной гайки.
ИЗОЛЯТОР
Для обеспечения бесперебойности искрообразования изолятор должен обладать необходимой электрической прочностью даже при высокой рабочей температуре. Напряжение, прикладываемое к изолятору в процессе работы двигателя. равно напряжению пробоя искрового зазора. Это напряжение возрастает с увеличением давления и величины зазора и уменьшается по мере возрастания температуры. На двигателях с классической системой зажигания используются свечи с искровым зазором 0.5-0,7 мм. Максимальная величина напряжения пробоя в этих условиях не превышает 12-15 кВ (амплитудное значение). На двигателях с электронными системами зажигания установочный искровой зазор составляет 0.8-1,0 мм. В процессе эксплуатации он может увеличиться до 1,3-1,5 мм (у обеих систем). При этом напряжение пробоя может достигать 20-25 кВ.
Конструкция изолятора относительно проста — это цилиндр с осевым отверстием для установки центрального электрода.
В средней части изолятора имеется утолщение, так называемый -поясок» для соединения с корпусом. Ниже пояска расположена более тонкая цилиндрическая часть — -дульце», переходящая в тепловой конус. В месте перехода от дульца к тепловому конусу расположена коническая поверхность, предназначенная для установки между изолятором и корпусом герметизирующей теплоотводящей шайбы. Выше пояска расположена -головка», а в месте перехода от пояска к головке расположено плечико под завальцовку буртика корпуса при сборке свечи.
Допустимая, с учетом коэффициента запаса прочности, толщина стенок определяется электрической прочностью материала изолятора. По отечественным стандартам изолятор должен выдерживать испытательное напряжение от 18 до 22 кВ (действующее значение), что больше амплитудного в 1.4 раза. Длина головки изолятора определяется напряжением поверхностного перекрытия и выполняется в пределах от 15 до 35 мм. У большинства автомобильных свечей эта величина около 25 мм. Дальнейшее увеличение малоэффективно и приводит к снижению механической прочности изолятора. Для исключения возможности электрического пробоя по поверхности изолятора его головку снабжают кольцевыми канавками (барьерами тока) и покрывают специальной глазурью для защиты от возможного загрязнения.
Функцию защиты от поверхностного перекрытия со стороны камеры сгорания выполняет тепловой конус. Эта важнейшая часть изолятора при относительно небольших размерах выдерживает без перекрытия по поверхности указанное выше напряжение.
Первоначально в качестве материала изолятора применяли обычный фарфор, но такой изолятор плохо сопротивлялся тепловому воздействию и имел низкую механическую прочность.
С увеличением мощности двигателей потребовались изоляторы более надежные. чем фарфоровые. Продолжительное время применяли слюдяные изоляторы. Однако при использовании топлив с присадкой свинца слюда разрушалась. Изоляторы снова стали изготавливать керамическими, но не из фарфора, а из особо прочной технической керамики.
Наиболее распространенной и экономически целесообразной для производства изоляторов является технология изостатического прессования, когда из заранее подготовленных компонентов изготавливают гранулы необходимого состава и физических свойств. Из гранул при высоком давлении прессуют заготовки изоляторов, шлифуют до необходимых размеров с учетом усадки при обжиге, а затем однократно обжигают.
Современные изоляторы изготавливают из высокоглиноземистой конструкционной керамики на основе оксида алюминия. Такая керамика, содержащая около 95% оксида алюминия, способна выдержать температуру до 1600 ‘С и имеет высокую электрическую и механическую прочность.
Важнейшим преимуществом керамики из оксида алюминия является то, что она обладает высокой теплопроводностью. Это существенно улучшает тепловую характеристику свечи, так как через изолятор проходит основной поток тепла, поступающий в свечу через тепловой конус и центральный электрод.
КОРПУС
Металлический корпус предназначен для установки свечи в двигатель и обеспечивает герметичность соединения с изолятором. К его торцу приваривается боковой электрод, а в конструкциях с кольцевым искровым зазором корпус непосредственно выполняет функцию электрода «массы».
Корпус изготавливают штамповкой или точением из конструкционных малоуглеродистых сталей.
Внутри корпуса имеется кольцевой выступ с конической поверхностью. на которую опирается изолятор. На цилиндрической части корпуса выполнена кольцевая проточка, так называемая термоосадочная канавка. В процессе сборки свечи верхний буртик корпуса завальцовывают на поясок изолятора. Затем его нагревают и осаживают на прессе, при этом термоосадочная канавка подвергается пластической деформации, и корпус плотно охватывает изолятор. В результате термоосадки корпус оказывается в напряженном состоянии, что обеспечивает герметичность свечи на весь срок службы.
ЭЛЕКТРОДЫ
Как сказано выше, для улучшения эффективности воспламенения электроды свечи должны быть как можно более тонкими и длинными, а искровой зазор должен иметь максимально допустимую величину. С другой стороны, для обеспечения долговечности электроды должны быть достаточно массивными.
Поэтому, в зависимости от требований к мощности, топливной экономичности и токсичности двигателей, с одной стороны, и требований к долговечности свечи с другой стороны, к каждому типу двигателя разрабатывалась своя конструкция электродов.
Появление биметаллических электродов позволило в определенной степени решить эту проблему, так как такой электрод имеет достаточную теплопроводность. В отличие от обычного «монометаллического» он при работе на двигателе имеет меньшую температуру и соответственно больший ресурс. В тех случаях, когда требуется увеличить ресурс, применяют два электрода «массы» (рис. 11). На свечах зарубежного производства с этой целью применяют три и даже четыре электрода. Отечественная промышленность выпускает свечи с таким количеством электродов только для авиационных и промышленных газовых двигателей. Следует отметить, что с увеличением числа электродов снижается стойкость к образованию нагара и затрудняется очистка от нагара.
К материалу электродов предъявляются следующие требования: высокая коррозионная и эрозионная стойкость; жаростойкость и окалиностойкость; высокая теплопроводность; достаточная для штамповки пластичность.
Стоимость материала нс должна быть высокой. Наибольшее распространение в отечественной промышленности для изготовления центральных электродов свечей зажигания получили жаростойкие сплавы: железо-хром- титан, никель-хром-железо и никель- хром с различными легирующими добавками
Боковой электрод «массы» должен обладать высокой жаростойкостью и стойкостью к коррозии. Он должен обладать хорошей свариваемостью с обычной конструкционной сталью, из которой изготавливают корпус, поэтому применяют сплав никель — марганец (например. НМц-5). Боковой электрод должен обладать хорошей пластичностью для обеспечения возможности регулирования искрового зазора.
С целью снижения гасящего влияния электродов при доработке свечей на электродах выполняют канавки, в электроде -массы» выполняют сквозные отверстия. Иногда боковой электрод разделяют на две части, превращая одноэлектродную свечу в двухэлектродную.
ВСТРОЕННЫЙ РЕЗИСТОР
Искровой разряд является источником электромагнитных помех, в том числе радиоприему. Для их подавления между центральным электродом и контактной головкой устанавливают резистор, имеющий при температуре 25±10 ‘С электрическое сопротивление от 4 до 13 кОм. В процессе эксплуатации допускается изменение величины этого сопротивления в диапазоне 2-50 кОм после воздействия температуры от -40 до +300 ’С и импульсов высокого напряжения.
ДОПОЛНИТЕЛЬНЫЙ ИЗОЛЯТОР
Даже небольшие потери энергии зажигания приводят к ослаблению искры со всеми неприятными последствиями; ухудшение пуска, неустойчивая работа на холостом ходу, потеря мощности двигателя, перерасход топлива, рост токсичности отработавших газов и т. д. Если поверхность изолятора покрыта нагаром, грязью или просто влагой, происходит утечка тока «на массу». Она обнаруживается в темноте в виде коронного разряда по поверхности изолятора. Утечка по загрязненной поверхности теплового конуса изолятора в каморе сгорания двигателя может привести к отказу в искрообразовании. Наиболее радикальнымспособом повышения электрической прочности изоляции является установка между корпусом и контактной головкой свечи дополнительного изолятора в виде керамической втулки. Таким образом, свеча приобретает двойную защиту от утечек тока «на массу».
Данное техническое решение защищено патентом и реализовано у нас в стране ЗАО «Автоконинвест» (Москва).
ФОРКАМЕРНЫЕ СВЕЧИ
Известны различные варианты устройства свечи, у которых рабочая камера выполнена в виде форкамеры. Их используют с целью улучшения сгорания рабочей смеси. Форкамерные свечи подобны свечам для спортивных форсированных двигателей, где электроды для защиты от перегрева установлены глубоко внутри рабочей камеры корпуса. Отличие заключается в том. что отверстие. соединяющее рабочую камеру (форкамеру) с цилиндром двигателя, делают специальной формы. При сжатии свежая смесь поступает в форкамеру, искровой разряд возникает в области вихревого потока, и образование первичного очага воспламенения становится интенсивнее. Благодаря этому обеспечивается быстрое распространение пламени в форкамере. Давление быстро возрастает и выбрасывает факел пламени, проникающий в камеру сгорания двигателя и интенсифицирующий воспламенение даже сильно обедненной рабочей смеси.
При перетекании горящих газов из форкамеры в цилиндр двигателя, в связи с турбулизацией горючей смеси, ускоряется и становится более эффективным процесс сгорания. Это. в свою очередь, может привести к улучшению показателей, характеризующих топливную экономичность и токсичность отработавших газов.
Недостатки форкамерных свечей заключаются в том, что велико гасящее влияние электродов, а стойкость к образованию нагара мала. Вентиляция форкамеры затруднена и горючая смесь в ней содержит повышенное количество остаточных газов. При перетекании горящих газов из форкамеры в цилиндр возникают дополнительные тепловые потери. Один из вариантов форкамерной свечи представлен на рис.
Страницы: 1 2 3
www.avtodiagnostika.info
Свечи зажигания: описание, характеристики, разновидности, выбор,цены
Свеча зажигания — устройство для поджига топливо-воздушной смеси в бензиновых двигателях внутреннего сгорания. Поджиг производится электрическим разрядом напряжением в несколько тысяч или десятков тысяч вольт, возникающим между электродами свечи.
Свеча зажигания является решающим фактором в определении оптимальной работы и надежного функционирования бензинового двигателя. Задачей свечи зажигания является подача высокого напряжения, генерированного в катушке зажигания, к камере сгорания, и воспламенение топливно-воздушной смеси. Между тем, свеча зажигания является предметом чрезвычайных и часто изменяющихся режимов работы, таких как "прекращение и начало" дорожного движения в городе или вождение по автострадам на полном газу.
Требования к современным свечам зажигания:
надежная работа при высоких напряжениях (до 40,000 вольт),
хорошие изоляционные свойства (при температуре в 1000 °С),
сопротивляемость химическим процессам в камере сгорания и агрессивным отложениям,
сопротивляемость тепловому удару,
изолятор и электроды должны обладать хорошей теплопроводностью.
Мало кто из автолюбителей придает особое значение выбору свечей зажигания. Однако свечи являются важнейшим элементом системы зажигания, ведь от устойчивости и своевременности искрообразования зависит стабильность работы всего двигателя. К основным характеристикам свечи можно отнести: калильное число, способность к самоочищению, величину искрового промежутка, число боковых электродов, срок службы, тепловую характеристику свечи и рабочую температуру свечи. Теперь обо всем этом подробно.
Основные характеристики
Калильное число
Первое, на что следует обращать внимание при выборе, — это калильное число. Данный параметр является условным и показывает, при каком давлении в цилиндре двигателя возникает калильное зажигание – воспламенение смеси не от искры, а от контакта с нагретыми участками свечи. Калильное число выбранной свечи должно строго соответствовать рекомендованному для вашего двигателя. Допускается непродолжительное использование свечей с несколько большим значением калильного числа, но категорически запрещается использовать свечи с меньшим значением, так как это может привести к самым печальным последствиям, вплоть до пробоя прокладки головки блока цилиндров, прогорания поршней, клапанов и т. д.
Способность к самоочищению
Тоже является условной характеристикой, не поддающейся количественной оценке. В процессе работы двигателя часть продуктов сгорания топливовоздушной смеси осаждается на поверхности камеры сгорания, поршнях и на тепловом конусе свечи.
Практически все производители говорят о том, что их свечи обладают высокой способностью к самоочищению, однако проверить правдивость подобных заявлений можно только на практике. В идеале свеча, прогревшаяся до рабочей температуры, вообще не должна покрываться нагаром, однако в реальных условиях добиться этого невозможно.
Теперь настала пора поговорить о том, чем вреден образовавшийся нагар.
Искровой промежуток
Это расстояние между центральным и боковым электродами. Для каждого типа свечей завод-изготовитель устанавливает определенный зазор, и дальнейшая его регулировка не предусмотрена. Если же вы каким-то образом изменили его величину, то «бюджетный» вариант решения проблемы – восстановление первоначального зазора, разумный — замена свечи.
Число боковых электродов
Классическая конструкция свечи предполагает один центральный электрод и один боковой. Однако некоторое время назад производители начали изготавливать двух-, трех- и даже четырехэлектродные модели. Бытует ошибочное мнение, что в процессе их работы образуются две, три и четыре искры соответственно. Это неверно. Просто искрообразование становится устойчивее, обуславливая более стабильную работу двигателя в режиме малых оборотов, улучшается процесс поджига смеси и, наконец, увеличивается срок службы самого изделия.
Недавно в продаже появились свечи вообще без боковых электродов, роль которых выполняют дополнительные, расположенные на изоляторе. Вот при такой конструкции как раз и возникает несколько разрядов, причем не все сразу, а по очереди, образуя тем самым «гуляющую» искру. Подобные конструкции являются весьма перспективными, так как объективно обеспечивают более надежное воспламенение смеси. Однако вследствие усложнения технологии производства они имеют и более высокую цену.
Рабочая температура свечи
Это температура рабочей части свечи при данном режиме двигателя. На всех режимах работы мотора она должна лежать в пределах от 500 до 900 градусов Цельсия. Как бы не различались тепловые потоки, бушующие в камере сгорания при пуске, работе на холостом ходу и режиме полной мощности, температура свечи не должна выходить из указанного поля допуска. Так как понижение температуры приведет к образованию нагара на изоляторе, способного шунтировать («закоротить») межэлектродный зазор и вызвать перебои в искрообразовании. А при повышении возникнет калильное зажигание.
Этот неуправляемый процесс способен полностью нарушить строго согласованный рабочий цикл двигателя и резко снизить его мощность. Помимо этого повышение средней температуры электродов сокращает срок службы самой свечи.
Тепловая характеристика свечи
Это зависимость температуры теплового конуса изолятора и центрального электрода (рабочей температуры свечи) от режима работы двигателя. Для увеличения рабочей температуры теплового конуса увеличивают его длину, однако выше 900 градусов разогревать конус нельзя, так как при этом возникает калильное зажигание.
Исходя из тепловой характеристики все свечи можно условно поделить на «горячие» и «холодные».
«Горячие» свечи предназначены для применения на двигателях, где необходимо достижение температуры самоочищения от нагара при относительно небольших тепловых нагрузках. Свечи, «горячее» положенных для данного двигателя, будут вызывать калильное зажигание.
«Холодные» свечи используются когда предусмотрен нагрев меньше температуры калильного зажигания при максимальной мощности двигателя. Свечи «холодные» для данного двигателя не будут достигать температуры самоочищения от нагара и перестанут работать через короткий промежуток времени.
Технологии «двойного металла»
Казалось бы, что еще нового можно привнести в конструкцию свечи? Оказывается – очень многое. На самом деле свеча имеет гораздо более сложное «внутреннее строение», чем принято считать.
В настоящее время многими производителями освоено производство свечей с составными, биметаллическими центральными электродами. По внешнему виду они ничем не отличаются от обычных – центральный электрод вроде бы также выполнен из хромоникелевого сплава. Но внутри — медь, теплопроводность которой заметно выше. Это позволяет улучшить процесс самоочистки от нагара и повысить защиту от перегрева. Диапазон рабочих температур у них значительно расширен, поэтому они получили название «термоэластик».
«Термоэластичные» свечи способны достигать нижнего температурного предела тепловой характеристики при наименьшей эффективной мощности, развиваемой двигателем.
Кроме того, применение биметаллических электродов снижает термонагруженность свечи, благодаря чему значительно увеличивается срок службы. Кстати, биметаллическим может быть не только центральный, но и боковой электрод, что еще больше расширяет температурный диапазон работы свечи.
А еще?
Появление особо форсированных моторов с турбонаддувом заставило искать материалы с более высокой эрозионной стойкостью, чем хромоникелевые сплавы. В результате появились свечи с центральным электродом из платиновых или иридиевых сплавов. По температурным характеристикам такие модели не имеют преимуществ перед обычными, вот только служить они будут как минимум в 2 раза дольше биметаллических, а цена их в 2—3 раза выше.
Чего ждать от нагара?
По образующемуся нагару происходит утечка энергии на корпус, значительно ослабляющая мощность электрической дуги между центральным и боковым электродами свечи (т.е. искру). Может случиться, что нагар полностью заполнит пространство между электродами, образуя электропроводный мостик, что полностью выведет свечу из строя. В большинстве случаев количество отложений, достаточное для потери свечей работоспособности, возникает при неисправности системы питания и неверно выставленном угле опережения зажигания. Если вы обнаружили, что свечи серьезно «закоптились», не пытайтесь отмачивать их в бензине или ацетоне с тем, чтобы затем очистить щеткой. Дело в том, что на поверхности электродов большинства современных свечей производится напыление благородных металлов. Таким образом, проводя вышеуказанные процедуры, вы буквально обдерете свечу, как липку, что только ухудшит ее характеристики. Кроме того, вы рискуете изменить величину искрового промежутка, чем окончательно нарушите ее работу.Если уж по каким-то причинам нет возможности приобрести новый комплект свечей (что является самым разумным решением), то просто на время немного прикрутите винт токсичности (совет подходит только для карбюраторных двигателей) в сторону обеднения смеси. После пробега 50—100 километров нагар самоликвидируется, если только причина его возникновения не кроется в нарушении нормальной работы какой-либо из систем двигателя.
О цвете и запахе
Срок службы правильно подобранной свечи во многом зависит не только от ее конструкции, но и от исправности систем питания, зажигания, а также деталей самого двигателя.
Ну а сами свечи зажигания вполне можно отнести к уникальным деталям, по внешнему виду которых можно судить о неисправностях тех или иных систем силового агрегата. Итак, переходим непосредственно к цветам отложений.
Светло-серый или светло-коричневый может быть вызван наличием небольшого количества отложений продуктов сгорания, заметных также на боковых поверхностях электродов. Эрозия практически отсутствует. Значит, двигатель и все его системы работают нормально, и в топливном баке у вас залит качественный бензин.
Черный свидетельствует о том, что на каких-то режимах двигателя система питания переобогащает топливовоздушную смесь. Она не сгорает полностью и образует большое количество копоти.
При загрязнении топливом изолятор и электроды свечи покрыты влажными отложениями черного цвета, а свеча пахнет бензином. Кроме того, причиной подобного явления может стать нестабильная работа системы зажигания, приводящая к сбоям искрообразования, а также использование чрезмерно «холодной» свечи.
Если электроды и изолятор свечи покрыты шлаком, имеющим маслянистый блеск, то можно сделать вывод о загрязнении свечи маслом. При длительной эксплуатации такой свечи, и не устраняя причину, можно получить полностью закоксованые продуктами сгорания масла изолятор и электрод. К этому приводит попадание масла в камеру сгорания, которое может быть вызвано износом маслосъемных колпачков, направляющих втулок клапанов, маслосъемных поршневых колец.
Иные, не так часто встречающиеся, но все же возможные причины — подтекание тормозной жидкости через поврежденную диафрагму вакуумного усилителя и просачивание во впускной коллектор трансмиссионной жидкости через мембрану вакуум-корректора (для машин с автоматической КПП). Чтобы уточнить причину, необходимы дополнительные диагностические методы. Возможна такая картина и на первых километрах пробега при обкатке нового двигателя или после ремонта, когда кольца еще не приработались.
Если в бак вашего автомобиля регулярно попадает этилированный бензин, то неизбежно отложение свинца на поверхности изолятора и электродов. Их поверхность покрывается пористыми отложениями, обладающими резким запахом сероводорода. Цвет этих отложений зависит от видов применяемых в бензине присадок и может изменяться от грязно-белого до темно-коричневого. Как показывает практика, срок службы свечей при использовании этилированного бензина сокращается как минимум вдвое.
Износ и остекленение
В ряде случаев происходит износ свечи. Изолятор имеет нормальный цвет, а кромки бокового и центрального электродов скруглены в результате эрозионного износа. Электродный зазор недопустимо увеличен. Такая свеча гарантирует проблемы при запуске двигателя, особенно в холодное время года, и увеличение расходов на топливо. Причина одна — несвоевременная проверка и замена свечей. Выгоревшие или сильно корродированные электроды, выгоревший «изъязвленный» изолятор — симптомы перегрева свечи. Причина — слишком низкое калильное число, неправильная установка зажигания, низкооктановый бензин. Менее вероятны, но возможны и другие причины — слишком бедная смесь, зависание клапана, плохое охлаждение и перегрев двигателя. Результат в любом случае один — калильное зажигание и сильная детонация. Если вы эксплуатируете автомобиль преимущественно в тяжелых условиях, поставьте более «холодные» свечи.
Если вы часто допускаете перегазовки и «кик-дауны», то у вас есть все шансы узнать, что такое остекленение свечи. Поверхность изолятора приобретает желтоватый цвет с глянцевым блеском. Образование глазури происходит из-за быстрого повышения температуры в камере сгорания в момент резкого нажатия на педаль газа. При разогреве находящиеся на поверхности изолятора отложения плавятся, образуя электропроводное стекловидное покрытие. В результате возникают сбои искрообразования, особенно на высоких оборотах двигателя. В большинстве случаев восстановлению такие свечи не подлежат.
Причины калильного зажигания и детонации
При перегреве электродов и изолятора возникает калильное зажигание. Следствием перегрева является оплавление электродов. Как правило, причиной перегрева служит неверный выбор типа свечи (более горячей, чем требуется). Если же свеча выбрана правильно, то следует искать неисправность в системе питания. Возможно, смесь переобеднена по причине нарушения регулировок карбюратора или неисправности одного из датчиков (на двигателях с впрыском топлива), как правило — ДМРВ. Также необходимо убедиться в отсутствии подсоса постороннего воздуха во впускной коллектор и проверить регулировку клапанов, так как неверно установленный угол опережения зажигания тоже может служить причиной перегрева свечей.
При использовании низкооктанового бензина, а также при нарушении регулировки зазора между электродами и слишком раннего зажигания может возникать детонация. Как следствие трескается или даже выкрашивается тепловой конус свечи. Гораздо большую опасность детонация имеет для поршневой группы и может послужить причиной прогорания поршней. Определить наличие детонации можно по повышенной вибрации двигателя и регулярному «постреливанию» из выхлопной трубы на холостом ходу (не путать с «вытраиванием» двигателя).
Чуть-чуть о ресурсе
Современные свечи зажигания при эксплуатации на полностью исправных и отрегулированных двигателях должны в соответствии с ОСТ 37. 003 081 бесперебойно работать в течение 30 тыс. км пробега для классической и 20 тыс. км для электронной системы зажигания. По мнению специалистов, фактический ресурс примерно вдвое выше, но труднодостижим из-за необходимости идеальных условий эксплуатации свечей, которые возможны не всегда. Однако с учетом прогресса в области новых технологий ресурс современных свечей, при условии исправности всех систем двигателя, составляет в среднем 50 тыс. км.
Безусловно, выбирая свечи, необходимо руководствоваться не только требуемыми характеристиками, но и здравым смыслом. Ведь если вы являетесь владельцем ВАЗовской «классики», двигатель которой является архаизмом во всех отношениях, то ставить свечи по $10—20 за штуку по меньшей мере неразумно. И наоборот, трудно представить себе владельца Lexus, покупающего дешевые свечи с ресурсом не более 20 тыс. км.
kammikadze.ru